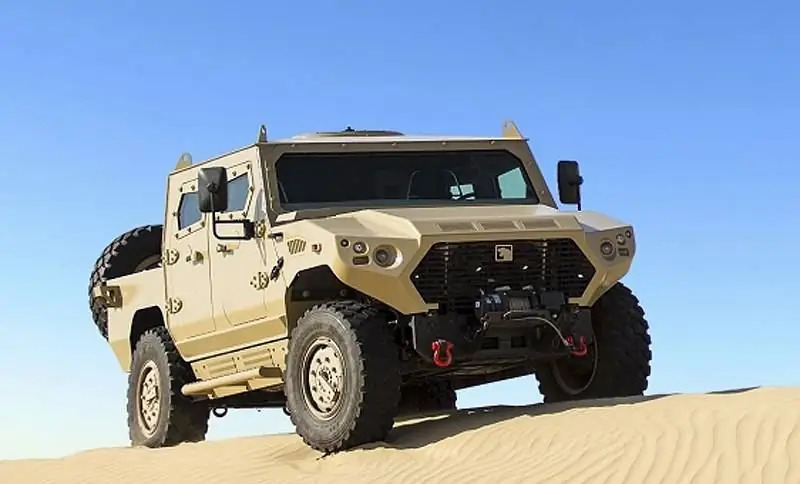
Zbroja jest o miliony lat starsza od ludzkości i została opracowana przede wszystkim w celu ochrony przed szczękami i pazurami. Możliwe, że krokodyle i żółwie mogą częściowo zainspirować ludzi do tworzenia elementów ochronnych. Wszystkie bronie wykorzystujące energię kinetyczną, czy to prehistoryczna maczuga, czy pocisk przeciwpancerny, są zaprojektowane do koncentracji dużej siły na niewielkim obszarze, jej zadaniem jest przebicie celu i zadanie mu maksymalnych obrażeń. W konsekwencji zadaniem pancerza jest zapobieganie temu poprzez odbijanie lub niszczenie środków atakujących i/lub rozpraszanie energii uderzenia na jak największym obszarze w celu zminimalizowania wszelkich uszkodzeń siły roboczej, systemów transportowych i konstrukcji, które chroni.
Współczesna zbroja zazwyczaj składa się z twardej warstwy zewnętrznej, która zatrzymuje, odchyla lub niszczy pocisk, warstwy pośredniej o bardzo wysokiej „pracy do zerwania” oraz lepkiej warstwy wewnętrznej, która zapobiega pęknięciom i odłamkom.
Stal
Stal, która stała się pierwszym materiałem szeroko stosowanym w tworzeniu pojazdów opancerzonych, wciąż jest poszukiwana, pomimo pojawienia się opancerzenia opartego na lekkich stopach aluminium i tytanu, ceramice, kompozytach z osnową polimerową, wzmocnionych włóknami szklanymi, aramidowymi oraz polietylen o ultrawysokiej masie cząsteczkowej, a także materiały kompozytowe z metalową osnową.
Wiele hut stali, w tym SSAB, nadal opracowuje wysokowytrzymałe stale do różnych zastosowań o znaczeniu krytycznym, takich jak dodatkowe poszycie. Gatunek stali pancernej ARM OX 600T, dostępny w grubościach 4-20 mm, jest dostępny z gwarantowaną twardością od 570 do 640 jednostek HBW (skrót od Hardness, Brinell, Wolfram; próba polegająca na prasowaniu kulki wolframowej o standardowej średnicy w próbkę materiału o znanej sile, następnie mierzy się średnicę uformowanego wgłębienia, następnie te parametry są podstawiane do wzoru, który pozwala uzyskać liczbę jednostek twardości).
SSAB podkreśla również znaczenie osiągnięcia właściwej równowagi twardości i wytrzymałości dla ochrony przed penetracją i rozerwaniem. Podobnie jak wszystkie stale, ARMOX 600T składa się z żelaza, węgla i wielu innych składników stopowych, w tym krzemu, manganu, fosforu, siarki, chromu, niklu, molibdenu i boru.
Istnieją ograniczenia dotyczące stosowanych technik wytwarzania, zwłaszcza jeśli chodzi o temperaturę. Stal ta nie jest przeznaczona do dodatkowej obróbki cieplnej, w przypadku podgrzania powyżej 170°C po dostawie SSAB nie może zagwarantować jej właściwości. Firmy, które mogą obejść tego rodzaju ograniczenia, prawdopodobnie przyciągną uwagę producentów pojazdów opancerzonych.
Inna szwedzka firma, Deform, oferuje formowane na gorąco elementy pancernej stali pancernej producentom pojazdów opancerzonych, zwłaszcza tym, którzy chcą poprawić ochronę pojazdów komercyjnych/cywilnych.
Jednoczęściowe zapory ogniowe Deform są instalowane w Nissanie PATROL 4x4, minibusie Volkswagen T6 TRANSPORTER i pick-upie Isuzu D-MAX, wraz z solidną podłogą z tego samego materiału. Proces formowania na gorąco opracowany przez Deform i stosowany w produkcji blach pozwala na zachowanie twardości 600 HBW.
Firma twierdzi, że może przywrócić właściwości wszystkich stali pancernych dostępnych na rynku, zachowując jednocześnie określony konstrukcyjnie kształt, podczas gdy powstałe części znacznie przewyższają tradycyjne konstrukcje spawane i częściowo zachodzące na siebie. W metodzie opracowanej przez Deform blachy są hartowane i odpuszczane po kuciu na gorąco. Dzięki temu procesowi możliwe jest uzyskanie trójwymiarowych kształtów, których nie można uzyskać przez formowanie na zimno bez obowiązkowych w takich przypadkach „spoin naruszających integralność punktów krytycznych”.
Blachy formowane na gorąco firmy Deform były stosowane w BAE Systems BVS-10 i CV90, a od początku lat 90. w wielu maszynach Kraus-Maffei Wegmann (KMW). Napływają zamówienia na produkcję trójwymiarowych płyt pancernych dla czołgu LEOPARD 2 oraz kilku płyt kształtowych dla pojazdów BOXER i PUMA, a także dla kilku pojazdów Rheinmetall, w tym ponownie BOXER, a także włazu do pojazdu WIESEL. Deform współpracuje również z innymi materiałami ochronnymi, w tym aluminium, kevlarem/aramidem i tytanem.
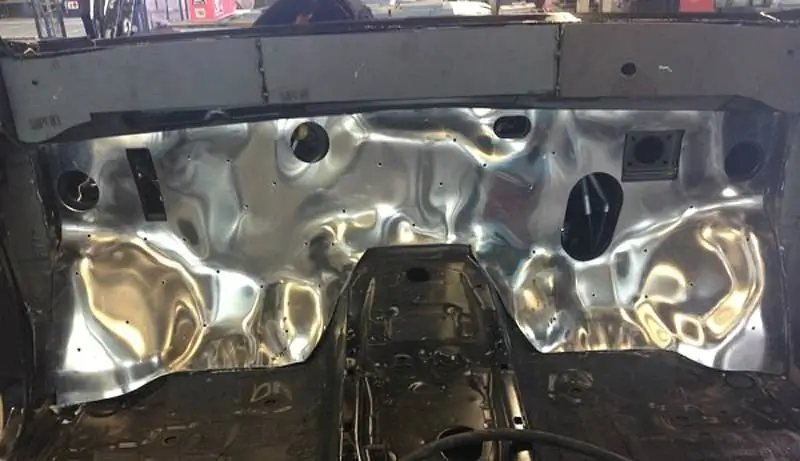
Postęp aluminium
Jeśli chodzi o pojazdy opancerzone, po raz pierwszy w produkcji transportera opancerzonego M113, który jest produkowany od 1960 roku, szeroko zastosowano aluminiowy pancerz. Był to stop oznaczony 5083, zawierający 4,5% magnezu i znacznie mniejsze ilości manganu, żelaza, miedzi, węgla, cynku, chromu, tytanu i innych. Chociaż 5083 dobrze zachowuje swoją wytrzymałość po spawaniu, nie jest to stop do obróbki cieplnej. Nie ma on tak dobrej odporności na pociski przeciwpancerne kalibru 7,62 mm, ale, jak potwierdziły oficjalne testy, powstrzymuje pociski przeciwpancerne kalibru 14,5 mm lepiej niż stal, przy jednoczesnym zmniejszeniu masy i dodaniu pożądanej wytrzymałości. Dla tego poziomu ochrony blacha aluminiowa jest grubsza i 9 razy mocniejsza od stali o niższej gęstości 265 r/cm3, co skutkuje zmniejszeniem masy konstrukcji.
Producenci pojazdów opancerzonych wkrótce zaczęli prosić o lżejsze, bardziej balistycznie silniejsze, spawalne i podatne na obróbkę cieplną pancerze aluminiowe, co doprowadziło do opracowania Alcana 7039, a później 7017, obu z wyższą zawartością cynku.
Podobnie jak w przypadku stali, tłoczenie i późniejszy montaż mogą negatywnie wpłynąć na właściwości ochronne aluminium. Podczas spawania strefy wpływu ciepła miękną, ale ich wytrzymałość zostaje częściowo przywrócona dzięki utwardzeniu podczas naturalnego starzenia. Struktura metalu zmienia się w wąskich strefach w pobliżu spoiny, tworząc duże naprężenia szczątkowe w przypadku błędów spawalniczych i/lub montażowych. W związku z tym techniki produkcyjne powinny je minimalizować, a ryzyko pęknięć korozyjnych naprężeniowych powinno być również zminimalizowane, zwłaszcza gdy oczekuje się, że maszyna będzie miała projektowany okres eksploatacji dłuższy niż trzy dekady.
Korozja naprężeniowa to proces pojawiania się i wzrostu pęknięć w środowisku korozyjnym, który ma tendencję do pogarszania się wraz ze wzrostem liczby pierwiastków stopowych. Powstawanie pęknięć i ich dalszy wzrost następuje w wyniku dyfuzji wodoru wzdłuż granic ziaren.
Określenie podatności na pękanie rozpoczyna się od wydobycia niewielkiej ilości elektrolitu z pęknięć i jego analizy. Testy korozji naprężeniowej o niskiej szybkości odkształcania są przeprowadzane w celu określenia, jak bardzo dany stop został zaatakowany. Następuje mechaniczne rozciąganie dwóch próbek (jednej w środowisku korozyjnym, a drugiej w suchym powietrzu) aż do uszkodzenia, a następnie porównuje się odkształcenie plastyczne w miejscu pęknięcia - im bardziej próbka jest rozciągana do zniszczenia, tym lepiej.
Podczas obróbki można poprawić odporność na pękanie korozyjne naprężeniowe. Na przykład, według Total Materia, która nazywa siebie „największą na świecie bazą danych materiałów”, Alcan 40-krotnie poprawił wydajność 7017 w przyspieszonych testach pękania korozyjnego naprężeniowego. Uzyskane wyniki pozwalają również na opracowanie metod ochrony antykorozyjnej stref konstrukcji spawanych, w których trudno uniknąć naprężeń szczątkowych. Trwają badania mające na celu udoskonalenie stopów w celu optymalizacji właściwości elektrochemicznych złączy spawanych. Prace nad nowymi stopami do obróbki cieplnej koncentrują się na poprawie ich wytrzymałości i odporności na korozję, podczas gdy prace nad stopami nieobrabialnymi cieplnie mają na celu usunięcie ograniczeń nałożonych przez wymagania spawalności. Najtwardsze materiały, które są opracowywane, będą o 50% mocniejsze niż najlepszy obecnie stosowany pancerz aluminiowy.
Stopy o niskiej gęstości, takie jak litowo-aluminiowe, oferują około 10% oszczędności masy w porównaniu z wcześniejszymi stopami o porównywalnej odporności na kule, chociaż wydajność balistyczna nie została jeszcze w pełni oceniona zgodnie z Total Materia.
Poprawiają się również metody spawania, w tym zrobotyzowane. Wśród rozwiązywanych zadań jest minimalizacja dopływu ciepła, stabilniejszy łuk spawalniczy dzięki usprawnieniu systemów zasilania energią i drutem, a także monitorowanie i sterowanie procesem przez systemy eksperckie.
Firma MTL Advanced Materials współpracowała z ALCOA Defense, renomowanym producentem aluminiowych płyt pancernych, aby opracować coś, co firma określa jako „niezawodny i powtarzalny proces formowania na zimno”. Firma zauważa, że stopy aluminium opracowane do zastosowań w pancerzach nie zostały zaprojektowane do formowania na zimno, co oznacza, że nowy proces powinien pomóc w uniknięciu typowych przyczyn awarii, w tym pękania. Według firmy ostatecznym celem jest umożliwienie projektantom maszyn zminimalizowania potrzeby spawania i zmniejszenia liczby części. Firma podkreśla, że zmniejszenie objętości spawania zwiększa wytrzymałość konstrukcji i ochronę załogi przy jednoczesnym obniżeniu kosztów produkcji. Zaczynając od sprawdzonego stopu 5083-H131, firma opracowała proces formowania na zimno części z kątem zgięcia 90 stopni wzdłuż i w poprzek ziaren, a następnie przeszła do bardziej złożonych materiałów, na przykład stopów 7017, 7020 i 7085, osiągając również dobre wyniki.
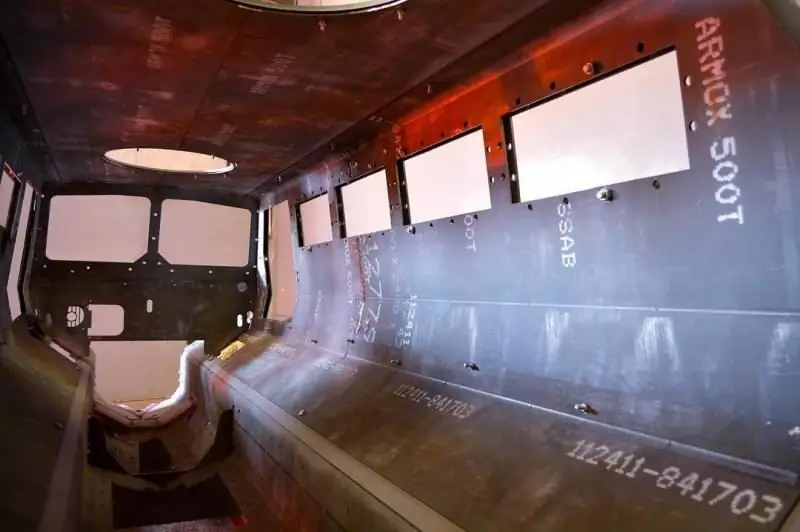
Ceramika i kompozyty
Kilka lat temu firma Morgan Advanced Materials ogłosiła opracowanie kilku systemów opancerzenia SAMAS, które składały się z połączenia zaawansowanej ceramiki i kompozytów strukturalnych. Linia produktów obejmuje pancerze na zawiasach, okładziny przeciwodłamkowe, kapsuły przeżywalności wykonane z kompozytów strukturalnych do wymiany metalowych kadłubów i ochrony modułów broni, zarówno zamieszkałych, jak i niezamieszkałych. Wszystkie mogą być dostosowane do konkretnych wymagań lub wykonane na zamówienie.
Zapewnia ochronę STANAG 4569 na poziomie 2-6, a także wydajność i oszczędność masy przy wielu uderzeniach (firma twierdzi, że systemy te ważą o połowę mniej niż podobne produkty stalowe), a także dostosowanie do określonych zagrożeń, platform i misji… Okładziny antyodpryskowe mogą być wykonane z płaskich paneli o wadze 12,3 kg dla pokrycia powierzchni 0,36 m2 (ok. 34 kg/m2) lub solidnych okuć o wadze 12,8 kg dla 0,55 m2 (ok. 23,2 kg/m2).
Według Morgan Advanced Materials dodatkowe opancerzenie przeznaczone do nowych i modernizacji istniejących platform oferuje te same możliwości przy o połowę mniejszej wadze. Opatentowany system zapewnia maksymalną ochronę przed szeroką gamą zagrożeń, w tym bronią małego i średniego kalibru, improwizowanymi urządzeniami wybuchowymi (IED) i granatami o napędzie rakietowym, a także wielozadaniową skutecznością.
Do modułów broni oferowany jest „półstrukturalny” system opancerzenia o dobrej odporności na korozję (oprócz zastosowań powietrznych i morskich), a wraz ze zmniejszeniem masy i zminimalizowaniem problemów ze środkiem ciężkości, w przeciwieństwie do stali, stwarza mniej problemów z kompatybilnością elektromagnetyczną.
Szczególnym problemem jest ochrona modułów uzbrojenia, ponieważ są one atrakcyjnym celem, gdyż ich wyłączenie drastycznie utrudnia załodze panowanie nad sytuacją i zdolność pojazdu do radzenia sobie z pobliskimi zagrożeniami. Mają też delikatną optoelektronikę i wrażliwe silniki elektryczne. Ponieważ są one zwykle montowane w górnej części pojazdu, opancerzenie powinno być lekkie, aby utrzymać środek ciężkości jak najniżej.
System ochrony modułów broni, który może obejmować szkło pancerne i ochronę górnej części, jest całkowicie składany, dwie osoby mogą go ponownie złożyć w 90 sekund. Kompozytowe kapsułki przeżywalności są wykonane z tego, co firma określa jako „unikalne wytrzymałe materiały i formuły polimerowe”, zapewniają ochronę przed odłamkami i mogą być naprawiane w terenie.
Ochrona żołnierza
SPS (Soldier Protection System) opracowany przez 3M Ceradyne obejmuje hełmy i wkładki w kamizelkach kuloodpornych dla zintegrowanego systemu ochrony głowy (IHPS) i VTP (Vital Torso Protection) - komponenty ESAPI (Enhanced Small Arms Protective Insert) - ulepszona wkładka do ochrony przed broni strzeleckiej) systemu SPS.
Wymagania IHPS obejmują mniejszą wagę, pasywną ochronę słuchu i ulepszoną ochronę przed tępym uderzeniem. W skład systemu wchodzą również akcesoria takie jak komponent chroniący dolną szczękę żołnierza, wizjer ochronny, mocowanie gogli noktowizyjnych, prowadnice np. latarki i kamery oraz dodatkowe modułowe kulochwyty. Kontrakt o wartości ponad 7 milionów dolarów przewiduje dostawę około 5300 hełmów. W międzyczasie ponad 30 000 zestawów ESAPI - lżejszych wkładek do kamizelek kuloodpornych - zostanie dostarczonych w ramach kontraktu o wartości 36 milionów dolarów. Produkcja obu tych zestawów rozpoczęła się w 2017 roku.
Również w ramach programu SPS KDH Defence wybrało materiały SPECTRA SHIELD i GOLD SHIELD firmy Honeywell dla pięciu podsystemów, w tym podsystemu ochrony tułowia i kończyn (TEP), które mają być dostarczone do projektu SPS. System ochrony TEP jest o 26% lżejszy, co ostatecznie zmniejsza wagę systemu SPS o 10%. KDH we własnych produktach do tego systemu zastosuje SPECTRA SHIELD, który jest oparty na włóknie UHMWPE oraz GOLD SHIELD, oparty na włóknach aramidowych.
Włókno SPECTRA
Honeywell wykorzystuje zastrzeżony proces przędzenia i ciągnienia włókien polimerowych, aby osadzić surowiec UHMWPE we włóknie SPECTRA. Materiał ten jest 10 razy mocniejszy wagowo od stali, jego wytrzymałość właściwa jest o 40% wyższa niż włókna aramidowego, ma wyższą temperaturę topnienia niż standardowy polietylen (150°C) oraz większą odporność na zużycie w porównaniu z innymi polimerami, dzięki czemu na przykład poliester.
Mocny i sztywny materiał SPECTRA wykazuje duże odkształcenia przy zerwaniu, czyli bardzo mocno się rozciąga przed zerwaniem; ta właściwość umożliwia pochłanianie dużej ilości energii uderzenia. Honeywell twierdzi, że kompozyty włókniste SPECTRA bardzo dobrze radzą sobie z uderzeniami o dużej prędkości, takimi jak pociski karabinowe i fale uderzeniowe. Według firmy „Nasze zaawansowane włókno reaguje na uderzenia, szybko usuwając energię kinetyczną ze strefy uderzenia… ma również dobre tłumienie drgań, dobrą odporność na powtarzające się odkształcenia i doskonałe właściwości tarcia wewnętrznego włókien, a także doskonałą odporność na chemikalia, woda i światło UV.”
W swojej technologii SHIELD Honeywell rozkłada równoległe pasma włókien i łączy je ze sobą, impregnując je zaawansowaną żywicą, tworząc jednokierunkową wstęgę. Następnie warstwy tej taśmy układa się poprzecznie pod żądanymi kątami oraz przy zadanej temperaturze i ciśnieniu, lutuje w strukturę kompozytową. W przypadku miękkich aplikacji do noszenia jest laminowany między dwiema warstwami cienkiej i elastycznej przezroczystej folii. Ponieważ włókna pozostają proste i równoległe, bardziej efektywnie rozpraszają energię uderzenia, niż gdyby były wplecione w tkaninę.
Short Bark Industries używa również SPECTRA SHIELD w ochroniarzu BCS (Ballistic Combat Shirt) dla systemu SPS TEP. Short Bark specjalizuje się w miękkiej ochronie, odzieży taktycznej i akcesoriach.
Według Honeywell, żołnierze wybrali elementy ochronne wykonane z tych materiałów po tym, jak wykazali lepszą wydajność niż ich odpowiedniki z włókna aramidowego.