Tak ciężką maszynę jak Mi-26 trzeba unieść w powietrze śmigłem o klasycznej konstrukcji, co zapewni jej niezawodność i trwałość. W momencie opracowywania Mil Design Bureau miało bardzo małe doświadczenie w tworzeniu łopat z włókna szklanego, więc początkowo postanowiono porzucić je w nowym śmigłowcu transportowym. Jako materiał dźwigarów śmigła wybrano stal, co zapewniło duży margines wytrzymałości zmęczeniowej. Było też trochę know-how - ucha do mocowania do tulei zostały wykonane w jednym kawałku z główną rurą śruby, co pozwoliło na wzmocnienie konstrukcji bez zwiększania masy. Włókno szklane wciąż znajdowało swoje miejsce w ostrzu jako struktura budująca formę wokół stalowego dźwigara.
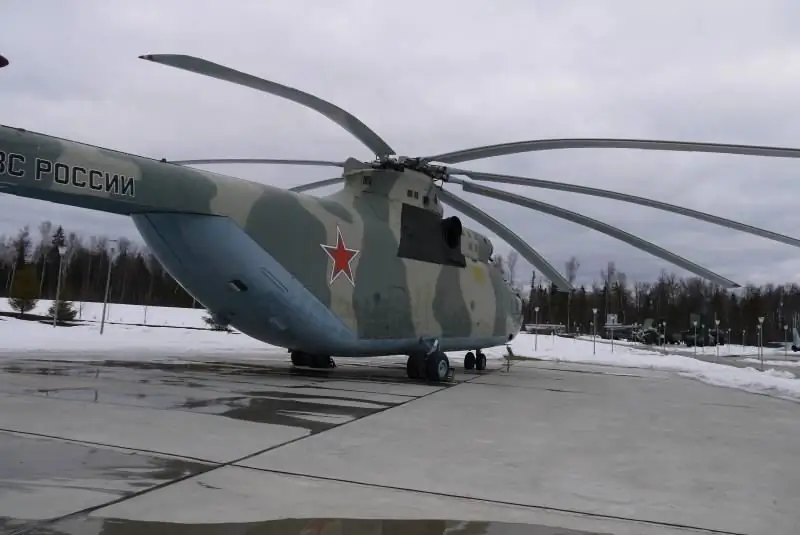
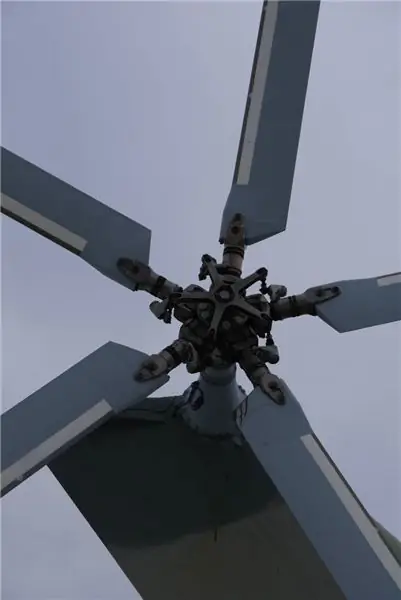
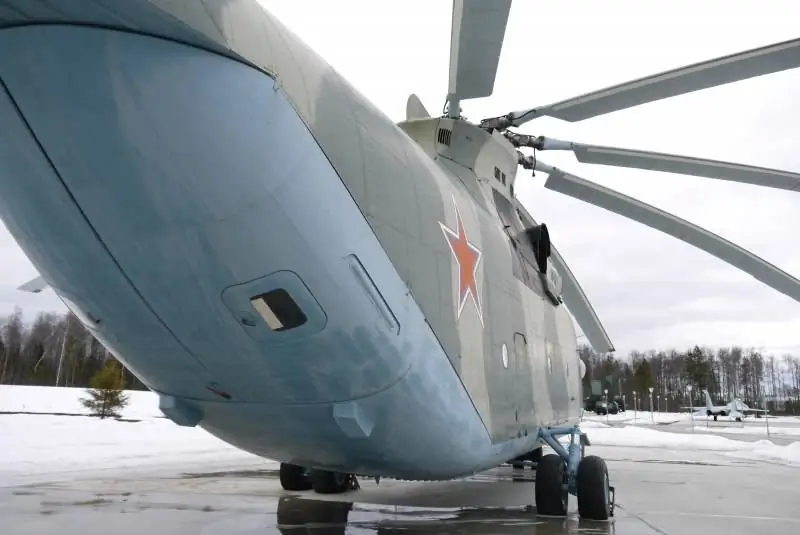

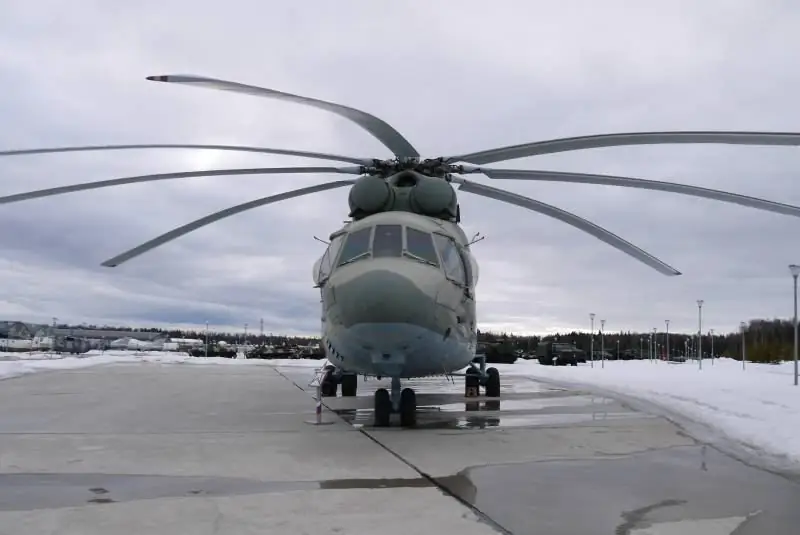
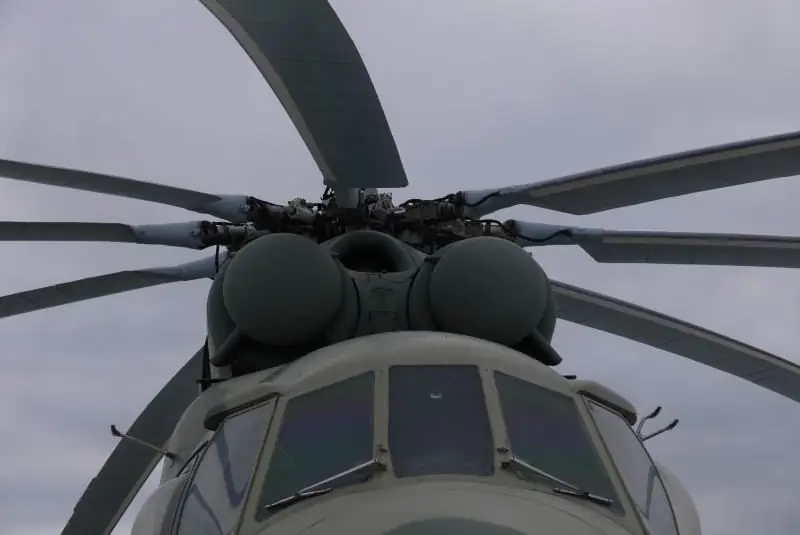
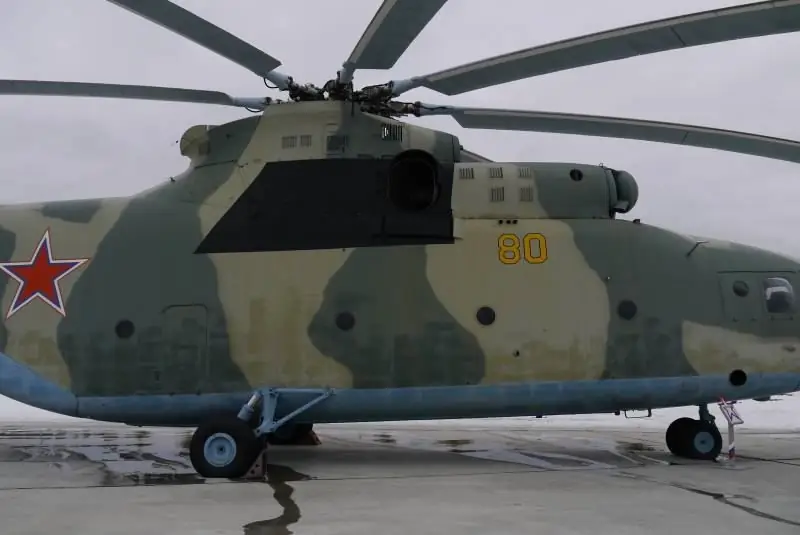
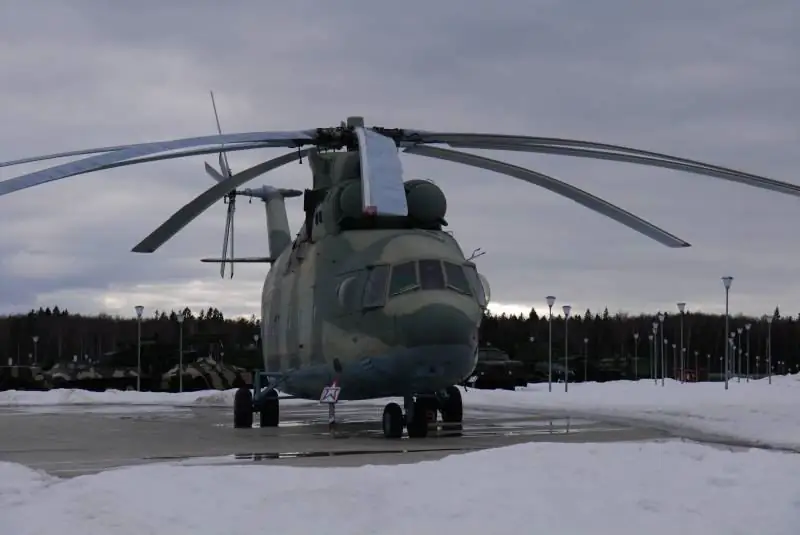
Mi-26 w ekspozycji Parku Patriot
Ręczne układanie skorupy ostrza z włókna szklanego powodowało powstawanie fałd, które w późniejszej eksploatacji mogły prowadzić do powstawania pęknięć. Z tego powodu konieczne było zainstalowanie systemu pneumatycznego do wykrywania pęknięć w łopatach śmigła. Wyjątkowości wirnika głównego Mi-26 dodawało jego osiem łopat, co było pierwszym takim doświadczeniem w światowym przemyśle śmigłowcowym. Nie można było podnieść tak ciężkiej maszyny w powietrze innym śmigłem. Montaż tak masywnego śmigła wymagał zamontowania zdejmowanych tulei tulei, a dla tulei zaprojektowano osobny drążek skrętny, który niweluje siłę odśrodkową. Generalnie tuleja okazała się niezwykle innowacyjna - wiele zawiasów wykonano z łożysk metalowo-fluoroplastycznego, a w konstrukcji stal zastąpiono tytanem. Na uwagę zasługuje postęp poczyniony przez inżynierów KB w projektowaniu głównego wirnika dla Mi-26. W porównaniu z pięciołopatowym śmigłem o średnicy 35 metrów w Mi-6, ośmiołopatowe 28-metrowe śmigło w Mi-26 rozwijało o 30% większy ciąg, podczas gdy jego masa była o 40% mniejsza.
W 1977 r. śmigło zostało ostatecznie przetestowane zarówno w TsAGI, jak iw laboratorium latającym Mi-6. Wnioski były jednoznaczne: konstrukcja w pełni spełnia wymagania nowego śmigłowca i może być polecana do produkcji seryjnej. Jeśli inżynierowie obawiali się stworzenia ramy mocy wykonanej z włókna szklanego z głównym wirnikiem, to postanowili nie uważać na wirnik kierownicy - był on całkowicie wykonany z nowego jak na tamte czasy materiału. Pozwoliło to znacznie zaoszczędzić na wadze gotowego produktu. Ręczne układanie skorupy głównego wirnika z włókna szklanego już w latach 60. wyglądało jak anachronizm, a z inicjatywy Michaiła Leontjewicza Mila biuro projektowe zaczęło opracowywać maszynowe nawijanie skorup. Wtedy narodził się pomysł stałego trzpienia, wokół którego obraca się urządzenie nawijające z czterema rozpórkami. Samo nawijanie na dźwigar odbywa się za pomocą taśmy z przygotowanego prepregu, a procesem steruje skomplikowana maszyna CNC. Milevtsy przyciągnął do rozwoju specjalistów NIAT, którzy pomogli stworzyć matematyczny model nawijania powłoki na trzpienie o złożonym kształcie - łopaty wirnika. Program otrzymał nietrywialną nazwę „Uzwojenie”. Nowa metoda wytwarzania głównej powłoki wirnika przyniosła wiele korzyści: powierzchnia łopat stała się jednorodna, utracone szwy, co w porównaniu z poprzednikami skutkowało większą trwałością i przeżywalnością.
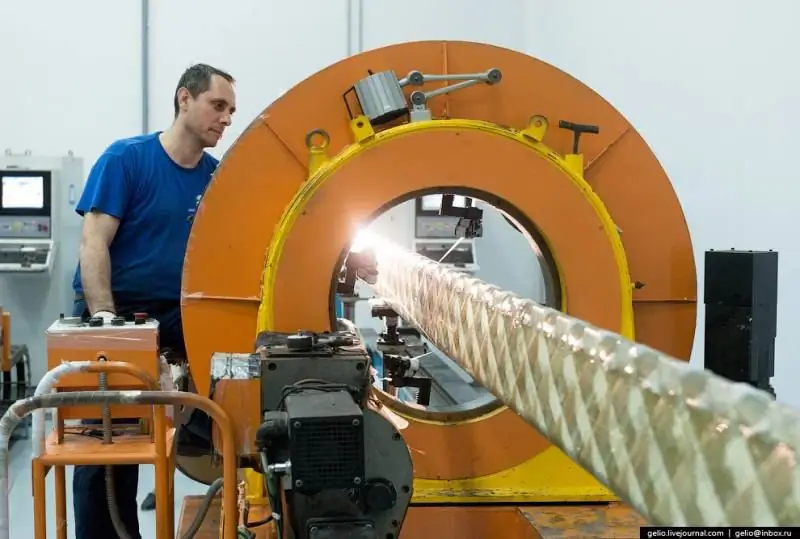
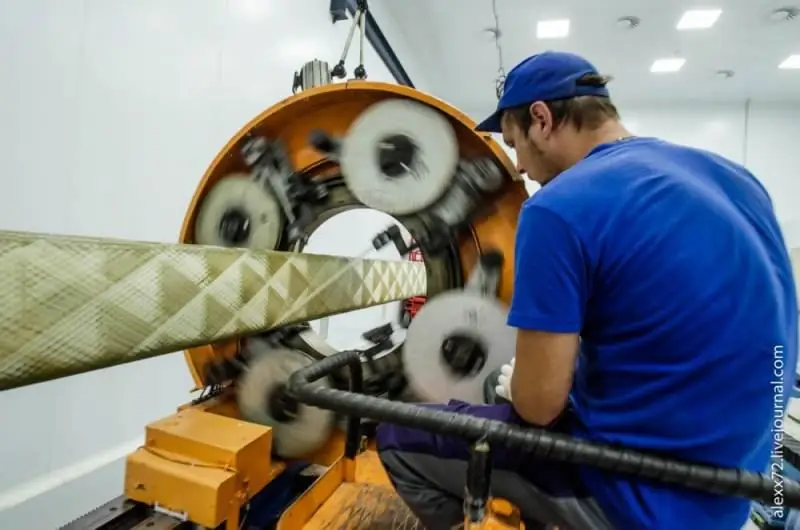
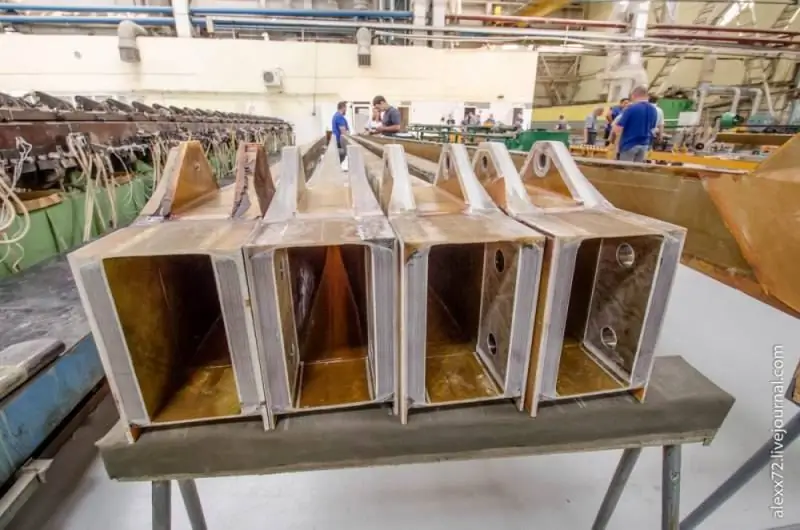
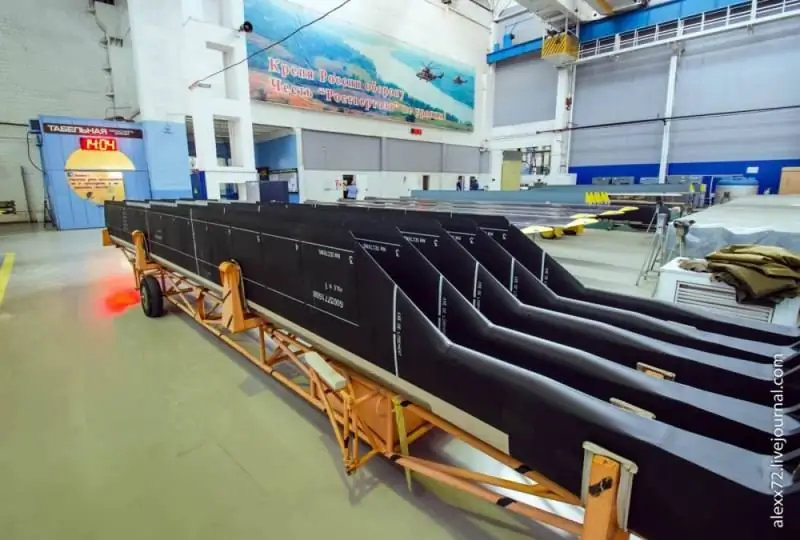
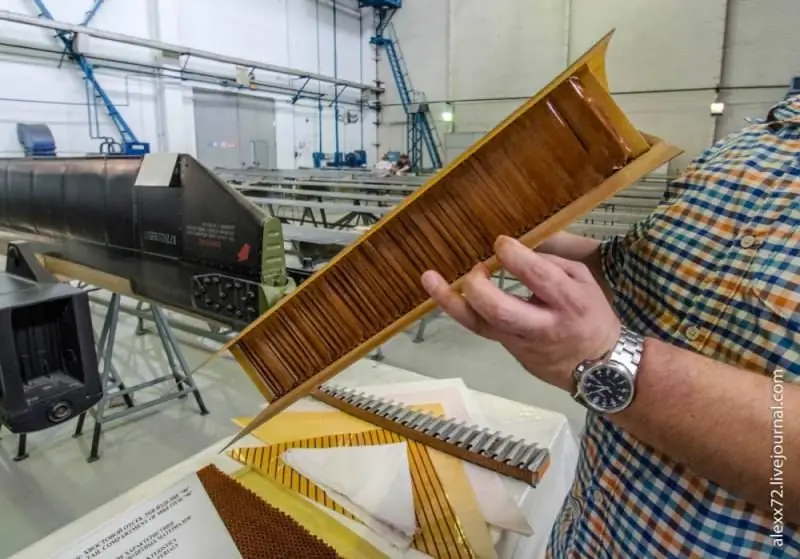
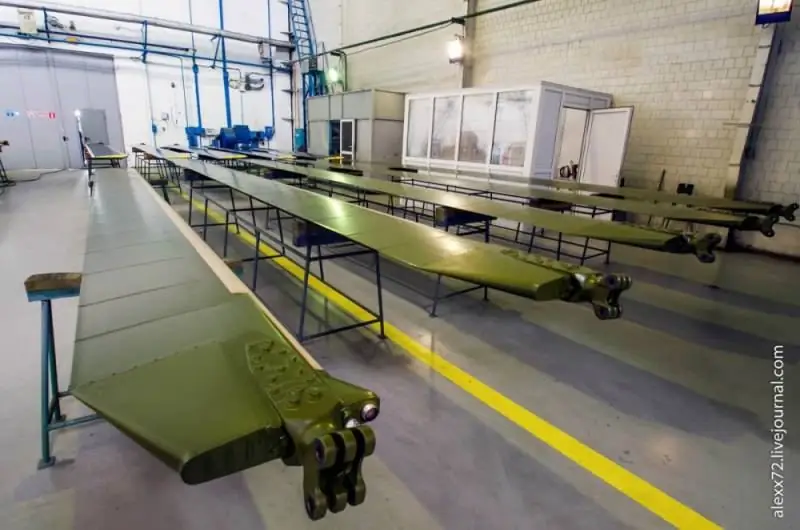
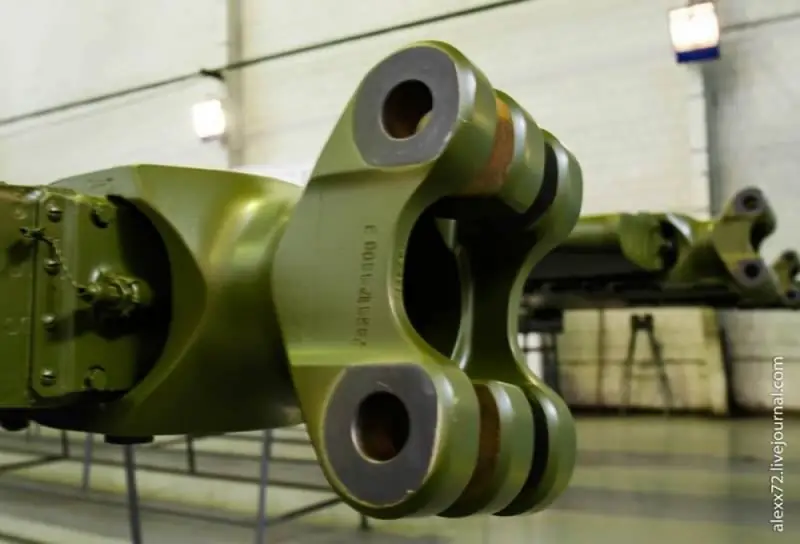
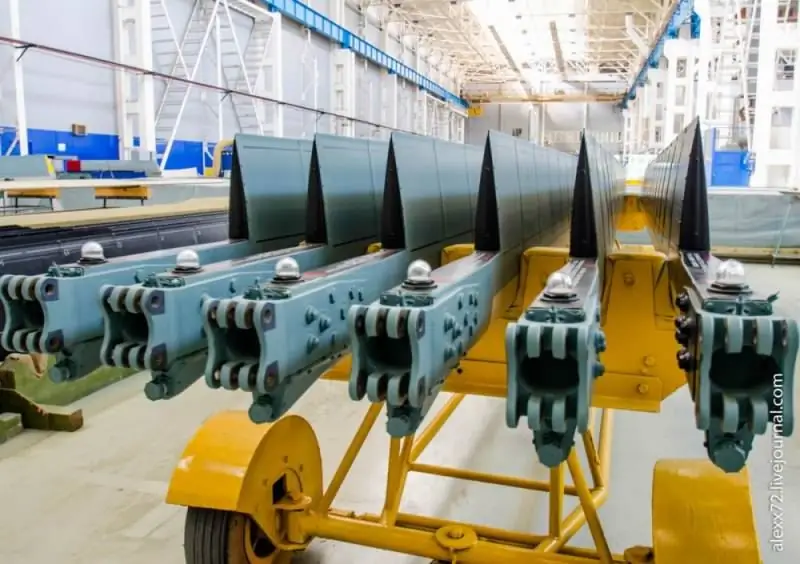
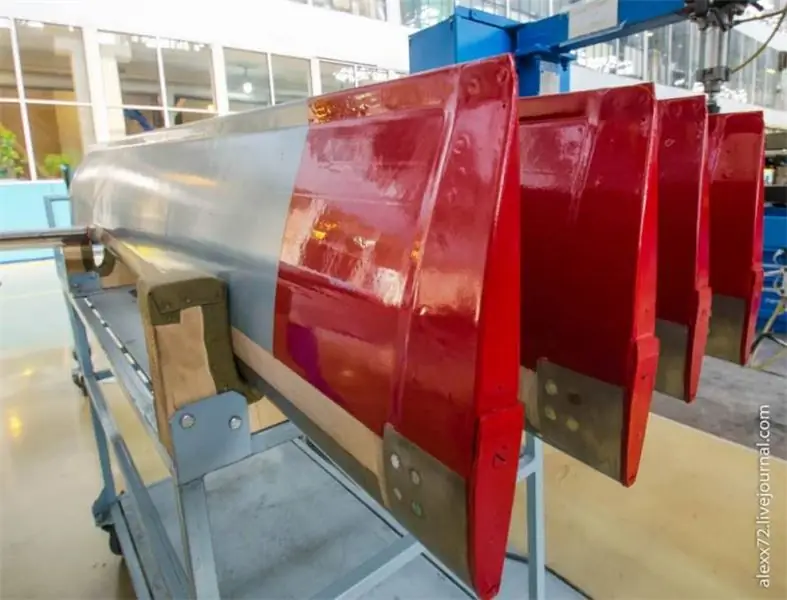
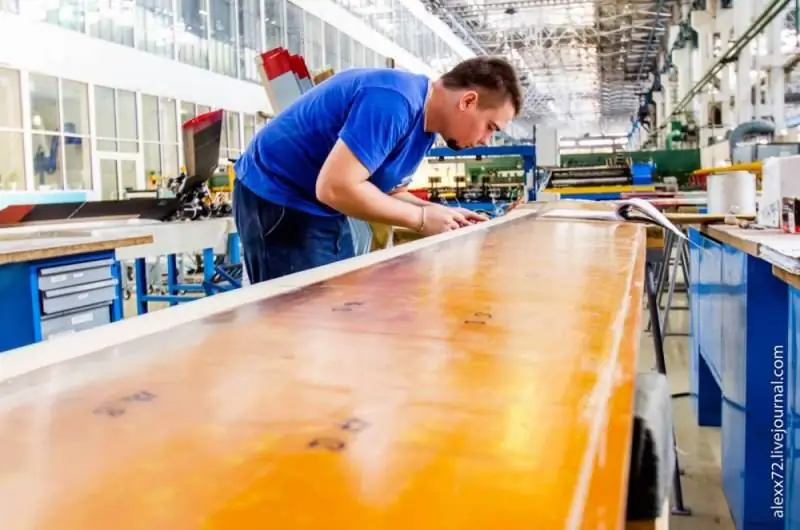
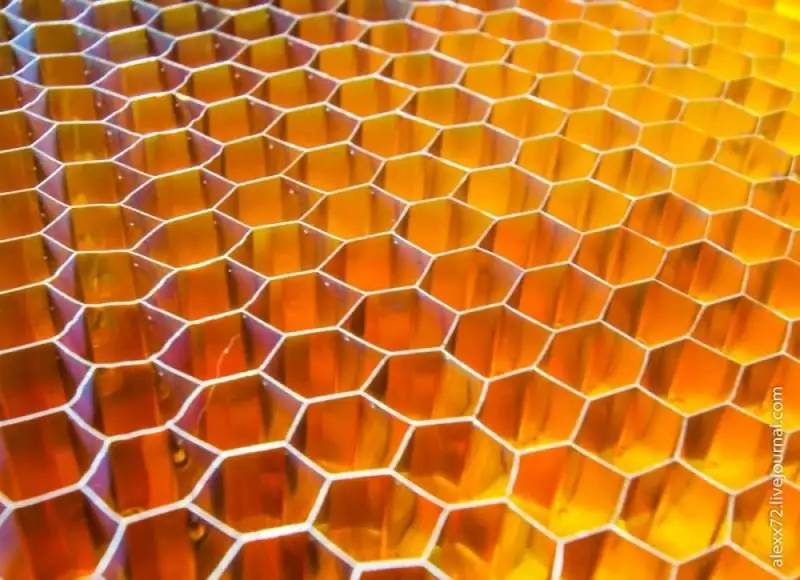
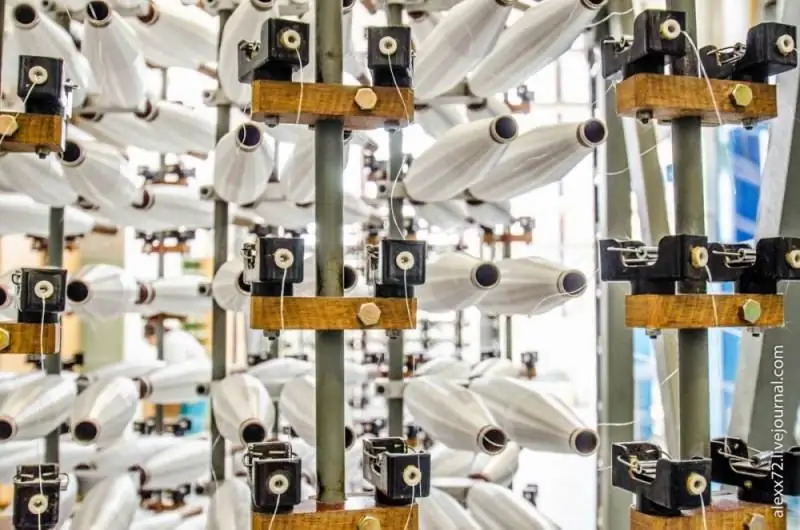
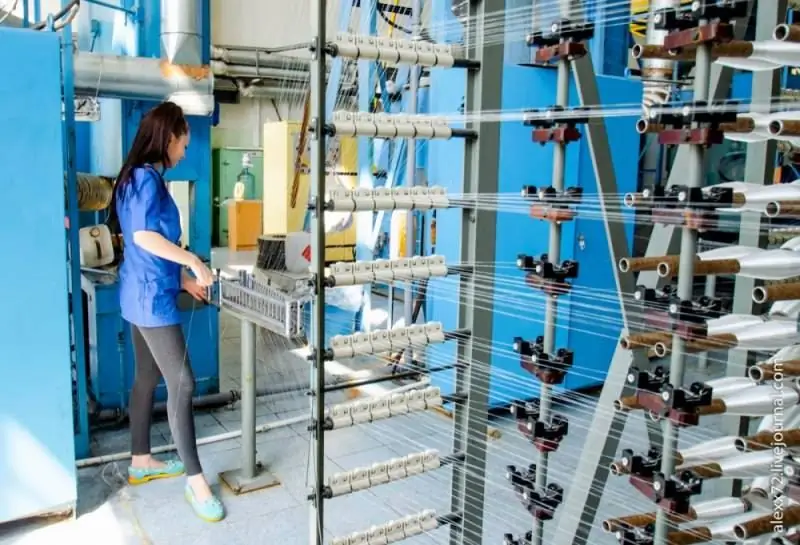
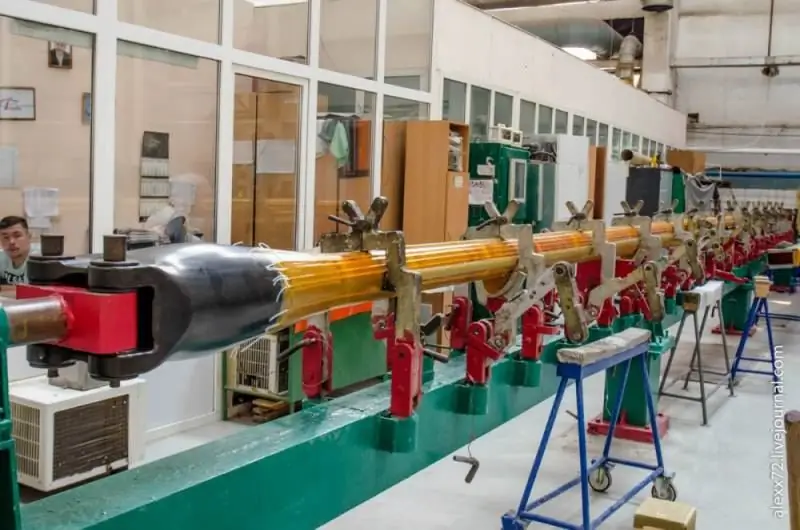
Nowoczesny proces produkcji łopat wirnika do maszyn rodziny Mil w przedsiębiorstwie Rostvertol (Rostów nad Donem)
Kolejnym majstersztykiem inżynierii Mi-26 jest główna skrzynia biegów VR-26, która wciąż nie ma sobie równych na świecie pod względem mocy przenoszonej na wirnik. Żadne biuro konstrukcyjne silników w tym czasie w ZSRR nie było w stanie stworzyć skrzyni biegów o wymaganych parametrach, więc Biuro Projektowe Mil musiało samodzielnie opracować jednostkę. Inżynierowie natychmiast stanęli przed wyborem schematu kinematyki skrzyni biegów - tradycyjna planetarna konkurowała z innowacyjną wielowątkową. Ten ostatni nie był wcześniej stosowany w przemyśle krajowym i nie było doświadczenia z jego wieloletnim działaniem. Jednak znaczny przyrost masy nowego projektu przechylił szalę na korzyść konstrukcji wielowątkowej. Jeśli porównamy skrzynię biegów VR-26 z wczesnym R-7, który jest montowany w Mi-6, to nowy produkt jest tylko o 8,5% cięższy od poprzednika, ale przekazuje 1,5 raza większy moment obrotowy (przesyłana moc podwoiła się od razu) …
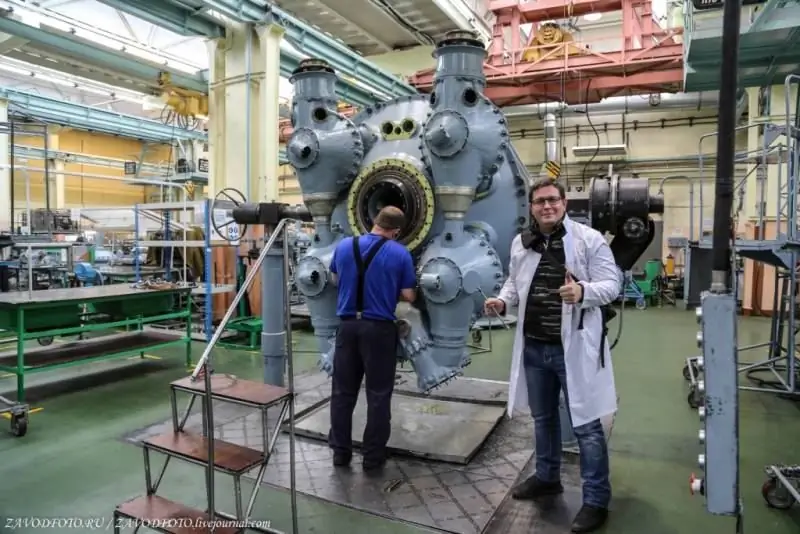
[/środek]
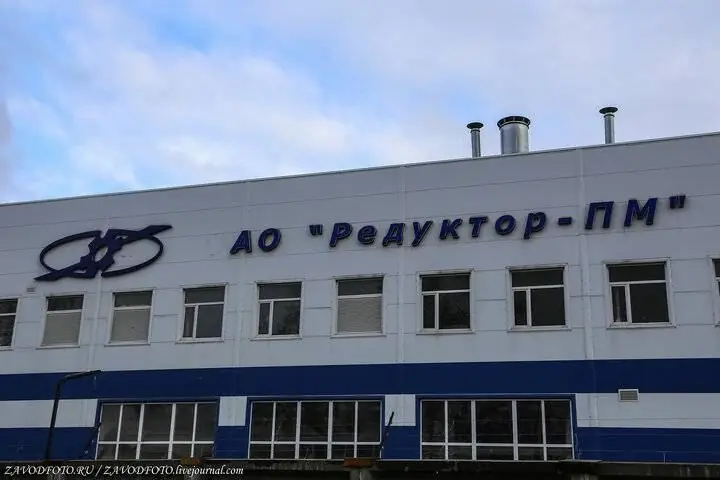
Przekładnia główna VR-26 i firma produkcyjna (Perm)
Podsumowując cechy konstrukcyjne Mi-26, należy stwierdzić, że pojazd ma wysoką autonomię bazową. Jest słabo uzależniony od infrastruktury lotniska - nie ma już potrzeby stosowania drabin, drabin i podobnego sprzętu. Śmigłowiec jest wyposażony w odchylane maski i panele elektrowni, które mogą być obsługiwane przez personel serwisowy. Wewnątrz gigantycznego bomu ogonowego i stępki znajduje się przejście do śmigła ogonowego. Kadłub pojazdu jest pełen drabin, włazów i włazów, co znacznie ułatwia obsługę naziemną.
[środek]
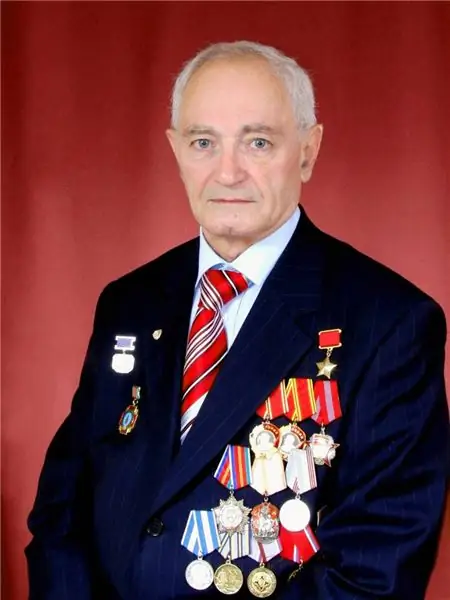
Gurgen Rubenovich Karapetyan, pilot testowy, Bohater Związku Radzieckiego
Ostateczny wygląd i konstrukcja Mi-26 powstała w 1975 roku, co umożliwiło rozpoczęcie montażu prototypów. Dopiero w grudniu 1977 roku pierworodni wyjechali z bram montowni w podmoskiewskich Pankach. A 14 grudnia załoga pilota testowego Gurgena Rubenovicha Karapetyana po raz pierwszy uniosła giganta w powietrze. W lutym 1978 roku w Lyubertsy rozpoczęto pełnoprawne testy fabryczne, które rozwijały się bardzo dobrze - do 1979 roku pierwszy egzemplarz Mi-26 został już przekazany do testów państwowych. W tym samym czasie Rostov Helicopter Plant już stawiał pierwsze kroki w kierunku wprowadzenia maszyny do produkcji seryjnej. Testy wykazały pierwszą i jedyną poważną wadę - w niektórych trybach pracy pojawiły się poprzeczne drgania o niskiej częstotliwości. Analiza wykazała, że przyczyną jest niedoskonały kształt owiewek maski. Inżynierowie szybko dokonali korekt i jednocześnie wymienili łopaty wirnika na nowe o ulepszonej aerodynamice.
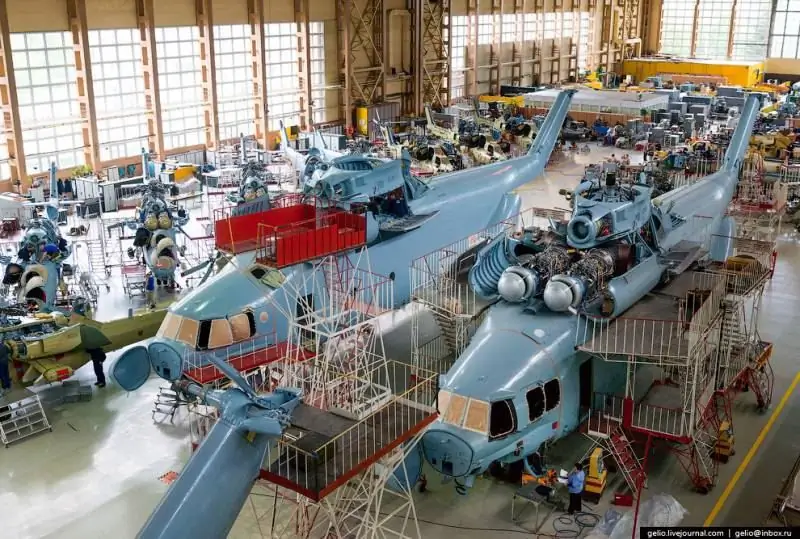
Przyszli giganci na giełdach w Rostowie nad Donem
Do maja 1979 roku do testów podłączono drugi egzemplarz Mi-26, na którym testowano możliwości transportowe śmigłowca. Półtora roku później gigant wykonał sztuczkę, której nikt wcześniej nie zrobił - wylądował na autorotacji o łącznej masie ponad 50 ton. Podczas testów samochód wykonał 12 lądowań w trybie autorotacji i przy wyłączonych silnikach. Znacznie później, w 1997 roku, Mi-26 w locie próbnym wylądował na autorotacji z masą lotu 56 ton! W trakcie prac radziecki gigant z obrotowymi skrzydłami opracował własną metodę przeniesienia maszyny w bezpieczny tryb autorotacji. W tym celu pilot musiał stworzyć pewien kąt pochylenia, który przekłada samochód na pochylenie przy jednoczesnym zmniejszeniu ogólnego pochylenia głównego wirnika. Tylko zgodnie z tym schematem główny wirnik zdążył rozkręcić się do prędkości wymaganej do lądowania. Pionowa prędkość lądowania w tym przypadku wynosiła 2,5 m/s. Łącznie w drugiej fazie prób państwowych (etap „B”) doświadczony śmigłowiec wyleciał 104 godziny i wykonał 150 lotów. Warto zauważyć, że pierwszy prototyp Mi-26 jest nadal w służbie i współpracuje z pojazdem testowym w fabryce śmigłowców Mil Moscow.
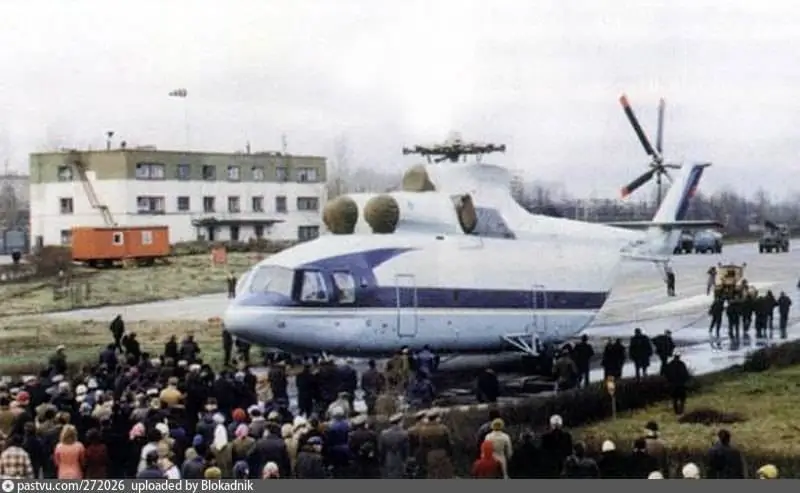
Roll-out pierwszego prototypu Mi-26 z montowni do stacji prób w locie Moskiewskiego Zakładu Śmigłowców w Pankach
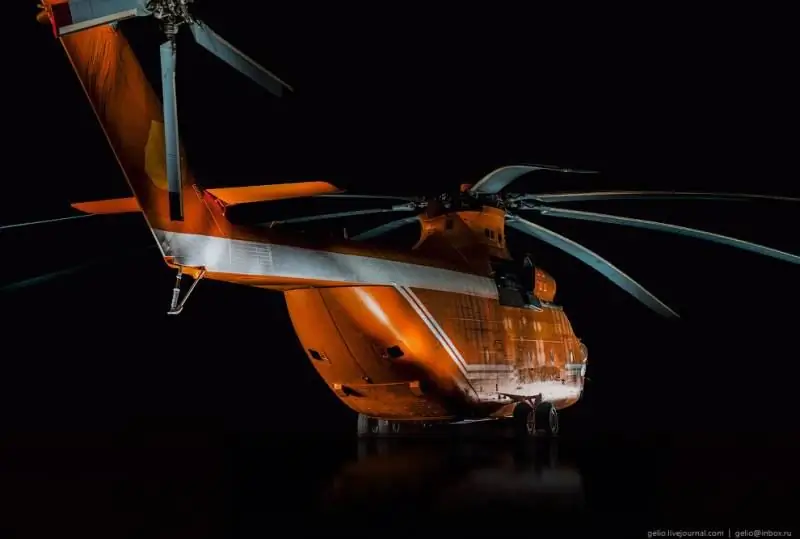
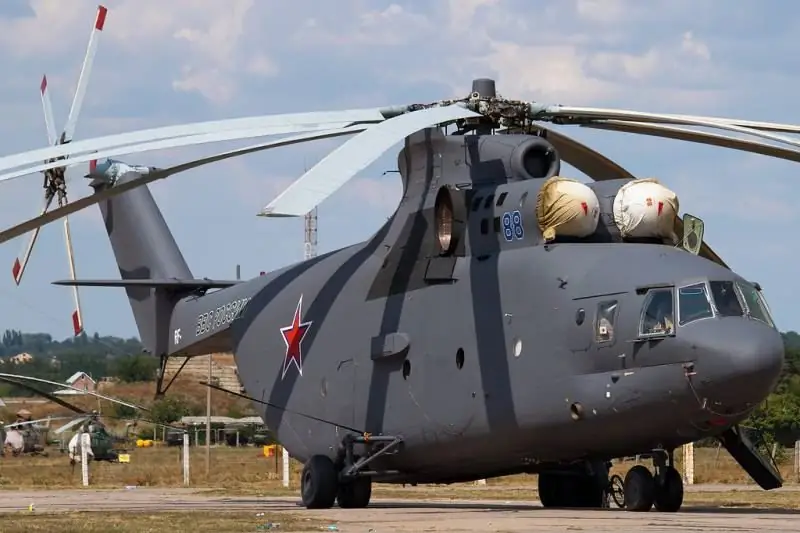
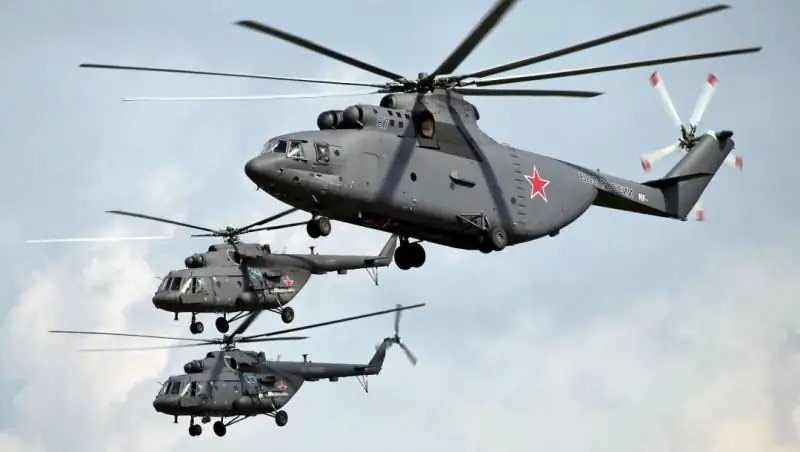
26 sierpnia 1980 r. W końcowym akcie prób państwowych napisano: „Eksperymentalny średni wojskowy śmigłowiec transportowy Mi-26 przeszedł wspólne testy państwowe na etapie„ B”… Lotnicze parametry techniczne, bojowe i operacyjne w zasadzie odpowiadają do cech określonych w dekrecie. Pułap statyczny i maksymalne obciążenia przekraczają określone przez TTT… Doświadczony wojskowy śmigłowiec transportowy Mi-26 i jego podzespoły, który uzyskał pozytywną ocenę zgodnie z wynikami badań, powinien być rekomendowany do uruchomienia do produkcji seryjnej i przyjęty przez Armia Radziecka”. Zwróć uwagę, że w wojsku, zgodnie z klasyfikacją, uznano to za „średnie”. Oczywiście wojsko porównywało Mi-26 z jeszcze bardziej potwornym B-12.