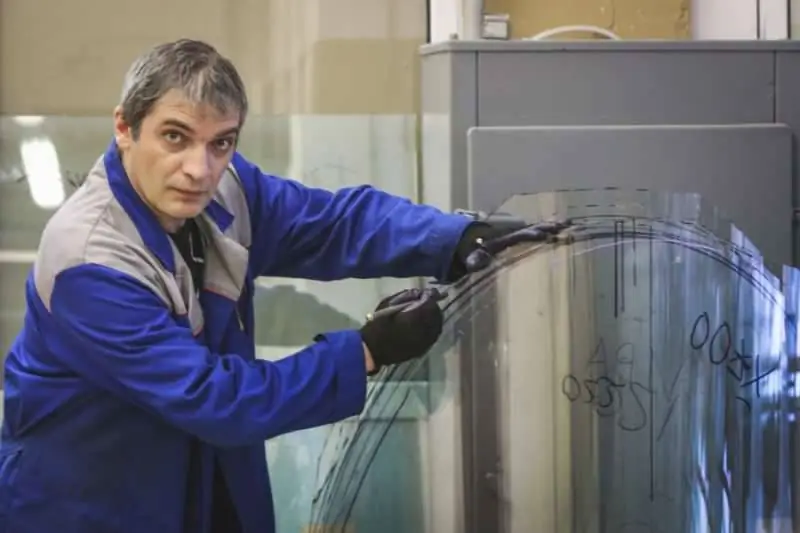
W Rosji opracowano nowe technologie do produkcji oszklenia kabin samolotów wojskowych i cywilnych ze szkła krzemianowego. Takie produkty okazują się lżejsze i mocniejsze, niż gdyby były tworzone z wcześniej stosowanych materiałów organicznych. Szkło krzemianowe jest również wykorzystywane w innych dziedzinach, od eksploracji kosmosu po budownictwo mieszkaniowe.
Od kilku lat wśród badaczy kosmosu toczy się debata na temat oceny bezpieczeństwa i działania Międzynarodowej Stacji Kosmicznej. Faktem jest, że w rosyjskim segmencie ISS zainstalowano 13 okien. Podczas wspólnych dyskusji na MSK proponuje się zamykanie okien w segmencie rosyjskim zaślepkami ze względu na niebezpieczeństwo defektów szkła w wyniku uderzeń mikrometeorytów - mówią, bezpieczeństwo stacji mogłoby się poprawić. Ale przedstawiciel strony rosyjskiej - dyrektor Instytutu Badań Naukowych Szkła Technicznego (NITS), Czczony Naukowiec, Wiceprezes Akademii Nauk Inżynierskich Federacji Rosyjskiej, doktor Nauk Technicznych, profesor Władimir Solinow stoi na swoim miejscu - przez wiele lat zachowana została wytrzymałość szczątkowa po uderzeniu mikrocząstek kosmicznych, a różne promieniowanie i inne zagrożenia z kosmosu nie wpłynęły na bezpieczeństwo okien tworzonych w instytucie, jak i załogi, dlatego nie ma powodów do ograniczania obserwacja naszej planety „zaciemnia” pracę kosmonautów w rosyjskich modułach stacji orbitalnej.
Iluminatory do stacji orbitalnej to tylko jeden z nielicznych produktów firmy NITS. Główna część pracy naukowców i technologów instytutu zlokalizowanego w południowo-zachodniej części Moskwy wiąże się oczywiście z tworzeniem optyki strukturalnej, szklenia, lub jak mówią tutaj „złożonych przezroczystych układów optycznych” dla samolotów bojowych czwartej i piątej generacji produkowanych przez zakłady ZAK. A pracy w lotnictwie z roku na rok jest znacznie więcej.
Krzemianowe lub organiczne
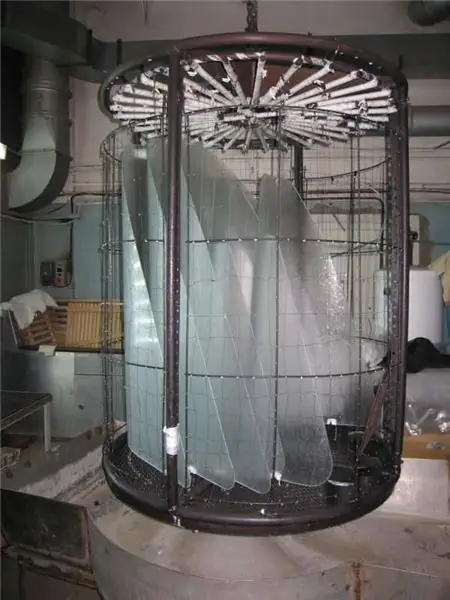
Na zdjęciu: półfabrykaty szyb T-50 w kasecie utwardzającej.
Szkło silikatowe to materiał o wyjątkowych właściwościach. Jego przezroczystość, wysoka optyka, odporność na ciepło, wytrzymałość oraz możliwość zastosowania różnych powłok sprawiają, że jest niezastąpiony w szybach lotniczych. Ale dlaczego priorytetowo traktowano materię organiczną przy szkleniu kabin samolotów za granicą iw naszym kraju? Tylko z jednego powodu - jest łatwiej. Mówią też, że szkło krzemianowe jest zbyt kruche.
W ciągu ostatnich kilku lat rozwój naukowców zajmujących się materiałami NITS umożliwił radykalną zmianę koncepcji szkła krzemianowego jako materiału kruchego. Nowoczesne metody wzmacniania pozwalają nadać szybom nowoczesnym samolotom bojowym wystarczającą wytrzymałość, aby wytrzymać uderzenie ptaka ważącego około dwóch kilogramów z prędkością 900 km/h.
„Dziś metoda utwardzania w warstwie wierzchniej wyczerpała się. Czas zmienić wewnętrzną strukturę szkła, jego wadliwość”- mówi Władimir Solinow. Choć może się to wydawać dziwne, ułatwiają to sankcje nałożone przez Zachód. Faktem jest, że nawet w czasach „przedsankcyjnych” firmy zagraniczne decyzją NATO nie dostarczały do Rosji okularów krzemianowych o lepszej jakości, które były tam używane do specjalnych celów. To zmusiło NITS do użycia szkła architektonicznego. Chociaż rosyjscy producenci produkują miliony metrów kwadratowych takiego szkła, jego jakość nie nadaje się do zastosowania w lotnictwie.
Na ratunek przyszła substytucja importu: w Moskwie uruchomiono nowy projekt badawczo-rozwojowy i projekt urządzeń, które były zasadniczo nowe dla przemysłu szklarskiego.
Na nim będą testowane wszystkie procesy syntezy szkła o rosyjskim priorytecie.
Projekt powierzono młodej naukowcowi Tatianie Kiseleva. 26-letni absolwent Rosyjskiego Uniwersytetu Technologii Chemicznej. Kierownikiem laboratorium jest D. I. Mendelejewa, w 2015 roku obroniła pracę magisterską. Na wydziale szkła w Mendelejewce Tatiana badała właściwości przezroczystej zbroi. Jednym z jej zawodowych wyzwań jest opracowanie szkła, które przewyższałoby właściwościami jeden z najlepszych analogów na świecie - szkło herkulitowe, którego Rosja jeszcze nie wyprodukowała.
Projekt oparty jest na nowej autorskiej metodzie wytapiania szkła. Już dziś laboratorium pozyskało próbki szkła, którego wytrzymałość strukturalna jest trzykrotnie wyższa niż analogów uzyskiwanych metodą tradycyjną. Dodaj do tego istniejące metody hartowania, a otrzymasz szkło, którego wytrzymałość jest kilkakrotnie wyższa niż wielu rodzajów stali stopowej. Bardziej wytrzymałe szkło sprawia, że produkty są lżejsze. Należy jednak zauważyć, że twórcy szkła organicznego stale poprawiają parametry techniczne swoich produktów, spór o to, które szkło jest lepsze, jeszcze się nie skończył.
Latarnia do T-50
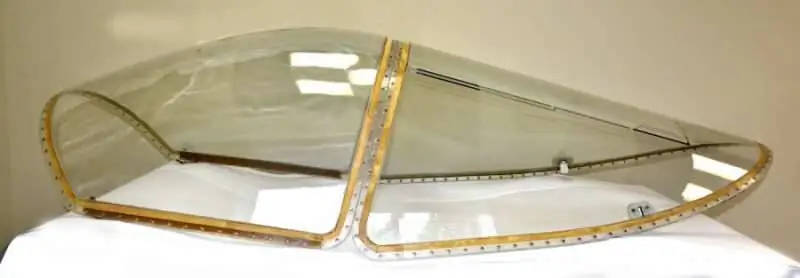
Na zdjęciu: komplet szyb do samolotu T-50 - przednia przyłbica i składana część.
Wyobraź sobie pakiet kilku płytek ze szkła krzemionkowego, które chcesz usprawnić przednią osłonę szybkiego samolotu.
Około czterdzieści lat temu specjaliści NITS opracowali technologię głębokiego gięcia. W specjalnym piecu układa się kilka warstw szkła. Przez kilka godzin w wysokich temperaturach pod własnym ciężarem szkło wygina się, nabierając pożądanego kształtu i krzywizny. W razie potrzeby specjalne mechanizmy popychają obrabiany przedmiot, zmuszając go do zginania zgodnie ze specjalnym harmonogramem.
Po raz pierwszy na świecie, korzystając z tej technologii, myśliwiec MiG-29 zastąpił latarnię, która składała się z trzech szyb, jedną szybą wolną od krzemianów.
Wraz ze wzrostem prędkości rosły wymagania dotyczące odporności termicznej oszklenia, z którym szkło organiczne nie mogło już sobie poradzić. Jednocześnie zaostrzono wymagania dotyczące optyki i widoczności. Kilka lat temu, we współpracy z Sukhoi Company, United Aircraft Corporation, opracowano nową technologię produkcji szkła do T-50.
Rozwój był finansowany przez producentów samolotów, częściowo przez Ministerstwo Przemysłu i Handlu. Udzielono znacznej pomocy w przeprowadzeniu technicznego ponownego wyposażenia przedsiębiorstwa, mówi Jurij Tarasow, dyrektor Centrum Technologicznego ZAK.
W rezultacie przednia szyba samolotu T-50 jest prawie dwukrotnie większa od wizjera MiG-29, a kształt produktu z klasycznego cylindra zamienił się w skomplikowany format 3D.
Efekt - po raz pierwszy na świecie przednia i składana część osłony samolotu T-50 (produkowanego przez Sukhoi) została wykonana ze szkła krzemianowego w formacie 3D. Co więcej, waga tych części okazała się mniejsza, niż gdyby były wykonane ze szkła organicznego.
Osiągnięte wyniki dały impuls do wyposażenia samolotów innych fabryk i biur projektowych należących do ZAK w podobne szyby. Natychmiast pojawiła się potrzeba modernizacji, polegającej na zastąpieniu oszklenia organicznego krzemianem np. na samolotach Jak-130, Su-35, MiG-31, MiG-35. Po takiej wymianie (czyli poprawie charakterystyki wytrzymałościowej szyby) np. MiG-35 po raz pierwszy osiągnął prędkość do 2000 km/h, czyli był w stanie latać o 40% szybciej średnio niż jakikolwiek inny samolot na świecie.
W ostatnich latach styl pracy moskiewskich naukowców poważnie się zmienił. Około trzystu specjalistów NITS wykonuje pełny cykl - od specyfikacji technicznych po produkcję na małą skalę. Obejmuje to rozwój technologii i dobór kluczowych materiałów przy użyciu szkła oraz duży cykl testów dla wszystkich czynników wpływających na samolot, zarówno na ziemi, jak i w powietrzu.
Na nowoczesne szkło nakłada się kilka kluczowych wymagań, wśród których oprócz wysokiej wytrzymałości są: przezroczystość optyczna, wysoka przepuszczalność światła, zwiększenie zasięgu widzenia, właściwości antyrefleksyjne, ochrona przed skutkami promieniowania słonecznego i innego promieniowania, ochrona przed oblodzeniem właściwości, zapewniając równomierną oporność elektryczną.
Wszystko to osiąga się poprzez powlekanie aerozolem, próżnią lub magnetronem. Potężny i wyrafinowany sprzęt odparowujący metal i osadzający go na powierzchni szkła pozwala NITS na nakładanie dowolnych powłok, w tym chroniących przed czynnikami specjalnymi.
Ten zestaw właściwości pozwala mówić o wyrobie szklarskim jako o złożonym układzie optycznym, a wysokie właściwości wytrzymałościowe szkła, które jest częścią kokpitu samolotu, stworzyły nową dziedzinę nauki i techniki i wprowadziły pojęcie „optyki strukturalnej”. produkty” (ICO).
Nowe technologie
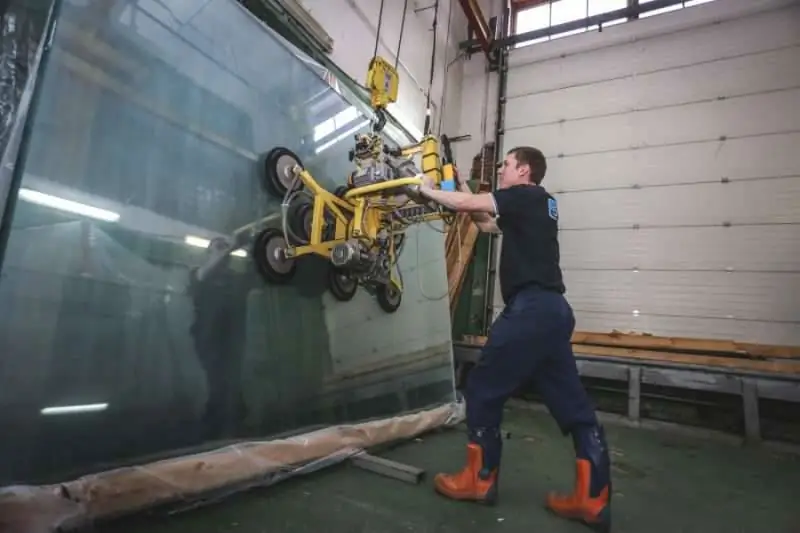
Na zdjęciu: ładowanie tafli szkła do dalszej obróbki.
Kiedy produkt - zawiasowa część latarni dla T-50 - jest rozładowywany z pieca do dalszej obróbki, prawie nie przypomina przyszłego produktu. Podczas gięcia szkła krawędzie przedmiotu obrabianego ulegają deformacji i nie można ich usunąć z dużego przedmiotu obrabianego, który ma złożony kształt geometryczny, za pomocą narzędzia diamentowego. Na ratunek przyszedł laser. Wiązka laserowa kompleksu zrobotyzowanego nie tylko tnie przedmiot zgodnie z określonym w nim programem, ale także poprzez topienie krawędzi zwiększa wytrzymałość krawędzi produktów, zapobiegając pojawianiu się pęknięć. Cięcie laserowe wielkogabarytowych produktów 3D po raz pierwszy zastosowano w Moskwie. Ta metoda została opatentowana w marcu 2012 roku. Wiązka laserowa służy również do odcinania warstwy przewodzącej prąd elektryczny na powierzchni szkła, tworząc strefy grzewcze. Po obróbce laserowej przedmiot coraz bardziej przypomina latarkę T-50.
Po wycięciu każdy przedmiot obrabiany jest na maszynie pięcioosiowej. Unikalne ułożenie pozwala na zapewnienie zerowych wstępnych naprężeń montażowych. Główny technolog instytutu Alexander Sitkin mówił o perspektywach wykorzystania kompleksu do szlifowania i polerowania powierzchni szkła: praca, która w razie potrzeby jest wykonywana tylko ręcznie. Opracowane technologie są chlubą instytutu.
Niedawno w metalowej ramie zamontowano gotowy szklany blok za pomocą szczeliwa. Przejście na materiały kompozytowe opracowane przez NITS umożliwiło zmniejszenie ciężaru produktu o 25%, zwiększenie odporności na ptaki i zasobów oszklenia do poziomu zasobów oszklenia. Możliwa stała się wymiana przeszklenia w terenie.
Cały cykl produkcyjny ICO trwa około półtora miesiąca. Większość produktów trafia do zakładów produkcyjnych ZAK, część do remontów zakładów do modernizacji, a część na lotniska Sił Powietrznych w tzw. apteczkach. Główna część produktów NITS realizowana jest w ramach państwowego zamówienia obronnego.
NITS niechętnie dzieli się informacjami o właściwościach oszklenia samolotów bojowych. Ale jasne jest, że okulary opracowane do kokpitów krajowych samolotów cywilnych przewyższają te importowane pod wieloma parametrami.
Przykładowo, jak widać na stronie NITS, grubość szkła w Tu-204 to 17 mm, grubość szkła o tych samych właściwościach dla Boeinga 787 to 45 mm.
Generacja V
W ciągu ostatnich kilku lat dyrektorowi instytutu Władimirowi Solinowowi udało się znacząco odmłodzić zespół. W moskiewskiej produkcji, która niedawno obchodziła swoje 60-lecie, pracują zarówno młodzi ludzie, jak i doświadczeni specjaliści. Chętnie przyjeżdżają tu starsi studenci Mendelejewki. Przychodząc na praktykę w instytucie i dowiadując się, że są pensje w wysokości 70 tysięcy rubli, początkowo są zatrudniani przez zwykłych pracowników, a potem szybko osiągają poziom technologów. Jest też wielu doświadczonych pracowników.
Jeden z nich, Nikołaj Jakunin, zajmuje się obróbką szkła do helikopterów. „Przybyłem tu zaraz po wojsku, czterdzieści lat temu. Ale gdyby nie wysoki poziom automatyzacji, prawdopodobnie by nie przetrwał. Ciężko mi pracować przez cały dzień, nawet w dobrej kondycji fizycznej, z produktem o wadze 30 kg”- mówi Yakunin.
Ludzie i paznokcie
Na całym świecie technologie opracowane do budowy samolotów, które pozwalają na produkcję okularów o wymaganej wytrzymałości, znajdują zastosowanie w wielu innych sektorach gospodarki narodowej.
Kilka lat temu, aby udowodnić wysoką wytrzymałość szkła krzemianowego, instytut wykonał… szklane gwoździe. Bili mnie młotkiem. Mogą znaleźć zastosowanie w produktach o właściwościach antymagnetycznych.
Również te gwoździe były testowane podczas budowy, zamiast zacisków podczas klejenia kadłubów jachtów. Ale paznokcie pozostały tylko egzotyczne. Teraz już nikt nie musi udowadniać wysokiej wytrzymałości szkła - wszystkie prace NITS są dowodem wysokiej jakości tego antycznego, a zarazem zupełnie nowego materiału.
Dyrektor Instytutu Władimir Solinow wykorzystuje wszystkie swoje możliwości, aby udowodnić konieczność zapewnienia wysokiej wytrzymałości szkła, w tym architektonicznego i konstrukcyjnego.
Jest członkiem Rosyjsko-Amerykańskiej Komisji Bezpieczeństwa Kosmicznego, o którym była mowa na początku tego artykułu, a także Komisji Rozwoju Miast przy Dumie Państwowej - wszak przy budowie nowoczesnych budynków coraz większy udział z materiałów to szkło. Oznacza to, że technologie i materiały opracowane dla lotnictwa sprawią, że w niedalekiej przyszłości życie milionów ludzi stanie się wygodniejsze i bezpieczniejsze.