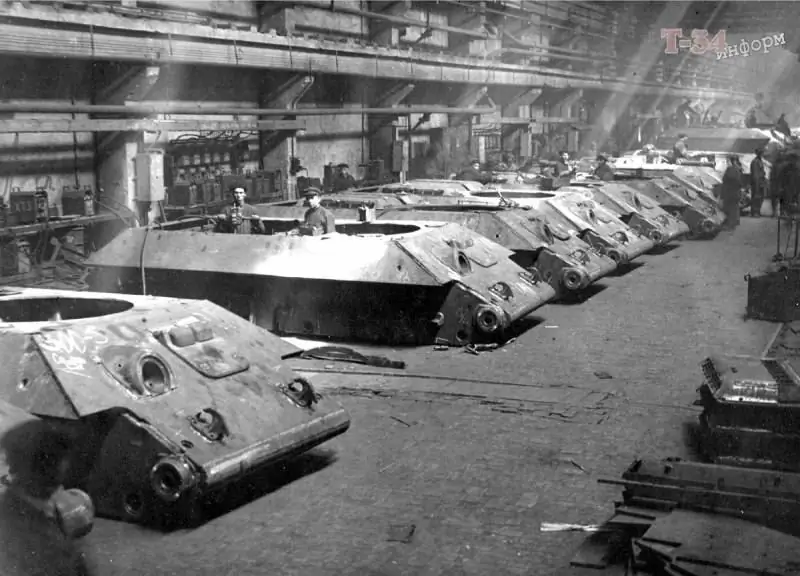
Słabe ogniwa stalowej osłony
Jak może lawinowo zwiększyć produkcję czołgów tak potrzebnych frontowi? Książka Nikity Mielnikowa „Przemysł czołgów ZSRR podczas Wielkiej Wojny Ojczyźnianej” zawiera dane na temat pogorszenia warunków otrzymywania gotowych produktów przez przedstawicieli wojskowych.
Od 15 stycznia 1942 r. fabryki czołgów są bardzo „liberalne” w ocenie jakości produkcji pojazdów opancerzonych. Tylko co dziesiąty czołg średni T-34 i ciężki KV na wybór przedstawiciela wojskowego został poddany krótkiemu pięciokilometrowemu przebiegowi. W przypadku czołgów T-60 wątpliwości było oczywiście więcej, więc co piąty czołg lekki został poddany próbie. A może takie maszyny były mniej potrzebne na froncie, dlatego były wobec nich surowsze nawet na etapie akceptacji. Pośrednio potwierdza to strzelanie kontrolne z armaty każdego T-60 opuszczającego bramy fabryk, podczas gdy działa T-34 i KV były testowane tylko na co dziesiątym pojeździe. Zezwalano na wysyłanie do wojsk czołgów z brakującymi prędkościomierzami, silnikami obracającymi wieże, interkomami, jeśli zostały zastąpione lampkami sygnalizacyjnymi, a także wentylatorami wieżowymi. Ostatni punkt na szczęście był dozwolony tylko zimą.
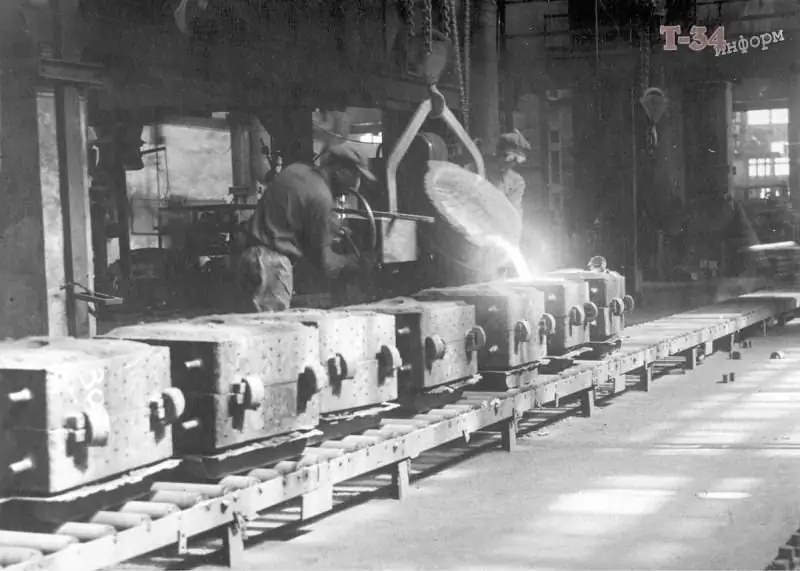
Należy osobno zauważyć, że przemysł czołgów już do połowy 1942 roku z powodzeniem radził sobie z ilościowymi wskaźnikami produkcji pojazdów opancerzonych. Uralmash regularnie przekraczał nawet normy produkcyjne dla czołgów, a fabryka Kirowa w Czelabińsku tylko od stycznia do marca zwiększyła czterokrotnie produkcję silnika wysokoprężnego V-2.
Takie tempo wzrostu produkcji było w dużej mierze spowodowane poważnym spadkiem jakości zbiorników schodzących z linii montażowej. Obrazowym przykładem jest 121. Brygada Pancerna, która podczas 250-kilometrowego rzutu straciła z powodu awarii połowę swoich ciężkich KV. Stało się to w lutym 1942 roku. Przez długi czas sytuacja nie uległa zasadniczej zmianie. Jesienią 1942 r. skontrolowano 84 czołgi KV, które były niesprawne z przyczyn technicznych, przez co nie przepracowały nawet 15 godzin motocyklowych. Najczęściej były to wadliwe silniki, zepsute skrzynie biegów, wadliwe rolki, bezużyteczne tripleksy i wiele drobnych usterek. Latem 1942 roku do 35% wszystkich czołgów T-34 zostało straconych nie z powodu trafienia pociskami wroga lub wysadzenia przez minę, ale z powodu awarii komponentów i zespołów (głównie silników). Nikita Mielnikow w swojej pracy sugeruje, że część strat można przypisać niskim kwalifikacjom załogi, ale nawet biorąc to pod uwagę, procent strat pozabojowych jest zbyt wysoki. Jednak takie awarie KV i T-34 można było łatwo wyeliminować w terenie, czasami po prostu wymieniając jednostkę lub zespół. Jednak walka z niezadowalającą jakością pancerza T-34 na froncie była bezużyteczna - pancerne kadłuby były ugotowane ze stali o niskiej lepkości, która po trafieniu pociskami wroga powodowała pękanie, rozwarstwianie i odpryskiwanie. Często na nowych maszynach powstawały pęknięcia, które znacznie zmniejszały szanse załogi na pomyślny wynik, gdy niemiecki pocisk trafi w pęknięcie lub sąsiedni obszar pancerza.
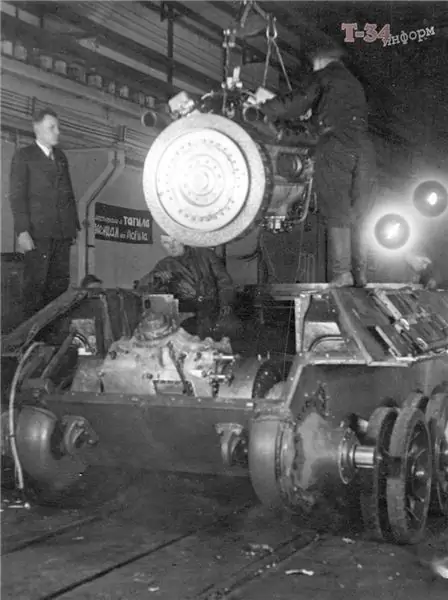
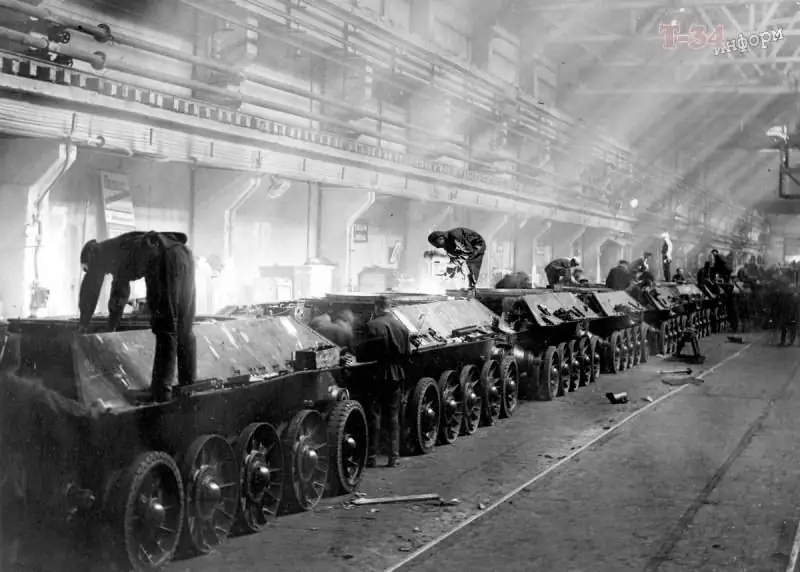
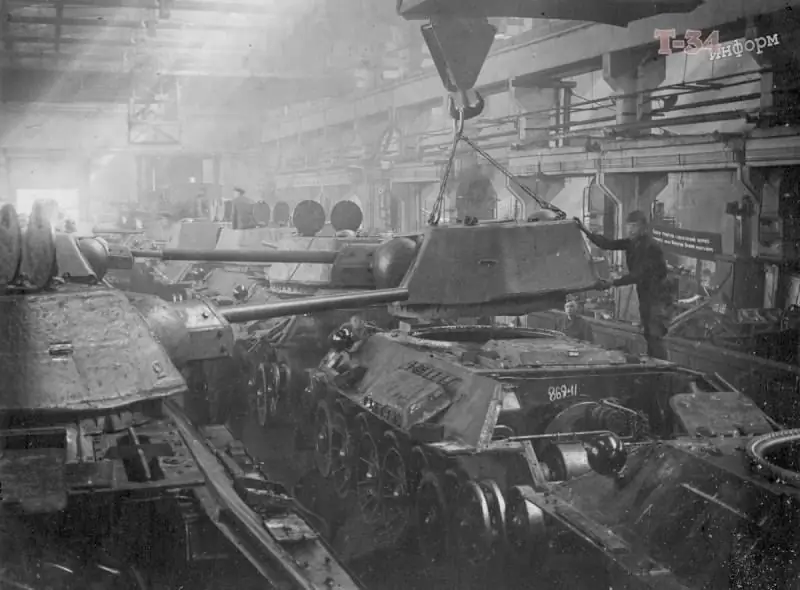
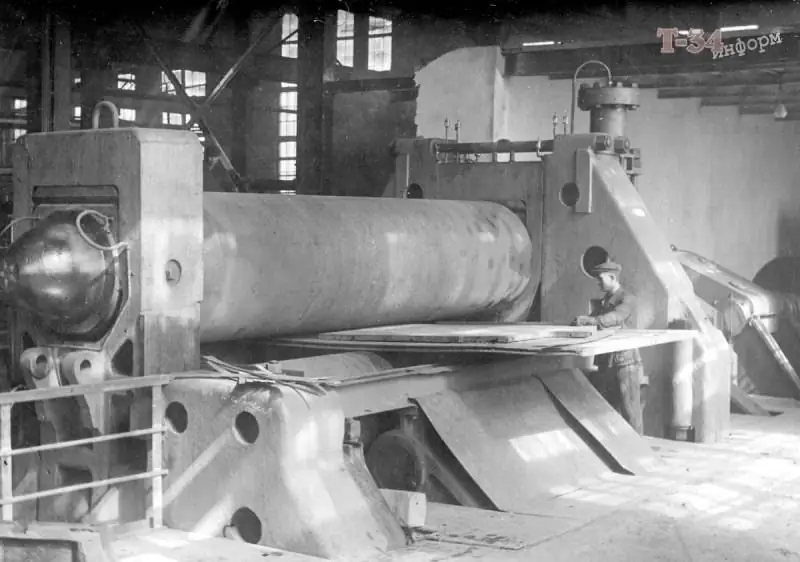
Pierwsze alarmujące wezwania o przybyciu jednostek T-34 z pęknięciami zabrzmiały w maju 1942 r.: fabryka nr 183 otrzymała zgłoszenia na 13 pojazdów w tym miesiącu, 38 czołgów w czerwcu i 72 T-34 w ciągu pierwszych dziesięciu dni Lipiec … Rząd nie mógł milczeć w tej sprawie i 5 czerwca Komitet Obrony Państwa przyjął rezolucję „O ulepszeniu czołgów T-34”. Jednocześnie prokuratura ZSRR otrzymała polecenie zbadania przyczyn spadku jakości czołgów.
W trakcie pracy śledczy w szczególności odkryli liczne fakty kradzieży produktów z diety pracowników przedsiębiorstw przemysłu czołgów. Pracownicy fabryki byli po prostu niedożywieni. Przykładem takiej drapieżnej postawy jest seria materiałów o Izaaku Zaltsmanie, najbardziej kontrowersyjnym liderze fabryk czołgów.
Wśród przedsiębiorstw, które „wyróżniły się” w produkcji wadliwych T-34, pierwsze miejsce zajęła słynna fabryka w Niżnym Tagile. Co więcej, szczyt w wypuszczaniu wadliwych produktów spadł właśnie w czasie kierownictwa wspomnianego Zaltsmana. Jednak dyrektor przedsiębiorstwa, jak pamiętamy, nie został zdegradowany, ale natychmiast mianowany komisarzem ludowym przemysłu czołgów. Oczywiście władze postanowiły obwiniać najwyższe szczeble Wiaczesława Aleksandrowicza Małyszewa, I Komisarza Ludowego przemysłu czołgów ZSRR. To prawda, że wytrzeźwienie nastąpiło rok później, latem 1943 r. Małyszew ponownie został umieszczony na stanowisku komisarza ludowego, które zachował do samego końca wojny.
Prokuratura w trakcie pracy w ewakuowanych przedsiębiorstwach przemysłu czołgów, oprócz na wpół zagłodzonej egzystencji pracowników fabryki, ujawniła kolejny problem niezadowalającej jakości czołgów - poważne naruszenie cyklu produkcyjnego.
Uproszczenie kosztem jakości
Jak wiadomo, zakład Mariupola imienia Iljicza nie mógł się obronić, trafił w ręce wroga, a także z masą sprzętu technologicznego, którego nie udało się ewakuować. To właśnie to przedsiębiorstwo (jedyne w kraju) było w stanie wyprodukować pełnoprawne kadłuby pancerne dla T-34 zgodnie ze wszystkimi normami. Na Uralu żadna fabryka nie mogła zaoferować czegoś takiego, więc zespół badawczy Instytutu Pancernego (TsNII-48) zaczął dostosowywać praktyki Mariupola do realiów ewakuowanych fabryk. Do produkcji wysokiej jakości zbroi w ilościach wymaganych przez GKO wystąpił dotkliwy brak pieców termicznych, dlatego instytut opracował nowy cykl hartowania części zbroi. W Mariupolu blacha zbroi najpierw poszła na hartowanie, potem na wakacje, a potem znowu na hartowanie. W końcu nastąpiły krótkie wakacje. Aby przyspieszyć produkcję, najpierw anulowano pierwsze hartowanie, a następnie wysokie odpuszczanie, co bezpośrednio wpływa na twardość stali pancernej i zmniejsza prawdopodobieństwo pękania. Wśród niezbędnych środków, zdaniem specjalistów Instytutu Pancerza, było też załadowanie do pieca cieplnego nie jednego, ale natychmiast czterech lub pięciu rzędów płyt pancernych. Oczywiście okazało się to znacznie szybsze, ale ostateczna jakość płyt była bardzo niejednorodna. Co ciekawe, Instytut Pancerny postanowił później zrezygnować z procedury niskiego odpuszczania, co zmniejsza naprężenia szczątkowe metalu, co ponownie nie ominęło negatywnego wpływu na powstawanie pęknięć.
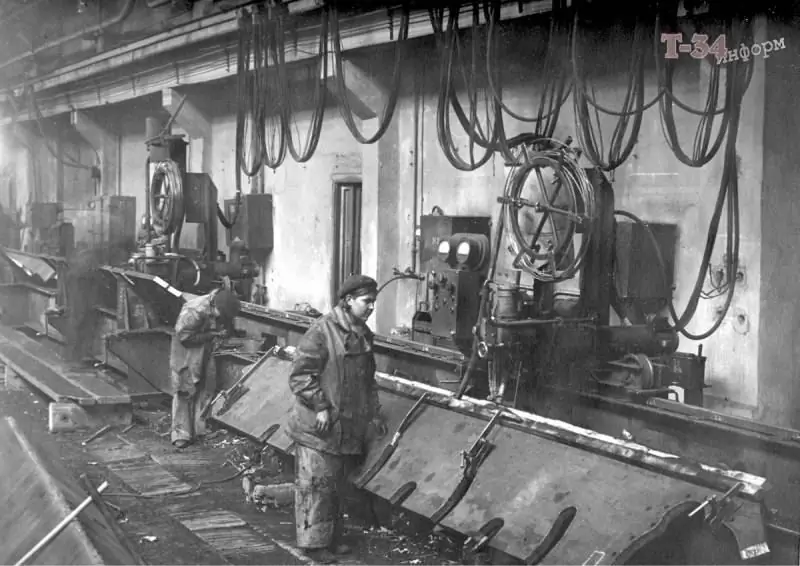
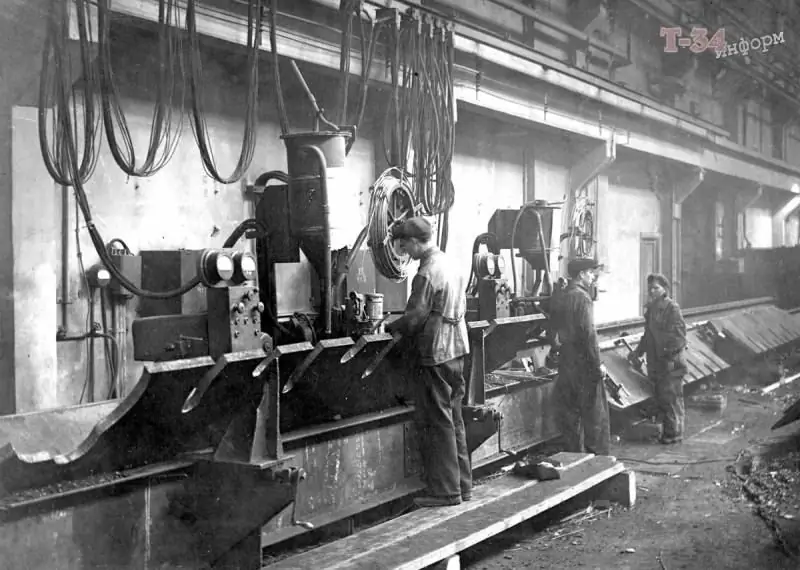
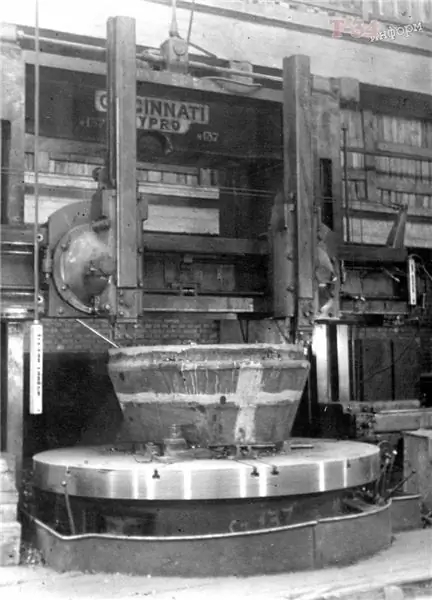
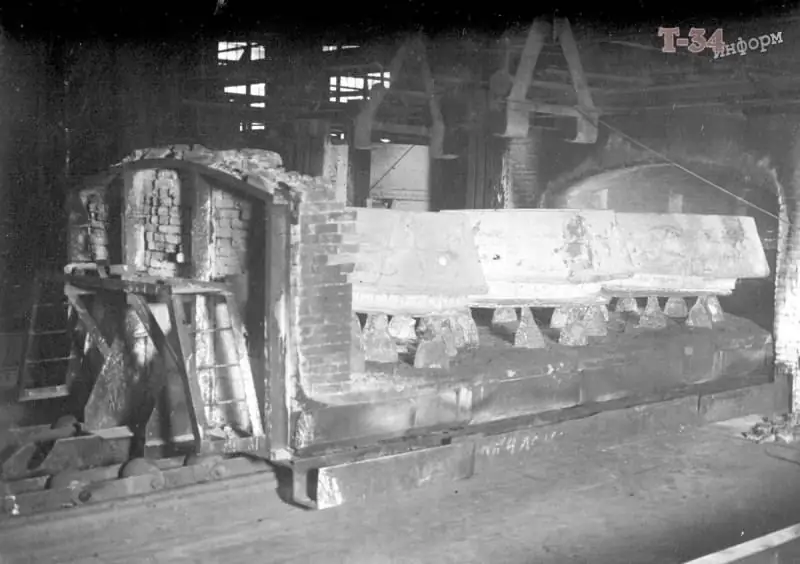
Hartowanej stali nie da się ciąć przecinarkami gazowymi - ta teza jest znana wszystkim, ale realia produkcji pancernych kadłubów T-34 zmuszają do uciekania się do tej niepopularnej metody. Chodziło o stal 8C, która rozszerzała się po hartowaniu, co oczywiście zmusiło pracowników fabryki do cięcia jej palnikami wysokotemperaturowymi. Utracono punkt utwardzania pancerza w obszarze cięcia.
Nie warto twierdzić, że zalecenia dotyczące ulepszenia procesu produkcyjnego były tylko negatywne dla jakości pancerza. Tak więc prawdziwą innowacją w montażu kadłubów czołgów T-34 było spawanie płyt pancernych „w kolce” zamiast starych „w zamek” i „w ćwiartkę”. Teraz współpracujące części nie wcinały się w siebie, ale częściowo nakładały się na siebie. Dopiero ta decyzja poważnie zmniejszyła liczbę maszynogodzin na sprawę z 198,9 do 36.
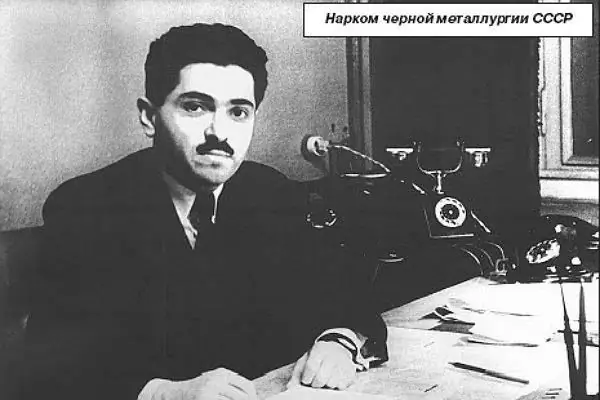
Głównym dostawcą wadliwej blachy stalowej do fabryk produkujących T-34 była fabryka Novo-Tagil Ludowego Komisariatu Metalurgii Żelaza. Początkowo przerywały mu dostawy z Mariupola, a gdy przeszedł na własne, napływały fale skarg z frontu i z fabryk. W szczególności w składzie zbroi 8C z tego przedsiębiorstwa wystąpiły poważne rozbieżności ze specyfikacjami technicznymi (TU) w zawartości węgla, fosforu i krzemu. Ogólnie rzecz biorąc, były problemy z TU. Ludowy Komisariat Metalurgii Żelaza nie zgodził się na zachowanie TU zgodnie ze standardami Mariupola, w których w szczególności fosfor nie powinien przekraczać 0,035%. Na początku listopada 1941 r. Komisarz Ludowy Metalurgii Żelaza Iwan Tewosjan zatwierdził nowe normy dla fosforu, które zwiększyły możliwą zawartość do 0,04%, a od 4 kwietnia do 0,045%. Warto zauważyć, że historycy wciąż nie mają zgody co do tego, oczywiście, ważnego czynnika jakości pancernej stali. W szczególności Nikita Melnikov wspomina, że fabryka Novo-Tagil, wręcz przeciwnie, do połowy 1942 r. Zmniejszyła udział fosforu z 0, 029% do 0, 024%. Wydaje się, że różni naukowcy znajdują różne powody pojawienia się wadliwych T-34 na froncie. Tak czy inaczej, czasami nie przestrzegano wskazanych norm dotyczących zawartości pierwiastków chemicznych w składzie stali. Fabrykom trudno było ustalić prostą jednorodność dostarczanych wyrobów walcowanych. Prokuratura ujawniła również, że w zakładach hutnictwa żelaza w piecach martenowskich stal pancerna była „niedogotowana” - zamiast 15-18 godzin w rzeczywistości, nie więcej niż 14 godzin.
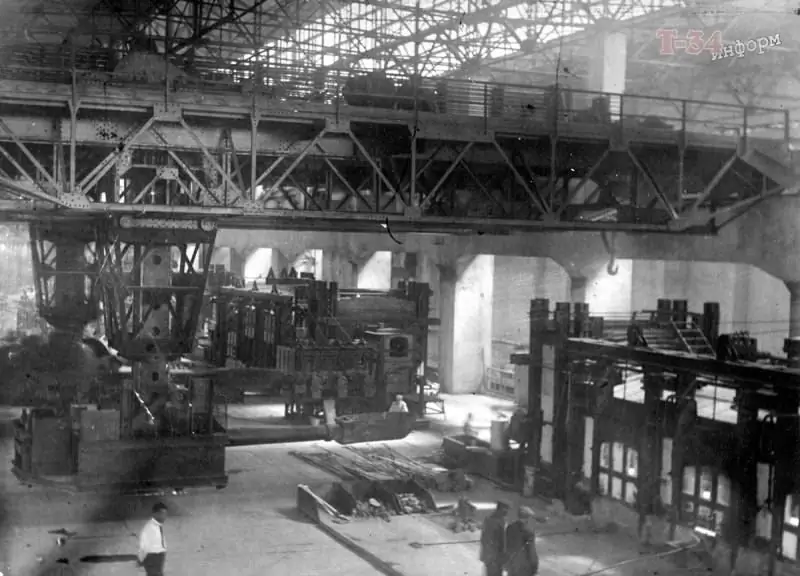
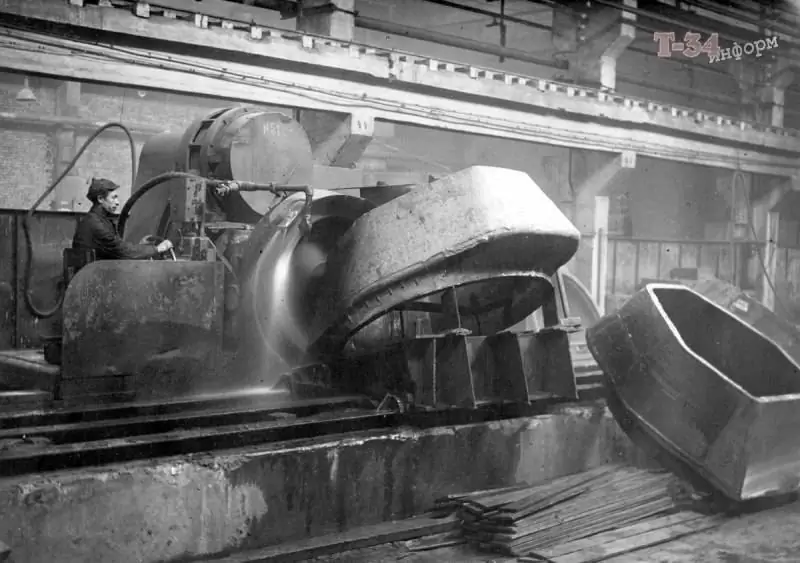
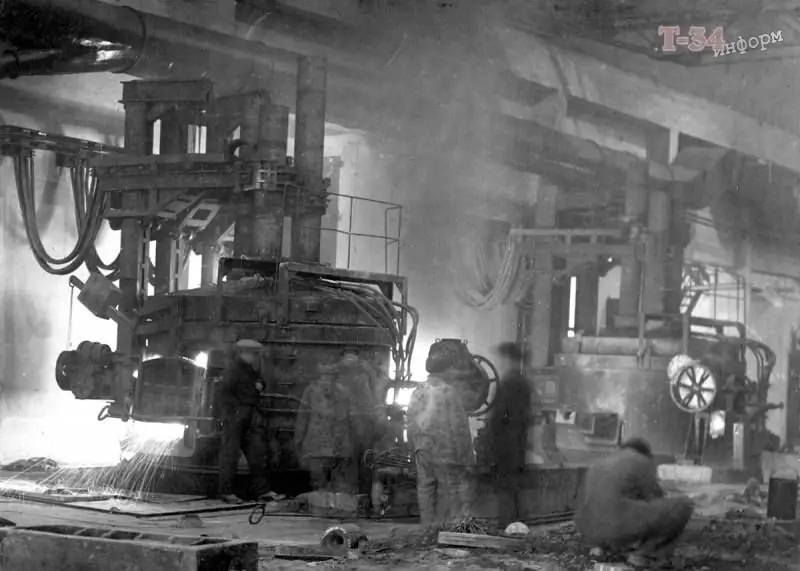
Kiedy informacja o przyczynach pękania kadłubów T-34 dotarła do Mołotowa, komisariaty ludowe metalurgii żelaza i przemysł czołgowy zaczęły przerzucać odpowiedzialność na siebie. Z jednej strony głównym powodem była wysoka zawartość fosforu w płytach pancernych, z drugiej poważne naruszenia technologii produkcji kadłubów w fabrykach czołgów.
W rezultacie TsNII-48 był zaangażowany w prace nad zwalczaniem pęknięć na T-34 (chociaż był pośrednio winny ich pojawienia się). Zaproponowany przez instytut zestaw środków dopiero do końca 1943 r. pozwolił na wyeliminowanie części uwag. A poprawa jakości produkcji stali w zakładach hutnictwa żelaza umożliwiła zmniejszenie udziału odrzutów z 56, 25% w 1942 r. do 13, 30% w 1945 r. Do końca wojny przedsiębiorstwa nie osiągnęły poziomu zbliżonego do 100%.