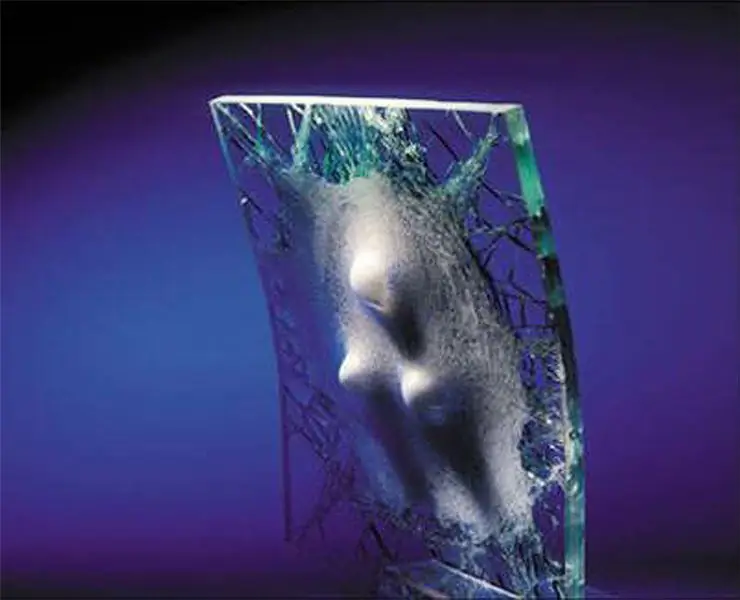
Pojazdy wojskowe tradycyjnie były wykonywane z ciężkiej, drogiej, ale bardzo wytrzymałej stali pancernej. Jako nienośne zabezpieczenie pojazdów bojowych coraz częściej stosuje się nowoczesne ceramiczne materiały kompozytowe. Główne zalety takich materiałów to znacznie niższy koszt, lepsza ochrona oraz redukcja wagi o ponad połowę. Rozważmy nowoczesne podstawowe materiały ceramiczne stosowane obecnie do ochrony balistycznej
Ze względu na odporność na bardzo wysokie temperatury, znacznie wyższe od metali, twardość, najwyższą wytrzymałość właściwą i sztywność właściwą, ceramika jest szeroko stosowana do produkcji okładzin do silników, elementów rakiet, krawędzi tnących narzędzi, specjalnych przezroczystych i nieprzezroczyste tarcze, które oczywiście należą do priorytetowych obszarów rozwoju systemów wojskowych. Jednak w przyszłości zakres jej stosowania powinien znacznie się poszerzyć, gdyż w ramach prac badawczo-rozwojowych prowadzonych w wielu krajach świata poszukuje się nowych sposobów zwiększania plastyczności, odporności na pękanie i innych pożądanych właściwości mechanicznych m.in. łączenie bazy ceramicznej z włóknami wzmacniającymi w tzw. osnowie ceramicznej materiały kompozytowe (KMKM). Ponadto nowe technologie produkcyjne pozwolą na masową produkcję bardzo trwałych, wysokiej jakości przezroczystych produktów o skomplikowanych kształtach i dużych rozmiarach z materiałów przepuszczających fale widzialne i podczerwone. Ponadto tworzenie nowych konstrukcji z wykorzystaniem nanotechnologii umożliwi uzyskanie materiałów trwałych i lekkich, odpornych na przegrzanie, chemoodpornych, a jednocześnie praktycznie niezniszczalnych. Ta kombinacja właściwości jest dziś uważana za wzajemnie wykluczającą się, a przez to bardzo atrakcyjną dla zastosowań wojskowych.
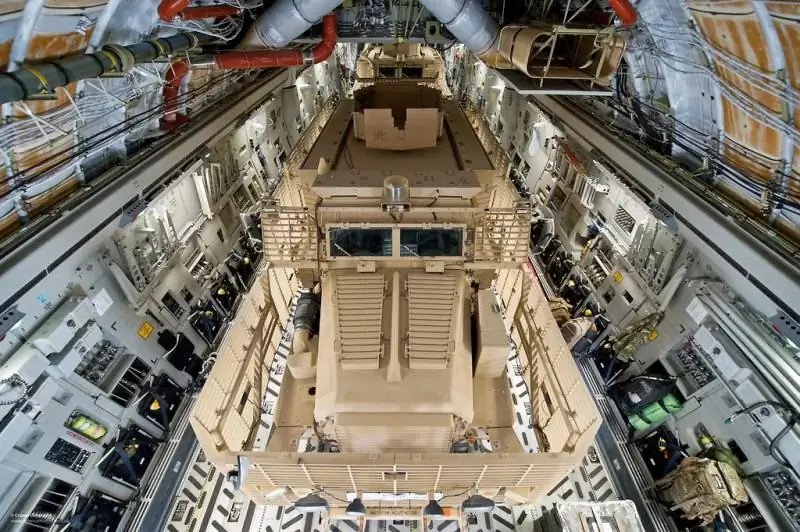
Materiały kompozytowe na osnowie ceramicznej (KMKM)
Podobnie jak ich polimerowe analogi, CMC składają się z substancji podstawowej, zwanej matrycą, oraz wypełniacza wzmacniającego, którym są cząstki lub włókna innego materiału. Włókna mogą być ciągłe lub dyskretne, zorientowane losowo, ułożone pod precyzyjnymi kątami, splecione w specjalny sposób w celu uzyskania zwiększonej wytrzymałości i sztywności w danych kierunkach lub równomiernie rozłożone we wszystkich kierunkach. Jednak bez względu na kombinację materiałów lub orientację włókien, wiązanie między osnową a elementem wzmacniającym ma kluczowe znaczenie dla właściwości materiału. Ponieważ polimery są mniej sztywne niż materiał, który je wzmacnia, wiązanie między matrycą a włóknami jest zwykle wystarczająco silne, aby materiał był odporny na zginanie jako całość. Jednak w przypadku CMCM, osnowa może być sztywniejsza niż włókna wzmacniające, tak że siła wiązania, podobnie zoptymalizowana w celu umożliwienia lekkiej zmiany lokalizacji włókna i osnowy, pomaga na przykład pochłaniać energię uderzenia i zapobiegać rozwojowi pęknięć w przeciwnym razie doprowadziłoby to do kruchego zniszczenia i rozszczepienia. To sprawia, że CMCM jest znacznie bardziej lepki w porównaniu z czystą ceramiką, a to jest najważniejsza z właściwości mocno obciążonych części ruchomych, np. części silników odrzutowych.
Lekkie i gorące łopatki turbiny
W lutym 2015 r. GE Aviation ogłosiło pomyślne testy tego, co nazywa „pierwszym na świecie niestatycznym zestawem CMC do silnika lotniczego”, chociaż firma nie ujawniła materiałów użytych do budowy matrycy i materiału wzmacniającego. Mowa o łopatkach turbiny niskiego ciśnienia w eksperymentalnym modelu silnika turbowentylatorowego F414, którego opracowanie ma na celu dalsze potwierdzenie zgodności materiału z deklarowanymi wymaganiami do pracy przy dużych obciążeniach udarowych. To działanie jest częścią programu demonstracyjnego demonstracji samodostosowujących się silników nowej generacji (Adaptive Engine Technology Demonstrator, AETD), w ramach którego GE współpracuje z Laboratorium Badawczym Sił Powietrznych Stanów Zjednoczonych. Celem programu AETD jest dostarczenie kluczowych technologii, które mogłyby być zaimplementowane w silnikach myśliwców szóstej generacji, a od połowy lat dwudziestych w silnikach samolotów piątej generacji, takich jak F-35. Silniki adaptacyjne będą w stanie dostosować swój wzrost ciśnienia i współczynnik obejścia w locie, aby uzyskać maksymalny ciąg podczas startu i walki lub maksymalne zużycie paliwa w trybie lotu przelotowego.
Firma podkreśla, że wprowadzenie obracających się części wykonanych z CMC do „najgorętszych i najbardziej obciążonych” części silnika odrzutowego stanowi istotny przełom, ponieważ wcześniej technologia pozwalała na wykorzystanie CMC tylko do produkcji części stacjonarnych, np. wysokociśnieniowa osłona turbiny. Podczas testów łopatki turbiny KMKM w silniku F414 przeszły 500 cykli - od biegu jałowego do ciągu startowego iz powrotem.
Łopatki turbiny są znacznie lżejsze niż konwencjonalne łopatki ze stopu niklu, dzięki czemu metalowe tarcze, do których są przymocowane, są mniejsze i lżejsze.
„Przejście ze stopów niklu na obrotową ceramikę wewnątrz silnika to naprawdę duży krok naprzód. Ale to czysta mechanika”- powiedział Jonathan Blank, szef CMC i spoiw polimerowych w GE Aviation. - Lżejsze ostrza wytwarzają mniejszą siłę odśrodkową. Oznacza to, że możesz obkurczać tarczę, łożyska i inne części. KMKM umożliwiło dokonanie rewolucyjnych zmian w konstrukcji silnika odrzutowego”.
Celem programu AETD jest zmniejszenie jednostkowego zużycia paliwa o 25%, zwiększenie zasięgu lotu o ponad 30% i zwiększenie maksymalnego ciągu o 10% w porównaniu z najbardziej zaawansowanymi myśliwcami 5. generacji. „Jednym z największych wyzwań przy przechodzeniu od statycznych elementów CMC do elementów wirujących jest pole naprężeń, w którym muszą działać”, powiedział Dan McCormick, kierownik programu Advanced Combat Engine w GE Aviation. Jednocześnie dodał, że testowanie silnika F414 przyniosło ważne wyniki, które zostaną wykorzystane w silniku cyklu adaptacyjnego. „Niskociśnieniowa łopatka turbiny CMC waży trzy razy mniej niż metalowa łopatka, którą zastępuje, dodatkowo w drugim trybie ekonomicznym nie ma potrzeby chłodzenia łopatki CMC powietrzem. Łopata będzie teraz bardziej wydajna aerodynamicznie, ponieważ nie ma potrzeby pompowania przez nią całego chłodzącego powietrza.”
Materiały KMKM, w które firma zainwestowała ponad miliard dolarów od momentu rozpoczęcia prac nad nimi na początku lat 90., wytrzymują temperatury o setki stopni wyższe niż tradycyjne stopy niklu i wyróżniają się wzmocnieniem włóknami z węglika krzemu w osnowie ceramicznej, co zwiększa jego udarność i odporność na pękanie.
Wydaje się, że GE wykonało dość ciężką pracę nad tymi łopatkami turbiny. Rzeczywiście, niektóre właściwości mechaniczne KMKM są bardzo skromne. Na przykład wytrzymałość na rozciąganie jest porównywalna z wytrzymałością na rozciąganie miedzi i tanich stopów aluminium, co nie jest zbyt dobre w przypadku części poddawanych dużym siłom odśrodkowym. Ponadto wykazują one niewielkie odkształcenie przy zerwaniu, to znaczy bardzo nieznacznie wydłużają się przy zerwaniu. Wydaje się jednak, że te niedociągnięcia zostały przezwyciężone, a niska waga tych materiałów zdecydowanie przyczyniła się do zwycięstwa nowej technologii.
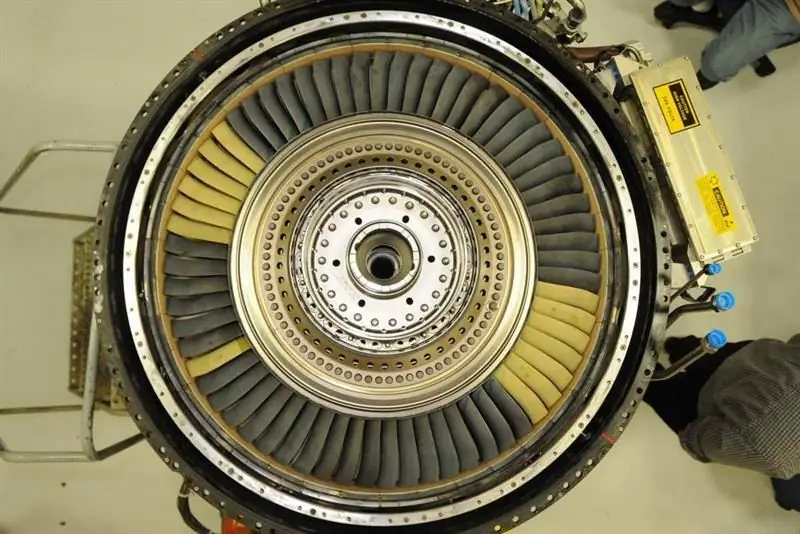
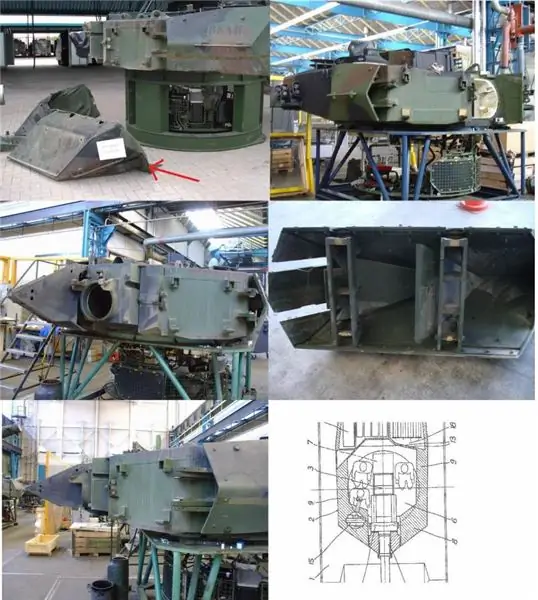
Pancerz modułowy z nanoceramiką do czołgu LEOPARD 2
Wkład pancerza kompozytowego
Chociaż technologie ochrony, które są kombinacją warstw metalu, kompozytów polimerowych wzmacnianych włóknami i ceramiki, są dobrze ugruntowane, przemysł nadal opracowuje coraz bardziej złożone materiały kompozytowe, ale wiele szczegółów tego procesu jest starannie ukrywanych. Morgan Advanced Materials jest dobrze znany w branży, ogłaszając nagrodę na konferencji Armored Vehicles XV w Londynie w zeszłym roku za technologię obronną SAMAS. Według Morgan, ochrona SAMAS szeroko stosowana w pojazdach armii brytyjskiej to materiał kompozytowy wzmocniony materiałami takimi jak S-2 Glass, E-Glass, aramid i polietylen, a następnie formowany w arkusze i utwardzany pod wysokim ciśnieniem: „Włókna można łączyć z hybrydowymi materiałami ceramiczno-metalowymi, aby spełnić specjalne wymagania projektowe i eksploatacyjne.”
Według Morgana, pancerz SAMAS o łącznej grubości 25 mm, używany do produkcji kapsuł ochronnych załogi, może zmniejszyć masę lekkich pojazdów chronionych o ponad 1000 kg w porównaniu z pojazdami ze stalową kapsułą. Inne korzyści to łatwiejsze naprawy przy grubości mniejszej niż 5 mm oraz naturalne właściwości wykładziny przeciwodpryskowej tego materiału.
Wyraźny postęp spinelu
Według Laboratorium Badawczego Marynarki Wojennej Stanów Zjednoczonych, rozwój i produkcja przezroczystych materiałów na bazie tlenku magnezowo-aluminiowego (MgAI2O4), znanych również pod wspólną nazwą sztucznych spineli, przeżywa boom. Spinele od dawna znane są nie tylko ze swojej wytrzymałości - spinel o grubości 0,25” ma te same właściwości balistyczne co szkło kuloodporne 2,5” - ale także z trudności w wykonywaniu dużych części o jednolitej przezroczystości. Jednak grupa naukowców z tego laboratorium wymyśliła nowy proces niskotemperaturowego spiekania w próżni, który pozwala uzyskać części o wymiarach ograniczonych jedynie wielkością prasy. Jest to duży przełom w porównaniu z poprzednimi procesami produkcyjnymi, które rozpoczęły się procesem topienia oryginalnego proszku w tyglu do topienia.
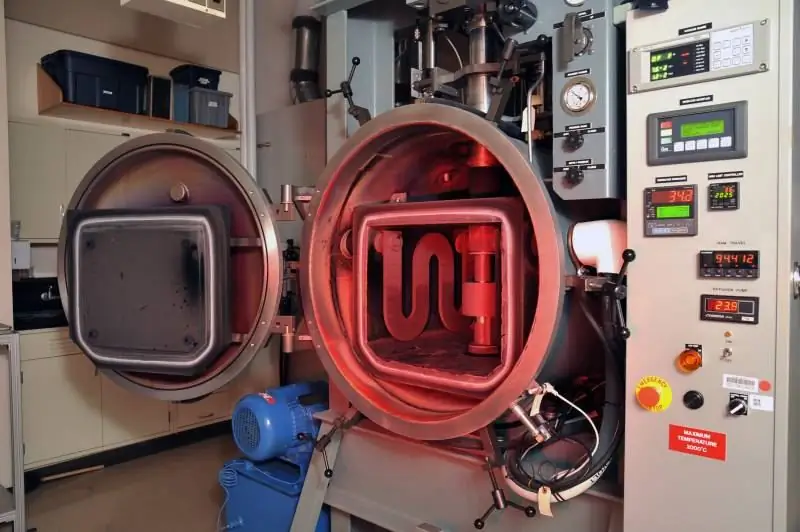
Jednym z sekretów nowego procesu jest równomierne rozprowadzanie dodatku do spiekania z fluorku litu (LiF), który topi i smaruje ziarna spinelu, dzięki czemu można je równomiernie rozprowadzić podczas spiekania. Zamiast mieszania na sucho sproszkowanego fluorku litu i spinelu, laboratorium opracowało metodę równomiernego powlekania cząstek spinelu fluorkiem litu. Pozwala to znacznie zmniejszyć zużycie LiF i zwiększyć przepuszczalność światła do 99% wartości teoretycznej w zakresie widzialnym i średniej podczerwieni widma (0,4-5 mikronów).
Nowy proces, który pozwala na produkcję optyki w różnych kształtach, w tym arkuszy, które wygodnie dopasowują się do skrzydeł samolotu czy drona, uzyskał licencję nienazwanej firmy. Możliwe zastosowania spinelu obejmują szkło pancerne ważące mniej niż połowę masy istniejącego szkła, maski ochronne dla żołnierzy, optykę do laserów nowej generacji oraz okulary z czujnikami wielospektralnymi. Przy masowej produkcji np. odpornych na pękanie okularów do smartfonów i tabletów, koszt produktów spinelowych znacznie się obniży.
PERLUCOR - nowy kamień milowy w systemach ochrony pocisków i zużycia
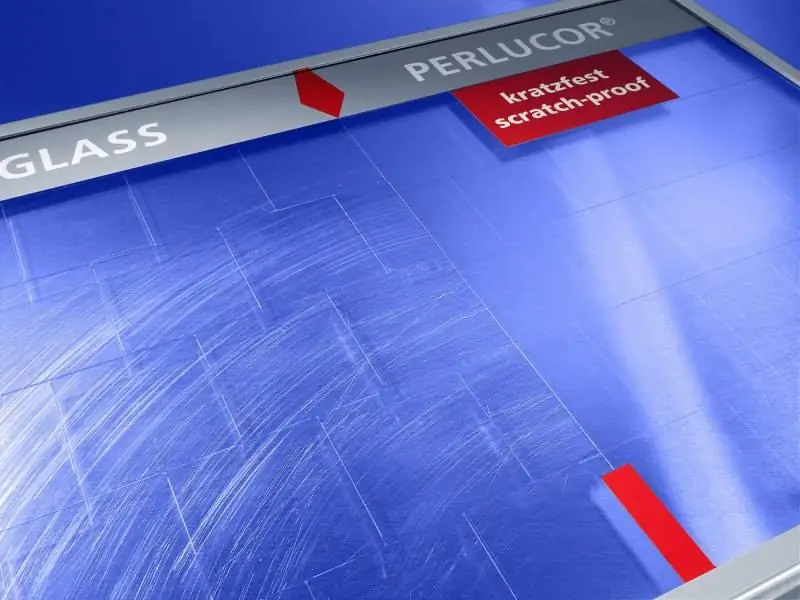
CeramTec-ETEC opracował kilka lat temu przezroczystą ceramikę PERLUCOR, która ma dobre perspektywy zarówno dla zastosowań obronnych, jak i cywilnych. Doskonałe właściwości fizyczne, chemiczne i mechaniczne PERLUCOR były głównymi przyczynami udanego wejścia tego materiału na rynek.
PERLUCOR ma względną przezroczystość ponad 90%, jest od trzech do czterech razy mocniejszy i twardszy niż zwykłe szkło, odporność cieplna tego materiału jest około trzykrotnie wyższa, co pozwala na jego stosowanie w temperaturach do 1600°C, również ma wyjątkowo wysoką odporność chemiczną, co pozwala na stosowanie go ze stężonymi kwasami i zasadami. PERLUCOR posiada wysoki współczynnik załamania światła (1, 72), co umożliwia wytwarzanie obiektywów optycznych i elementów optycznych o miniaturowych wymiarach, czyli uzyskiwanie urządzeń o dużym powiększeniu, którego nie można osiągnąć przy użyciu polimerów lub szkła. Płytki ceramiczne PERLUCOR mają standardowy format 90x90 mm; jednak CeramTec-ETEC opracował technologię produkcji arkuszy o skomplikowanych kształtach w oparciu o ten format według specyfikacji klienta. Grubość paneli może w szczególnych przypadkach wynosić dziesiąte części milimetra, ale z reguły jest to 2-10 mm.
Rozwój lżejszych i cieńszych systemów przejrzystej ochrony rynku obronnego postępuje w szybkim tempie. Istotny wkład w ten proces ma przezroczysta ceramika firmy SegamTes, która wchodzi w skład systemów ochronnych wielu producentów. Podczas testów zgodnie ze STANAG 4569 lub APSD redukcja masy jest rzędu 30-60 procent.
W ostatnich latach ukształtował się kolejny kierunek rozwoju technologii opracowanych przez SegatTes-ETEC. Okna pojazdów, zwłaszcza na skalistych i pustynnych obszarach, takich jak Afganistan, są podatne na uderzenia kamieni i zarysowania spowodowane ruchem piór wycieraczek na piaszczystej, zakurzonej przedniej szybie. Zmniejszeniu ulegają również właściwości balistyczne szkieł kuloodpornych, które zostały uszkodzone przez uderzenia kamieni. Podczas działań wojennych pojazdy z uszkodzoną szybą narażone są na poważne i nieprzewidywalne zagrożenia. SegamTes-ETEC opracował prawdziwie innowacyjne i oryginalne rozwiązanie ochrony szkła przed tego typu zużyciem. Cienka warstwa (<1 mm) powłoki ceramicznej PERLUCOR na powierzchni szyby pomaga skutecznie przeciwdziałać takim uszkodzeniom. Ta ochrona jest również odpowiednia dla instrumentów optycznych, takich jak teleskopy, soczewki, urządzenia na podczerwień i inne czujniki. Płaskie i zakrzywione soczewki wykonane z przezroczystej ceramiki PERLUCOR przedłużają żywotność tego bardzo cennego i czułego sprzętu optycznego.
CeramTec-ETEC z powodzeniem zaprezentował na targach DSEI 2015 w Londynie panel do drzwi ze szkła kuloodpornego oraz panel ochronny odporny na zarysowania i kamienie.
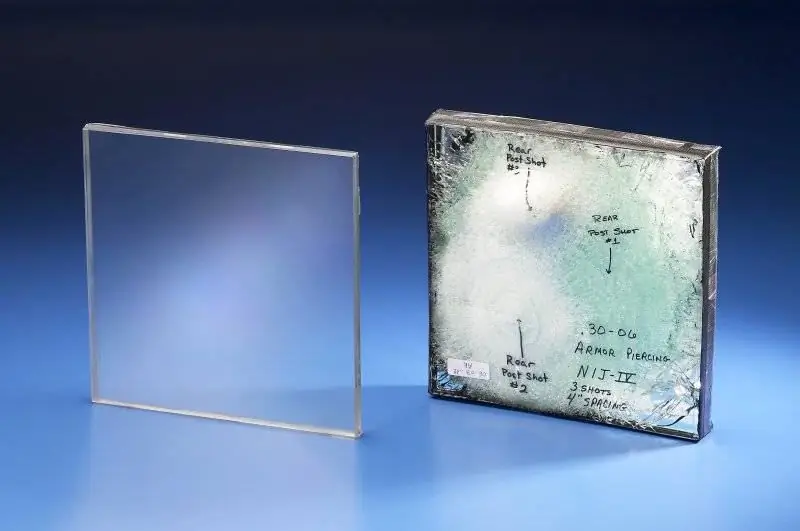
Trwała i elastyczna nanoceramika
Elastyczność i sprężystość nie są cechami nieodłącznymi od ceramiki, ale zespół naukowców pod kierownictwem profesora materiałoznawstwa i mechaniki Julii Greer z Kalifornijskiego Instytutu Technologicznego podjął ten problem. Naukowcy opisują nowy materiał jako „twarde, lekkie, regenerowalne trójwymiarowe nanosieci ceramiczne”. Jest to jednak ta sama nazwa dla artykułu opublikowanego przez Greer i jej uczniów w czasopiśmie naukowym kilka lat temu.
To, co kryje się pod spodem, najlepiej ilustruje sześcian nanosieci z tlenku glinu o wielkości kilkudziesięciu mikronów, zrobiony pod mikroskopem elektronowym. Pod wpływem obciążenia kurczy się o 85%, a po usunięciu powraca do pierwotnego rozmiaru. Eksperymenty przeprowadzono również z sieciami składającymi się z rurek o różnej grubości, przy czym najcieńsze rurki są najmocniejsze i najbardziej elastyczne. Przy grubości ścianki rurki wynoszącej 50 nanometrów sieć zapadła się, a przy grubości ścianki wynoszącej 10 nanometrów powróciła do swojego pierwotnego stanu - przykład tego, jak efekt rozmiaru zwiększa wytrzymałość niektórych materiałów. Teoria wyjaśnia to faktem, że wraz ze spadkiem rozmiaru proporcjonalnie maleje liczba defektów w materiałach sypkich. Dzięki tej architekturze sieci pustych rur 99,9% objętości sześcianu to powietrze.
Zespół profesora Greera tworzy te maleńkie struktury, uruchamiając proces podobny do drukowania 3D. Każdy proces rozpoczyna się od pliku CAD, który napędza dwa lasery, które „malują” strukturę w trzech wymiarach, utwardzając polimer w punktach, w których wiązki wzmacniają się nawzajem w fazie. Nieutwardzony polimer wypływa z utwardzonej siatki, która teraz staje się podłożem tworząc ostateczną strukturę. Następnie naukowcy nakładają tlenek glinu na podłoże za pomocą metody, która dokładnie kontroluje grubość powłoki. Na koniec końce sieci są cięte w celu usunięcia polimeru, pozostawiając jedynie sieć krystaliczną pustych rurek z tlenku glinu.
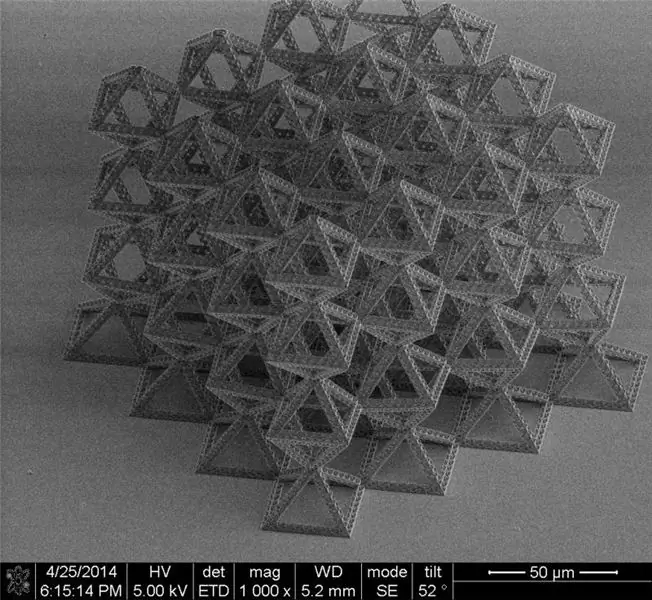
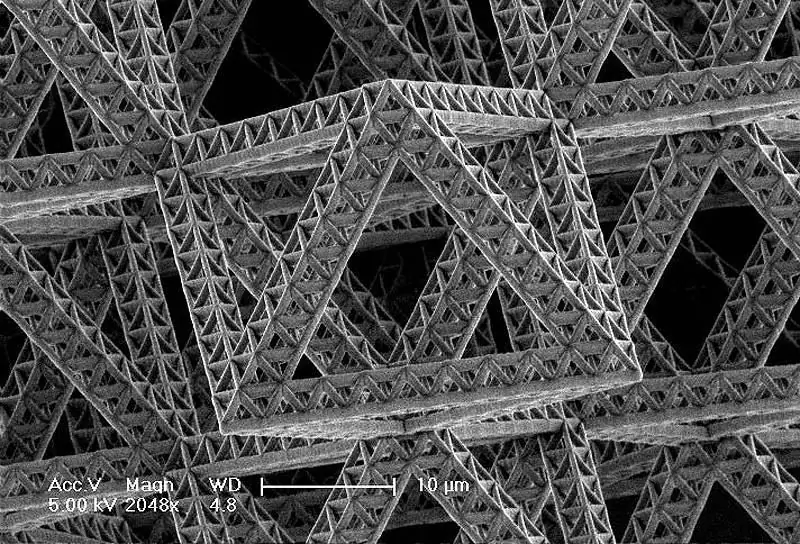
Wytrzymałość stali, ale waży jak powietrze
Potencjał takich „inżynieryjnych” materiałów, które objętościowo są głównie powietrzem, ale mniej wytrzymałymi jak stal, jest ogromny, ale trudny do zrozumienia, więc profesor Greer podał kilka uderzających przykładów. Pierwszy przykład to balony, z których wypompowywany jest hel, ale jednocześnie zachowują swój kształt. Drugi, przyszły samolot, którego konstrukcja waży tyle, ile waży jego ręczny model. Co najbardziej zaskakujące, gdyby słynny most Golden Gate był wykonany z takich nanosiatek, wszystkie materiały potrzebne do jego budowy można by umieścić (poza powietrzem) na ludzkiej dłoni.
Tak jak ogromne zalety strukturalne tych twardych, lekkich i żaroodpornych materiałów nadających się do niezliczonych zastosowań wojskowych, ich z góry określone właściwości elektryczne mogą zrewolucjonizować magazynowanie i wytwarzanie energii: „Te nanostruktury są bardzo lekkie, stabilne mechanicznie, a jednocześnie ogromne pod względem wielkości powierzchni, czyli możemy wykorzystać w różnych aplikacjach typu elektrochemicznego.”
Należą do nich niezwykle wydajne elektrody do baterii i ogniw paliwowych, są cenionym celem dla autonomicznych zasilaczy, przenośnych i przenośnych elektrowni, a także prawdziwym przełomem w technologii ogniw słonecznych.
„Kryształy fotoniczne można również nazwać w tym względzie” - powiedział Greer. „Te struktury pozwalają manipulować światłem w taki sposób, że można je całkowicie uchwycić, co oznacza, że można zrobić znacznie wydajniejsze ogniwa słoneczne - przechwytuje się całe światło i nie ma utraty odbicia”.
„Wszystko to sugeruje, że połączenie efektu wielkości w nanomateriałach i elementach strukturalnych pozwala nam tworzyć nowe klasy materiałów o właściwościach, które nie były osiągalne” - powiedział profesor Greer z Europejskiej Organizacji Badań Jądrowych w Szwajcarii. „Największym wyzwaniem, przed którym stoimy, jest skalowanie i przejście z nanotechnologii do rozmiarów naszego świata”.
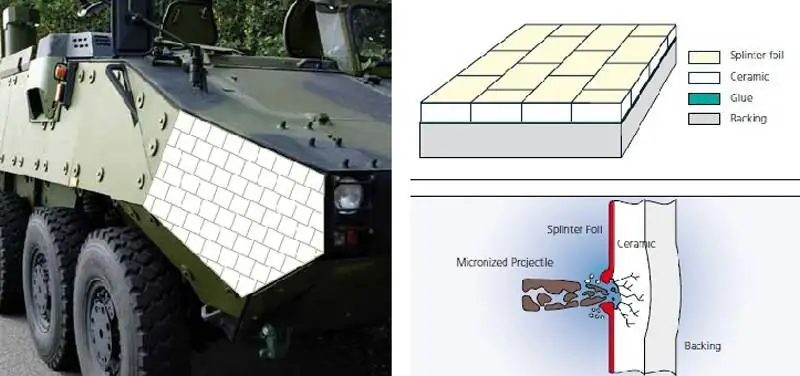
Przemysłowa przezroczysta ochrona ceramiczna
Firma IBD Deisenroth Engineering opracowała przezroczysty pancerz ceramiczny o właściwościach balistycznych porównywalnych z nieprzezroczystym pancerzem ceramicznym. Ten nowy przezroczysty pancerz jest o około 70% lżejszy od szkła pancernego i może być montowany w konstrukcje o takich samych właściwościach wielokrotnych uderzeń (zdolność do wytrzymania wielokrotnych uderzeń) jak pancerz nieprzezroczysty. Pozwala to nie tylko radykalnie zmniejszyć masę pojazdów z dużymi szybami, ale także zamknąć wszelkie luki balistyczne.
Aby uzyskać ochronę zgodnie ze STANAG 4569 Poziom 3, szkło kuloodporne ma gęstość powierzchniową około 200 kg/m2. Przy typowej powierzchni okna ciężarówki o powierzchni trzech metrów kwadratowych masa okularów kuloodpornych wyniesie 600 kg. Przy wymianie takich szkieł kuloodpornych na ceramikę IBD redukcja wagi wyniesie ponad 400 kg. Przezroczysta ceramika IBD to dalszy rozwój ceramiki IBD NANOTech. Firma IBD odniosła sukces w opracowaniu specjalnych procesów spajania, które są wykorzystywane do montażu płytek ceramicznych („przezroczysty pancerz mozaikowy”), a następnie laminowania tych zespołów w mocne warstwy strukturalne w celu utworzenia dużych paneli okiennych. Ze względu na wyjątkowe właściwości tego materiału ceramicznego możliwe jest wytwarzanie przezroczystych paneli pancernych o znacznie niższej wadze. Podkład, w połączeniu z laminatem Natural NANO-Fiber, dodatkowo poprawia właściwości balistyczne nowej przezroczystej ochrony dzięki większej absorpcji energii.
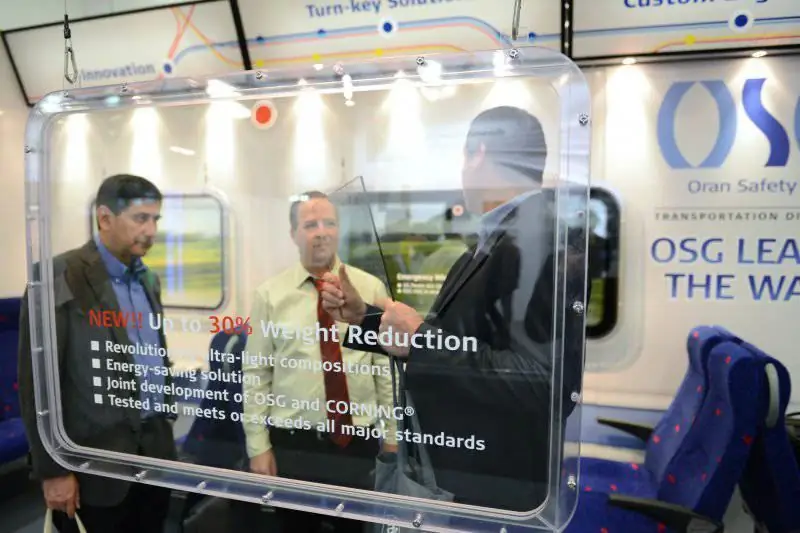
Izraelska firma OSG (Oran Safety Glass), odpowiadając na rosnący poziom niestabilności i napięć na całym świecie, opracowała szeroką gamę produktów ze szkła kuloodpornego. Są specjalnie zaprojektowane dla sektora obronnego i cywilnego, wojska, paramilitarnych, cywilnych zawodów wysokiego ryzyka, budownictwa i przemysłu motoryzacyjnego. Firma promuje na rynku następujące technologie: rozwiązania ochrony transparentnej, rozwiązania ochrony balistycznej, dodatkowe zaawansowane systemy opancerzenia transparentnego, okna cyfrowego widzenia, okna ewakuacyjne, okna ceramiczne z technologią kolorowego wyświetlacza, zintegrowane systemy sygnalizacji świetlnej, osłony szklane odporne na wstrząsy, kamienie i wreszcie technologia antyodpryskowa ADI.
Przezroczyste materiały OSG są stale testowane w rzeczywistych sytuacjach: odpieranie ataków fizycznych i balistycznych, ratowanie życia i ochrona mienia. Wszystkie opancerzone przezroczyste materiały zostały stworzone zgodnie z najważniejszymi międzynarodowymi standardami.