Wojna jest znana jako najlepszy motor postępu. Przemysł czołgów w Związku Radzieckim dokonał oszałamiającego skoku jakościowego w ciągu zaledwie kilku lat wojny. Prawdziwą koroną tego były czołgi z serii IS.
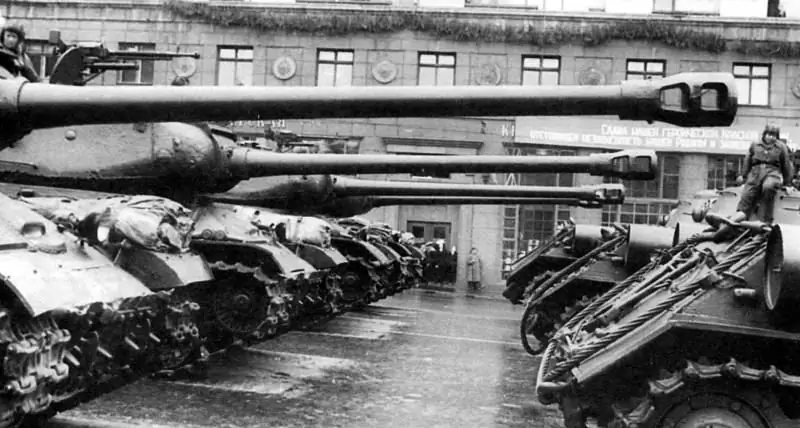
Przepisy Magnitogorsk
W poprzedniej części historii chodziło o odlewany pancerz 70L o wysokiej twardości, stosowany w wieżach czołgów IS. Twórcy opancerzenia z TsNII-48 byli dalecy od pierwszych doświadczeń w tworzeniu ochrony dla czołgów ciężkich.
Przed Wybrzuszeniem Kurskim, które stało się katalizatorem rozwoju krajowej budowy ciężkich czołgów, głównym przedmiotem modernizacji był czołg KV. Początkowo wszystkie prace miały na celu zmniejszenie udziału rzadkich dodatków stopowych w składzie pancerza. Nawet nazwa w TsNII-48 wymyśliła odpowiednią - stal ekonomicznie stopową. Oryginalny pancerz marki FD-7954, z którym czołg KV wszedł do Wielkiej Wojny Ojczyźnianej, zawierał, zgodnie z wymaganiami technicznymi, do 0,45% molibdenu, 2,7% niklu i chromu.
Do końca 1941 r. grupa badaczy kierowana przez Andrieja Siergiejewicza Zawiałowa w Instytucie Pancernym stworzyła recepturę stali FD-6633 lub 49C, w której molibden wymagał nie więcej niż 0,3%, chrom - do 2,3%, a nikiel - do 1, 5%. Biorąc pod uwagę, że czołgi serii KV od drugiej połowy 1941 do 1943 roku zebrano około 4 tysięcy egzemplarzy, można sobie wyobrazić wielkość realnych oszczędności w stopach metali.
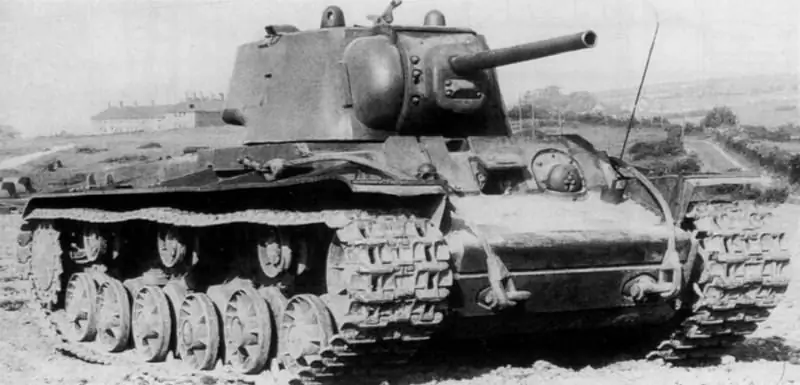
Sekret sukcesu
Tajemnica sukcesu metalurgów tkwi w badaniu parametrów powstawania włóknistego pęknięcia pancerza - głównego parametru odporności na pocisk. Okazało się, że można obejść się bez znacznej proporcji pierwiastków stopowych, po prostu zmieniając szybkość chłodzenia pancerza podczas hartowania. Ale to jest proste w słowach - ile wstępnych eksperymentów i wytopów musieli wykonać metalurdzy, tylko teraz utajnione archiwa będą w stanie powiedzieć.
W Zakładach Metalurgicznych Magnitogorsk w 1941 roku uzyskano pierwsze prototypy stali 49C, które nie ustępowały tradycyjnej „przedwojennej” zbroi. W szczególności ostrzał z 76-mm armaty wykazał pełną zgodność z wymaganiami taktycznymi dla czołgu. A od 1942 roku w serii KV używano tylko zbroi o nazwie 49C. Warto pamiętać, że znacząco spadło zużycie chromu, molibdenu i niklu.
Na tym nie zakończyły się poszukiwania nowych formuł opancerzenia dla ciężkiego sprzętu. W 1942 r. stal GD-63-3 została „spawana”, całkowicie pozbawiona deficytowego chromu i niklu. W pewnym stopniu nikiel został zastąpiony manganem - jego udział wzrósł ponad trzykrotnie (do 1,43%). Ostrzelano prototypy nowej zbroi. I okazały się całkiem odpowiednie do masowego użytku przy projektowaniu KV. Ale czołgi Klim Woroszyłow z pancerzem o średniej twardości odchodziły na emeryturę. A miejsce ciężkich pojazdów zajęły pojazdy „Józef Stalin” z opancerzeniem o wysokiej twardości.
Pancerz walcowany 51C
Jeśli można było oddać opancerzenie 70L wieży IS-2, ta sztuczka nie działała z częściami kadłuba czołgu. Tutaj inżynierowie stanęli jednocześnie przed dwoma problemami - stworzeniem pancerza o wysokiej twardości o dużej grubości i koniecznością wspawania go w gotowy kadłub.
Każdy zainteresowany zapewne już zdaje sobie sprawę z problemów spowodowanych spawaniem pancerza T-34 - istnieje duże prawdopodobieństwo pęknięcia w obszarze spawów. IS-2 nie był wyjątkiem. A jego ciało pierwotnie miało być gotowane z części poddanych ostatecznej obróbce cieplnej.
Zdając sobie sprawę z trudności i niebezpieczeństw, jakie takie rozwiązanie technologiczne przyniesie w operacjach wojskowych, specjaliści TsNII-48 zmienili cykl produkcyjny czołgów. W rezultacie w 1943 r. W Uralskim Zakładzie Budowy Maszyn Ciężkich i zakładzie w Czelabińsku nr 200 postanowiono ugotować kadłub IS-2 z płyt pancernych, które po toczeniu przeszły tylko długie wakacje. Oznacza to, że w rzeczywistości kadłub czołgu ciężkiego został zmontowany z „surowej” stali. To znacznie zmniejszyło defekty spawalnicze na pancerzu walcowanym o wysokiej twardości 51C.
Ostateczną obróbkę cieplną przez ogrzewanie przed hartowaniem przeprowadzono już na spawanym korpusie zbiornika, uprzednio wzmocniwszy go wewnętrznymi rozpórkami. Ciało trzymano w piecu przez trzy godziny. A następnie, na specjalnych urządzeniach, przeniesiono je do zbiornika wodnego i trzymano w nim przez 15 minut. Ponadto temperatura wody w wannie hartowniczej wzrosła z 30 do 55°C. Temperatura powierzchni ciała po wyjęciu z wody wynosiła 100-150 ° С. A to jeszcze nie wszystko.
Po hartowaniu korpus natychmiast poddano niskiemu odpuszczaniu w piecu obiegowym w temperaturze 280-320 ° С z utrzymywaniem po osiągnięciu tej temperatury przez 10-12 godzin. W podobny sposób przeprowadzono niskie hartowanie wież odlewanych z pancerza 70L. Co ciekawe, kontrola pęknięć w eksperymentalnych kadłubach IS-2 trwała cztery miesiące, kiedy pierwsze czołgi produkcyjne opuściły bramy fabryki.
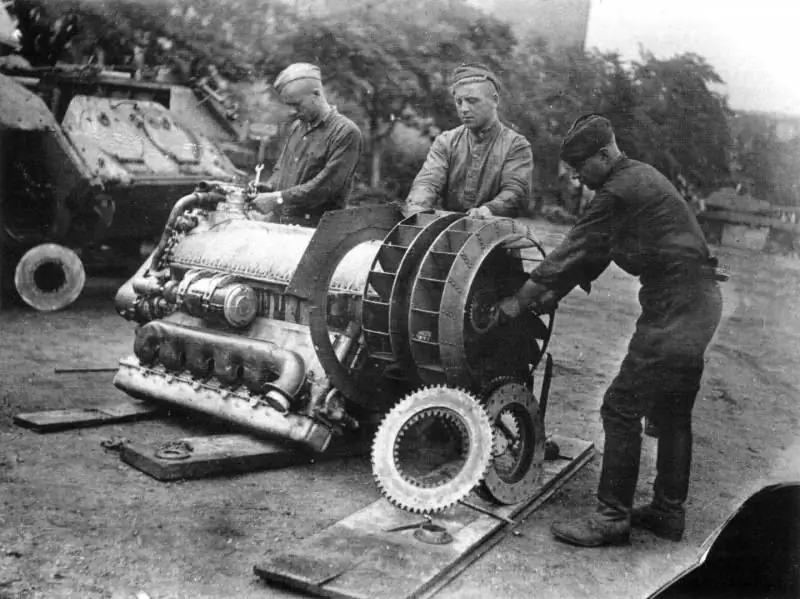
Skład chemiczny
Jaki był walcowany pancerz 51C, który stał się głównym pancerzem dla IS-2, ISU-122 i ISU-152? Jest to stal głęboko hartująca na duże grubości pancerzy o następującym składzie chemicznym (%):
C 0, 18-0, 24
Mn 0, 70-1, 0
Si 1, 20-1, 60
Cr 1, 0-1, 5
Ni 3,0-3,8
Po 0, 20-0, 40
P ≤0,035
S ≤0,035.
W porównaniu z pancerzem odlewanym 70L stal walcowana 51C miała wyższy udział molibdenu i niklu, co gwarantowało wzrost hartowności do 200 mm. Kiedy kadłuby czołgów ciężkich były wystrzeliwane pociskami 88 mm, okazało się, że pancerz o wysokiej twardości był znacznie bardziej wytrzymały niż jego poprzednicy o średniej twardości. Kwestia umieszczenia pancerza walcowanego 51C została natychmiast rozwiązana.
Inteligentne spawanie
Ważny wkład w sukces rozwoju produkcji opancerzenia czołgów serii IS miało automatyczne spawanie stali pod warstwą topnika. Ponieważ na początku 1944 roku nie było możliwe przeniesienie całego procesu produkcji opancerzonego kadłuba czołgu na takie spawanie, inżynierowie skupili się na automatyzacji najbardziej rozszerzonych i obciążonych mechanicznie szwów.
W czelabińskim zakładzie nr 200 w procesie montażu kadłuba czołgu ciężkiego IS-2 zautomatyzowano zaledwie 25% wszystkich spoin. Do połowy 1944 roku Tankograd był w stanie zautomatyzować 18% wszystkich możliwych 25% spoin. Łączna długość spawanych szwów wzdłuż kadłuba czołgu ciężkiego IS-2 wynosiła 410 mb, z czego 80 mb wykonano metodą zautomatyzowanego spawania.
Wynik ten doprowadził do znacznych oszczędności w ograniczonych zasobach i energii elektrycznej. Udało się uwolnić do 50 wykwalifikowanych spawaczy ręcznych (ich koszty pracy w wysokości 15 400 roboczogodzin) i zaoszczędzić 48 000 kilowatogodzin energii elektrycznej. Zmniejszone zużycie elektrod (około 20 000 kg, austenityczne - 6000 kg), tlenu (o 1440 metrów sześciennych).
Znacznie skrócił się również czas poświęcony na spawanie. Na przykład spawanie dna i skrzyni wieży do boków szesnastometrowym szwem zajęło 9,5 roboczogodziny w trybie ręcznym, a tylko 2. Wymagany jest szew o podobnej długości łączący dno z bokami kadłuba czołgu w trybie automatycznym 3 roboczogodziny (w instrukcji od razu 11, 4). Jednocześnie wysoko wykwalifikowani spawacze mogliby zostać zastąpieni przez niewykwalifikowanych robotników w spawaniu automatycznym.
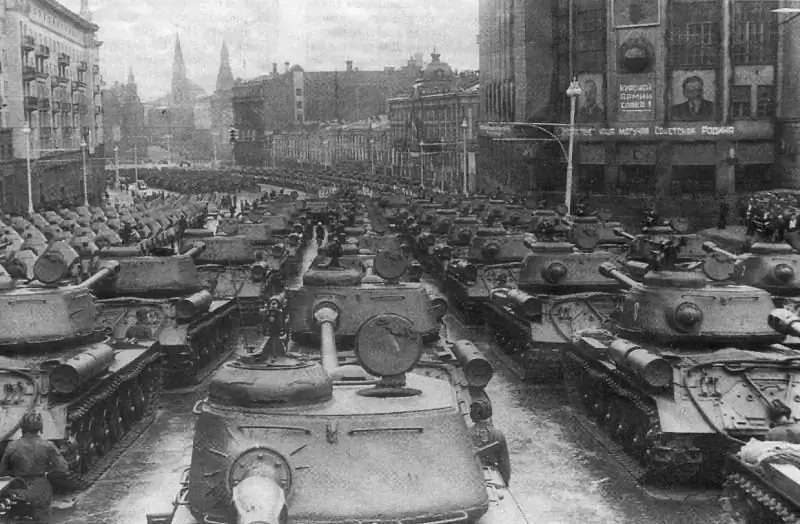
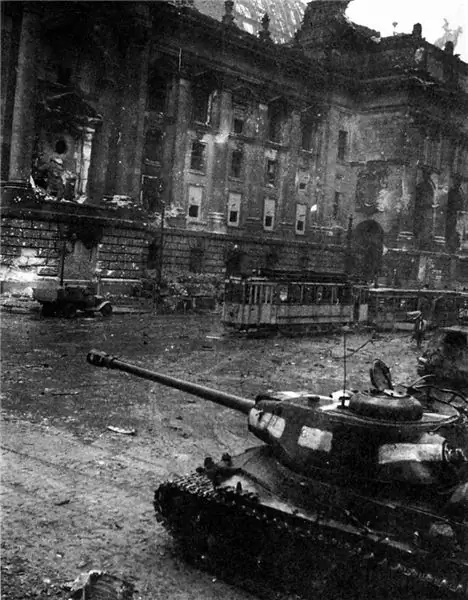
Ural SAG
Badacz radzieckiego przemysłu czołgów, kandydat nauk historycznych Zapariy Wasilij Władimirowicz z Instytutu Historii i Archeologii Uralskiego Oddziału Rosyjskiej Akademii Nauk w jednej ze swoich prac bardzo szczegółowo opisuje automatyczne jednostki spawalnicze stosowane na Uralu do pancernych produkcja kadłuba.
Najbardziej rozpowszechniony był karabin szturmowy typu „ACC” z głowicą Bushtedt. W Uralmaszu było osiem takich instalacji. Prędkość podawania drutu w tej maszynie zależała od napięcia w łuku. Wymagało to 5 jednostek, w tym 3 kinematycznych silników elektrycznych i 1 generatora silnikowego.
Do połowy 1943 roku spawarka SA-1000 została zaprojektowana na potrzeby czołgów ciężkich IS-2. Lub spawarkę o wydajności do 1000 A.
Aby opanować produkcję pancernych kadłubów dla nowego ciężkiego czołgu czelabińskiego IS-3, inżynierowie fabryki w 1944 roku zaprojektowali aparat „SG-2000”. Maszyna ta została zaprojektowana do pracy z niskowęglowymi drutami spawalniczymi o zwiększonej średnicy (6-8 mm) i znalazła zastosowanie w produkcji wieży IS-3. Instalacja posiadała dozownik do wprowadzania specjalnej kompozycji (różne żelazostopy) do odcinka spawanego w celu odtlenienia (odtworzenia) znajdującego się w nim metalu. W sumie na zasadzie samoregulacji łuku spawalniczego w UZTM do 1945 r. Utworzono 9 instalacji autospawalniczych trzech typów: „SA-1000”, „SG-2000”, „SAG” („Automatyczne spawanie głowa ).
Piękniejsza niż niemiecka zbroja
Rezultatem całej historii z opancerzeniem ciężkich czołgów IS było zaskakująco szybkie opracowanie receptury stali, która przewyższała niemieckie opancerzenie pod względem właściwości taktycznych. TsNII-48 otrzymał hartowaną stal 120 mm, której grubość w razie potrzeby można było zwiększyć do 200 mm.
Stało się to głównym fundamentem rozwoju powojennej rodziny ciężkich radzieckich czołgów.