Patriotyzm sowieckiej elity przemysłowej łączył się ze współodpowiedzialnością za efekt końcowy
Interakcje międzybranżowe przez cały czas - zarówno w Imperium Rosyjskim, jak iw ZSRR, a także dzisiaj - nie należały do mocnych stron krajowego przemysłu. W przeciwieństwie do Niemiec czy Stanów Zjednoczonych, gdzie zobowiązania umowne miały i mają niezmienną i niemal świętą moc.
Weźmy na przykład relacje między rosyjskimi metalurgami a konstruktorami maszyn. W drugiej połowie XIX wieku nowe zakłady inżynierii transportu i stocznie nie otrzymywały od uralskich górników wymaganej ilości metali przemysłowych. Ten ostatni uznał za nieopłacalne wytwarzanie wielu stosunkowo tanich wyrobów walcowanych, ponieważ taki sam zysk zapewniał znacznie mniejszy wolumen drogiego żelaza do pokryć dachowych. Brakujący metal do osi samochodowych, wałów silników i poszycia okrętu trzeba było kupić za granicą. Dopiero pod koniec stulecia problem rozwiązały południowo-rosyjskie zakłady metalurgiczne, założone przez belgijskich lub francuskich przemysłowców. Na Uralu Francuzi zbudowali także jedną fabrykę - Chusovskaya.
Wydawałoby się, że w czasach sowieckich takie kaprysy nie wchodziły w rachubę. Ponadto wybudowane w latach 30. zakłady metalurgiczne zaopatrywały cały kraj w metal. Jednak za każdym razem, gdy konstruktorzy maszyn żądali nowych skomplikowanych rodzajów wyrobów walcowanych, hutnicy opanowywali je przez lata, a nawet dziesięciolecia.
Feudalizm departamentalny
Przejdźmy do historii Uralwagonzawodu. Już w pierwszych projektach planowano zastosowanie pod wagony czteroosiowe pełnych stalowych kół walcowanych, ponieważ możliwości projektowe osiągnęły już swoje możliwości projektowe, których dostawcę planowano do pobliskiego Zakładu Metalurgicznego Novo-Tagil. Ta ostatnia była jednak budowana przez wydział metalurgiczny i przesunęła budowę walcowni kołowej na 1938-1942, a nie w pierwszej kolejności. W rezultacie sprawa nie rozpoczęła się przed wojną. A po wojnie hutnicy nie interesowali się wypożyczaniem kół. Rezultat: do połowy lat 50. samochody Tagil opuszczały fabrykę na krótkotrwałych żeliwnych kołach zamiast stalowych. Przyniosło to ogromne straty kolejarzom, ale nie było wyboru: albo takie samochody, albo żadne.
To samo stało się z wprowadzeniem stali niskostopowych do budowy wagonów. Obiecali zauważalne zmniejszenie ciężaru własnego taboru kolejowego przy zachowaniu wszystkich właściwości użytkowych. Konstruktorzy Uralvagonzawodu rozpoczęli projektowanie samochodów wykonanych z niskostopowego metalu pod koniec lat 30-tych, ale ich seryjna produkcja rozpoczęła się dopiero w drugiej połowie lat 50-tych, ponieważ metalurdzy nie dostarczali ani odpowiednich wyrobów walcowanych, ani żelazostopów do odlewania części.
Trzeba powiedzieć, że wirus feudalizmu resortowego dotknął samych konstruktorów maszyn. Latem 1937 miała miejsce ciekawa historia, która charakteryzowała ówczesne relacje międzyagencyjne. Główna Dyrekcja Przedsiębiorstw Metalurgicznych wysłała do Uralvagonzawodu zamówienie na pięć tysięcy ton półfabrykatów do niedawno uruchomionej wytwórni bandaży Zakładu Novo-Tagil. Główna Dyrekcja Inżynierii Transportu była oburzona ingerencją w podległe przedsiębiorstwo. Zastępca Szefa Zarządu Głównego G. G.11 lipca Aleksandrow wysłał list do GUMP i Uralwagonzawod z następującym oświadczeniem: „Jesteśmy niezwykle zaskoczeni, że rozwiązanie tak ważnej kwestii, jak zorganizowanie produkcji wykroju bandażowego na Uralwagonzawodzie, zostało przeprowadzone bez naszego udziału, a tym bardziej - nie wysłano nam nawet kopii stroju wysłanego na Uralvagonzavod … Proszę o ustalenie sztywnej procedury wydawania półfabrykatów do naszych fabryk tylko w porozumieniu z nami i za pośrednictwem Glavtransmash”.
W rezultacie metalurgom odmówiono stali opatrunkowej, rzekomo z powodu technicznej niemożności odlewania wysokiej jakości wlewków w sklepie z otwartym paleniskiem Uralwagonzawodu. Tymczasem już w 1936 r. odlano tu półfabrykat osiowy, aw 1937 r. wlewki do walcowania blach. Dlatego wlewki do młyna całunowego, położonego kilka kilometrów od UVZ, musiały być transportowane z zakładów Vyksa i Kuznetsk. Ponadto ich jakość pozostawiała wiele do życzenia, a wielkość dostaw była niewystarczająca.
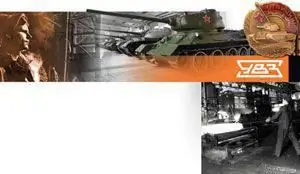
W 1938 roku historia się powtórzyła. Głównym konsumentem sztabek UVZ był Zakład Artylerii Mołotowa (czyli Perm), który pod koniec roku otrzymał partię wykrojów. I tylko niewielka ich część poszła do sklepu z bandażami, który znowu musiał sprowadzić brakujący metal na dwa, dwa i pół tysiąca kilometrów. Wyraźnie przeważały interesy przemysłu w dystrybucji stali Uralwagonzawodsk.
Choroba resortowa nie oszczędziła też przemysłu obronnego. Liczne publikacje na temat historii radzieckiej budowy czołgów są wręcz pełne przykładów opóźnień budowy prototypów lub wprowadzenia do masowej produkcji z powodu niedostarczenia metalu, zwłaszcza opancerzenia.
I nawet dzisiaj sektorowy interes własny nigdzie nie zniknął, zmienił jedynie swoją formę. Prośby o nowe kształty wyrobów walcowanych są po prostu zwalczane wygórowanymi cenami. Nie ma potrzeby mówić o skoordynowanej polityce. Po załamaniu kursu rubla na przełomie lat 2014-2015 firmy metalurgiczne podniosły ceny na tabor o 30-60 proc. I natychmiast zaczęli narzekać na konstruktorów maszyn na sprzęt, który podrożał - w końcu maszyny są produkowane w Rosji i nie są powiązane z kursem dolara.
Wydaje się, że w naszym kraju jest tylko jedno lekarstwo na problemy międzysektorowe: tworzenie pionowo zintegrowanych systemów, w których wydobywaną własnymi siłami rudę zamieniamy najpierw na metal, a następnie na gotowe maszyny.
Wojenna jedność
W naszej historii jest jednak krótki okres, w którym interesy przemysłu zeszły na dalszy plan. Mówimy o Wielkiej Wojnie Ojczyźnianej. Niewątpliwy patriotyzm ówczesnej radzieckiej elity przemysłowej łączył się ze wspólną odpowiedzialnością wszystkich zaangażowanych w produkcję obronną za efekt końcowy. Oznacza to, że dyrektor pancernej walcowni był odpowiedzialny nie tyle za ilość wytopionej i walcowanej stali, ile za liczbę zbudowanych czołgów.
Główny krok w tym kierunku wykonał dyrektor NII-48 A. S. Zavyalov. Na początku wojny zwrócił się do rządu z propozycją polecenia instytutowi wprowadzenia technologii produkcji stali specjalnych i konstrukcji pancernych w przedsiębiorstwach na wschodzie kraju, które jako pierwsze zajmowały się produkcją pancernych pojazdy. Na początku lipca zespoły specjalistów z NII-48 kierowały restrukturyzacją technologiczną 14 największych przedsiębiorstw. Wśród nich były zakłady metalurgiczne Magnitogorsk i Kuznieck, zakłady metalurgiczne Novo-Tagil i Chusovka, Ural Heavy Machine Construction Plant, Gorki Krasnoye Sormowo, Stalingradzka Fabryka Traktorów, Stalingrad Czerwony Październik i nr 264. W ten sposób Zawiałow naruszył zasady przedwojenne tabu: na liście znalazły się przedsiębiorstwa trzech komisariatów ludowych.
Patriotyzm i przymusowe tłumienie resortowego egoizmu zapewniły sowieckiej metalurgii bezprecedensowe tempo rozwoju produktów obronnych ani w okresie przedwojennym, ani powojennym. W ciągu kilku miesięcy na wschodzie kraju (głównie na Uralu) zorganizowano produkcję żelazomanganu, żelazokrzemu, żelazochromu, żelazowanadu i innych stopów, bez których nie można uzyskać stali pancernej. Po utracie zachodnich regionów Czelabińsk pozostał jedyną fabryką żelazostopów w ZSRR. Na nim w krótkim czasie wytop został zwiększony o dwa i pół razy. Wytworzono 25 rodzajów produktów, ale przede wszystkim różnego rodzaju ferrochromy. Wytop żelazomanganu rozpoczęto w wielkich piecach, a nie tylko w małotonażowych starych wielkich piecach Niżnego Tagila i Kushvinsky'ego, ale także w dużym nowoczesnym piecu Kombinatu Magnitogorskiego. Wbrew wszelkim przedwojennym pomysłom, w drugiej połowie 1941 r. ferrochrom został wytopiony w ich wielkich piecach przez hutników zakładów Niżny Tagil i Sierow, a naukowcy z Uralskiego Oddziału Akademii Nauk ZSRR wnieśli wielką pomoc w stworzeniu nowego technologia. Później wytop żelazokrzemu został opanowany w wielkich piecach Serov.
Przed wojną nie było obozów pancernych ani na Uralu, ani na Syberii Zachodniej, trzeba je było pośpiesznie przenosić z przedsiębiorstw znajdujących się w strefie walk.
Latem 1941 r. ewakuowany sprzęt był jeszcze w tranzycie. A potem główny mechanik Kombinatu Magnitogorsk N. A. Ryzhenko zasugerował zwinięcie zbroi na kwitnącym młynie. Mimo dużego ryzyka pomysł został zrealizowany. A w październiku do służby wszedł obóz pancerny, wywieziony z zakładów Mariupol. Został zmontowany w zaledwie 54 dni. Według przedwojennych standardów trwało to rok.
Zakład Novo-Tagil dostał obóz z Leningradu. Przygotowania do jego przyjęcia rozpoczęły się w lipcu, początkowo zakładano, że zostanie on zamontowany w miejscu bandaża. Obóz bandaży został zdemontowany, ale okazało się, że stary inwentarz nie wystarczył do zainstalowania obozu pancernego i trzeba go było umieścić w innym miejscu. Wojna zmusiła do zrobienia tego, co do niedawna uważano za niemożliwe: zaledwie rok temu próby realizacji budownictwa przemysłowego zintegrowaną metodą „szybkich” w Niżnym Tagile odniosły co najwyżej częściowy sukces, a latem 1941 r. najbardziej skomplikowana operacja budowlana była niemal perfekcyjna. 10 września pierwsza blacha Tagil została zwinięta na miesiąc przed terminem. Łącznie do końca roku uzyskano 13 650 ton blach, w tym ok. 60 proc. pancerzy (walcowanie testowano na stali węglowej, a w okresie październik - grudzień walcowano stal węglową przy braku wlewków pancerza). W efekcie już w styczniu 1942 r. miesięczna produkcja płyt pancernych w fabrykach Uralu przekroczyła pół roku w całym przedwojennym Związku Radzieckim.
Nie mniej zaskakujące wydarzenia miały miejsce w innych mało znanych przedsiębiorstwach. W czasie wojny Zakład Metalurgiczny Zlatoust był gorszy od Kombinatu Magnitogorskiego pod względem ilości wytopu i walcowanej stali, ale znacznie przewyższał go asortymentem - wyprodukowano tu około 300 gatunków stali stopowej i węglowej. Bez dostaw ze Złatoustu produkcja wielu rodzajów broni, przede wszystkim silników czołgowych, zostałaby wstrzymana.
Stare zakłady w Uralu okazały się nieodzowne w produkcji niewielkich partii stali szczególnie wysokiej jakości. Na przykład w każdy radziecki czołg zainwestowano metal z Serov Metallurgical, głównego producenta kalibrowanych wyrobów walcowanych. Fabryka w Nizhnesaldzie przeszła na wytop niklu i stali. Tę listę można kontynuować bez końca - w latach wojny, gdziekolwiek była przynajmniej jedna kopuła, topił się metal do broni.
Jest ciekawa historia z topnikami do automatycznego spawania. Przed i na początku wojny przetopiono je w jednym z przedsiębiorstw Donbasu, po zajęciu którego scentralizowane dostawy całkowicie ustały. Pod koniec 1941 r. pracownicy Instytutu Spawania Elektrycznego Akademii Nauk Ukraińskiej SRR rozpoczęli poszukiwania materiałów zastępczych dostępnych na Uralu w stanie mniej lub bardziej użytecznym. I znaleźli je - w postaci żużli wielkopiecowych hutnictwa Ashinskiy. Potrzebne były tylko drobne ulepszenia: wielkie piece wzbogaciły swoje żużle w mangan i tym samym zamieniły je w całkowicie odpowiedni topnik. Sprzęt niezbędny do testów został sprowadzony z Niżnego Tagila bezpośrednio do Ashy.
Przykłady współpracy lokalnej zbiorników i zakładów metalurgicznych są bardzo orientacyjne. Przed uruchomieniem własnych obiektów w zakładzie metalurgicznym Niżny Tagil przeprowadzono obróbkę cieplną części zbiornika Ural Tank Plant nr 183.
Pomyślną pracę odlewni UTZ znacznie ułatwiła pomoc sąsiedniej fabryki szamotu Niżny Tagil, która rozpoczęła produkcję wysokiej jakości ogniotrwałych zatyczek krzemiennych. Umożliwiło to bezproblemowe odlewanie wytopów ciężkiej stali pancernej do odlewania kształtowego.
W latach 1942-1945 piece martenowskie w UTZ pracowały głównie na gazie koksowniczym i wielkopiecowym z Hutniczej Nowo-Tagil i Koksowni Niżny Tagil. Gazociąg jest eksploatowany od lutego 1942 roku. Własna gazownia Zakładu nr 183 zaspokajała nie więcej niż 40 procent potrzeb.
Czasami do rozwiązania problemu wystarczyła prosta rada. Informacje od miejscowych metalurgów o małej kopalni manganu powstałej w latach 70. XIX wieku pozwoliły przetrwać kilka tygodni przed rozpoczęciem dostaw żelazomanganu bez przerywania odlewania torów czołgowych.
Inny przykład: wraz ze wzrostem produkcji stali pancernej warsztat martenowski nie mógł już nadążyć z wytopem metalu na głowice bomb lotniczych. Nie można było go zdobyć z zewnątrz. Reżyser Yu E. Maksarev wspominał przebieg dalszych wydarzeń w swoich wspomnieniach: „Kiedy byłem na jednym ze spotkań w komitecie miejskim, spotkałem dyrektora starej, wciąż jeszcze zakładu Demidova i poprosiłem o odebranie mi castingu głowice bomb. Powiedział: nie mogę pomóc ze stalą, ale radą pomogę. A kiedy przyjechałem do jego zakładu, pokazał mi półtoratonowy konwerter Bessemera ze średnim nadmuchem. Dał mi rysunki i powiedział, że wie, że mamy dobrą zmechanizowaną odlewnię żeliwa, a wasze konwertery spawają”. Tak pojawiło się zamówienie na fabrykę z 8 września 1942 r. na zorganizowanie w felgach Griffin sekcji Bessemer trzech małych konwertorów (półtora tony metalu każdy). Do 25 września projekt został przygotowany przez dział projektowo-technologiczny kierownictwa budowy kapitału, specjaliści z wydziału głównego mechanika szybko spawali konwertory i kotły - zbiorniki do przechowywania ciekłego żelaza. Przebieg próbny wydziału Bessemera i odlanie doświadczalnej partii pięciu nazw części odbyło się na przełomie października i listopada 1942 roku. Produkcja seryjna rozpoczęła się pod koniec listopada.
Na koniec temat: współpraca hutników i budowniczych czołgów w czasie wojny działała w obu kierunkach. Instalatorzy Ural Tank Plant uczestniczyli w uruchomieniu wielu nowych jednostek Zakładu Metalurgicznego Novo-Tagil. W maju 1944 r. w odlewni wież pancernych wyprodukowano znaczną liczbę płyt okładzinowych do remontu wielkiego pieca.
Ale głównym pomocnikiem metalurgów był oczywiście Uralski Zakład Budowy Ciężkich Maszyn. Księgi zamówień UZTM na lata 1942-1945 dosłownie zapełnione są dokumentami dotyczącymi produkcji części zamiennych i urządzeń do celów hutniczych - zarówno na potrzeby przemysłu czołgów, jak i przedsiębiorstw Ludowego Komisariatu Metalurgii Żelaza. Jesienią 1942 r. w UZTM oficjalnie odtworzono specjalny dział produkcji urządzeń dla zakładów metalurgicznych. Otrzymał kod „Oddział 15” i podlegał zastępcy dyrektora ds. zaopatrzenia i produkcji kadłubów.
Sukces na skrzyżowaniu branż
Współpraca metalurgów i budowniczych czołgów doprowadziła do powstania szeregu technologii, które bez przesady można nazwać prawdziwymi przełomami naukowymi i technicznymi.
Po stopieniu i zwinięciu stali pancernej na arkusze metalurdzy przenieśli swoje wyroby do produkcji kadłubów pancernych. Tutaj metal został pocięty zgodnie z szablonem na odpowiednie części. Przy produkcji "trzydziestej czwórki" szczególnie dużo kłopotów sprawiały dwie części kadłuba: błotniki (pochylona strona burty) i pionowa płyta boczna. Oba były długie, nawet w szerokości pasów z ukośnymi cięciami wzdłuż krawędzi.
Pomysł naturalnie nasunął się na zrolowanie taśmy pomiarowej o szerokości równej gotowym częściom. Po raz pierwszy został sformułowany przez samochody pancerne fabryki Mariupol latem 1941 roku. Do próbnego walcowania wybraliśmy walcownię w Zaporoże, do której wysłano dwa rzuty wlewków zbroi. Ale potem nie mieli czasu, aby zabrać się do pracy: zbliżające się wojska niemieckie schwytały zarówno eszelony, jak i samo Zaporoże.
Na przełomie 1941-1942, podczas ewakuacji i rozwoju produkcji zbroi w nowych fabrykach, zabrakło pasa. Jednak w maju 1942 r. Ludowy Komisariat Metalurgii Żelaza ponownie otrzymał polecenie wynajęcia go na czołgi T-34 i KV. Zadanie okazało się trudne: tolerancje szerokości nie powinny przekraczać -2 / + 5 milimetrów, kształt półksiężyca (zgięcie) dla całkowitej długości części wynosił 5 milimetrów. Pęknięcia, zachody słońca i rozwarstwienia na krawędziach nie były dozwolone, aby spawanie można było przeprowadzić bez obróbki skrawaniem lub cięcia płomieniowego.
Prace eksperymentalne rozpoczęły się jednocześnie w walcowniach hut Magnitogorsk i Kuznieck, początkowo bez żadnych szczególnych osiągnięć. Wkrótce zrezygnowano z wypożyczania części do czołgów KV, ale T-34 w końcu odniósł sukces. Zespół autorów składający się z kierownika wydziału metalurgicznego NII-48 G. A. Vinogradov, głównego inżyniera KMK L. E. Vaisberg i inżyniera tego samego zakładu S. E. stoisk „900” walcowni szynowo-konstrukcyjnej jest zupełnie nowy metoda toczenia „na krawędzi”. W styczniu 1943 wydano 280 sztuk, w lutym 486, w marcu 1636 sztuk. W kwietniu, po wszystkich wymaganych testach, rozpoczęto opracowywanie produkcji brutto listew pomiarowych do tulei nadkoli czołgów T-34. Początkowo trafiały do UZTM i Uralskiej Fabryki Czołgów, a następnie do innych fabryk - producentów czołgów T-34. Złom, który pierwotnie wynosił 9,2 procent, spadł do 2,5 procent do października 1943 roku, a taśmy niespełniające norm zostały wykorzystane do produkcji mniejszych części.
Kompletną i dokładną ocenę nowej technologii podaje odpowiedni raport TsNII-48 z dnia 25 grudnia 1943 r.: Opracowano, przetestowano i wprowadzono do produkcji masowej „zasadniczo nową metodę walcowania szerokiej taśmy pancernej” na krawędzi, co do niedawna było uważane za niewykonalne w ZSRR i za granicą. Uzyskanie skalibrowanej (zmierzonej) taśmy o szerokości gotowej części kadłuba pancernego czołgu T-34 umożliwiło fabrykom NKTP przyjęcie nowej wysokowydajnej technologii wytwarzania części pancernych bez cięcia wzdłużnych krawędzi. Dzięki zastosowaniu nowej metody do jednego z głównych elementów opancerzonych czołgu T-34 (błotników) uzyskano bardzo dużą oszczędność czasu (około 36%) przy ich wycinaniu. Osiągnięto oszczędności stali pancernej 8C do 15 procent i oszczędności tlenu 15 000 m3 na 1000 kadłubów”.
Do końca 1943 r. opanowano walcowanie taśmy pomiarowej dla innej części kadłuba T-34 - pionowej części burty. Pozostaje tylko dodać, że autorom tego wynalazku przyznano Nagrodę Stalina za rok 1943.
W tym samym 1943 r. wspólnymi siłami laboratorium Ukraińskiego Instytutu Metali (kierowanego przez PA Aleksandrowa) oraz pracowników Kuźnieckiego Kombinatu Metalurgicznego i Uralskich Zakładów Zbiornikowych opracowano i opanowano do produkcji specjalny profil okresowy walcowany na zamówienie. części masowych i krytycznych „trzydziestu czterech” - osi balansera. Pierwsza eksperymentalna partia o profilu okresowym została odebrana w KMK w grudniu, na początku 1944 roku rozpoczęto produkcję seryjną. Do października Ural Tank Plant całkowicie przestawił się na produkcję osi balansera z nowego blanku, pod koniec roku dołączył do niego UZTM. W rezultacie wydajność młotów kuźniczych wzrosła o 63 procent, a liczba pęknięć części spadła.
Pomyślną pracę budowniczych czołgów znacznie ułatwił tabor walcowni bandaży Zakładu Metalurgicznego Novo-Tagil. Od wiosny 1942 r. dostarczali zwijane paski naramienne ze zmniejszonymi naddatkami na obróbkę, w 1943 r. naddatki zostały ponownie zmniejszone. W połączeniu z nowym narzędziem tnącym umożliwiło to czasochłonne zdejmowanie pasów naramiennych ściśle zgodnie z harmonogramem i bez większego stresu. Rzadki przypadek: Komisarz Ludowy Przemysłu Pancernego V. A. Malyshev, w swoim rozkazie z 28 września 1943 r., Uznał za konieczne wyrażenie szczególnej wdzięczności metalurgom Tagil.
I wreszcie ostatni przykład: w 1943 roku felgi czołgów pomocniczych T-34, najpierw w zakładzie Czelabińsk Kirowa, a następnie w innych przedsiębiorstwach, zaczęto wytwarzać ze specjalnie profilowanych wyrobów walcowanych. Ten sukces został również odnotowany w kolejności V. A. Malysheva.
Pozostaje dodać, że specjaliści amerykańskiej firmy „Chrysler”, po przestudiowaniu zdobytego w Korei czołgu T-34-85, szczególnie zauważyli doskonałość stalowych półfabrykatów, z których wykonano pojazd bojowy. A także fakt, że często przewyższali liczebnie produkty amerykańskich przedsiębiorstw metalurgicznych.