Na początku sierpnia 2016 r. US Navy pomyślnie przetestowała tiltrotor Osprey MV-22. Sam samolot nie jest niczym niezwykłym. Dwuwirnikowy pojazd od dawna służy amerykańskiej marynarce wojennej (do służby trafił w drugiej połowie lat 80.), ale po raz pierwszy w historii krytyczne części zostały zamontowane na tiltrotorze (bezpieczeństwo lotu). bezpośrednio od nich zależy), które zostały wydrukowane na drukarce 3D.
Do testów wojsko USA wydrukowało z tytanu wspornik do mocowania silnika do skrzydła tiltrotora za pomocą bezpośredniego spiekania laserowego warstwa po warstwie. W tym samym czasie na samym wsporniku zamontowano czujnik tensometryczny, mający na celu rejestrację ewentualnego odkształcenia części. Każdy z dwóch silników tiltrotora Osprey MV-22 jest przymocowany do skrzydła za pomocą czterech takich wsporników. W tym samym czasie, w czasie pierwszego testowego lotu tiltrotora, który miał miejsce 1 sierpnia 2016 roku, zainstalowano na nim tylko jeden wspornik wydrukowany na drukarce 3D. Wcześniej informowano, że mocowania gondoli wydrukowane metodą druku trójwymiarowego zostały również zainstalowane na tiltrotorze.
Opracowaniem wydrukowanych części do tiltrotora zajęło się Centrum Operacji Bojowych Marynarki Wojennej USA znajdujące się w McGuire-Dix-Lakehurst Joint Base w New Jersey. Testy w locie Osprey MV-22 z częściami drukowanymi przeprowadzono w bazie US Navy Patxent River, testy zostały uznane przez wojsko za całkowicie udane. Amerykańskie wojsko uważa, że dzięki powszechnemu wprowadzeniu druku trójwymiarowego technologia w przyszłości będzie w stanie szybko i stosunkowo tanio produkować części zamienne do konwerterów. W takim przypadku niezbędne szczegóły można wydrukować bezpośrednio na statkach. Ponadto drukowane części można następnie modyfikować w celu poprawy wydajności pokładowych zespołów i systemów.
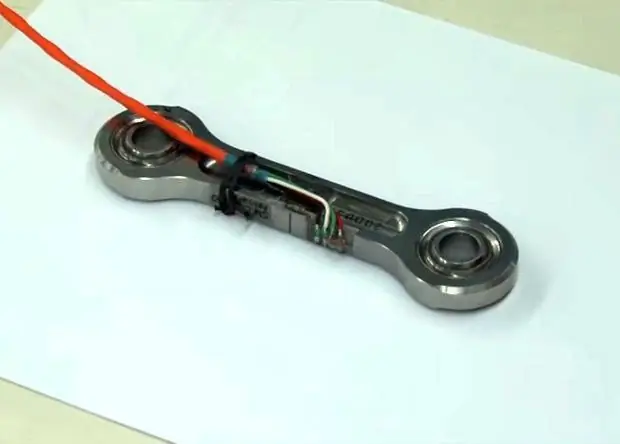
Wspornik do montażu silnika z nadrukiem tytanowym
Amerykańskie wojsko już kilka lat temu interesowało się technologiami druku 3D, ale do niedawna funkcjonalność drukarek 3D nie była wystarczająco szeroka, aby można było ich rutynowo używać do budowy dość skomplikowanych części. Części do tiltrotora zostały stworzone za pomocą addytywnej drukarki 3D. Część jest wykonywana stopniowo warstwami. Co trzy warstwy pyłu tytanowego spajane są laserem, proces ten jest powtarzany tak długo, jak jest to konieczne do uzyskania pożądanego kształtu. Po zakończeniu nadmiar jest odcinany od części; powstały element jest całkowicie gotowy do użycia. Ponieważ testy zakończyły się sukcesem, wojsko amerykańskie nie poprzestanie na tym, zamierza zbudować 6 ważniejszych elementów konstrukcyjnych tiltrotora, z których połowa będzie również tytanem, a druga stalą.
Druk 3D w Rosji i na świecie
Pomimo tego, że produkcja typu drukarka została z powodzeniem wdrożona kilka lat temu w USA i Rosji, tworzenie elementów do sprzętu wojskowego jest w trakcie finalizowania i testowania. Przede wszystkim wynika to z bardzo wysokich wymagań stawianych wszystkim produktom militarnym, głównie pod względem niezawodności i trwałości. Jednak nie tylko Amerykanie robią postępy w tej dziedzinie. Już drugi rok z rzędu rosyjscy projektanci produkują części do opracowanych karabinów i pistoletów w technologii druku 3D. Nowe technologie oszczędzają cenny czas rysowania. A wprowadzenie takich części do sieci może zapewnić szybką wymianę w terenie, w batalionach naprawczych, ponieważ nie będzie trzeba czekać na fabryczne części zamienne do tych samych czołgów czy bezzałogowych statków powietrznych.
Dla okrętów podwodnych wojskowe drukarki 3D będą po prostu na wagę złota, ponieważ w przypadku autonomicznej nawigacji dalekobieżnej wymiana części przez samych okrętów podwodnych da okrętowi podwodnemu niemal niewyczerpane zasoby. Podobną sytuację obserwuje się w przypadku statków odbywających długie rejsy i lodołamaczy. Większość z tych statków otrzyma w niedalekiej przyszłości drony, które ostatecznie będą wymagały naprawy lub całkowitej wymiany. Jeśli na statku pojawi się drukarka 3D, która umożliwi szybkie drukowanie części zamiennych, to za kilka godzin sprzęt będzie mógł być ponownie użyty. W warunkach przemijania operacji i dużej mobilności teatru działań wojennych, lokalny montaż niektórych części, zespołów i mechanizmów na miejscu pozwoli na utrzymanie wysokiego poziomu sprawności jednostek wsparcia.
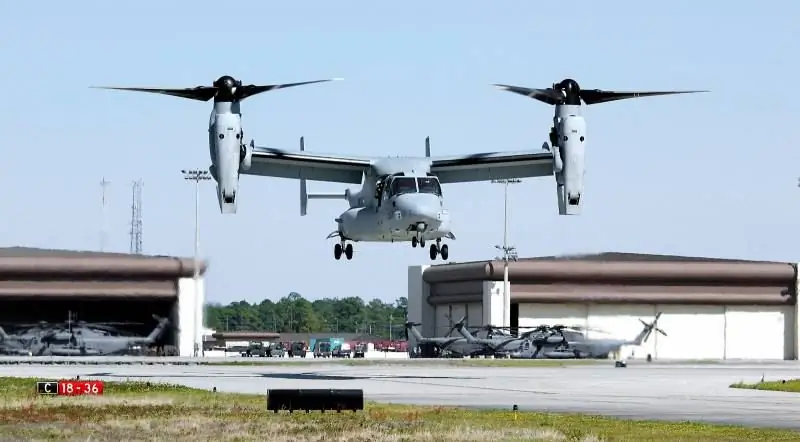
Rybołów MV-22
Podczas gdy wojsko amerykańskie wypuszcza na rynek swoje konwersaplany, rosyjscy producenci czołgu Armata już drugi rok używają drukarki przemysłowej na Uralwagonzawodzie. Za jego pomocą produkowane są części do pojazdów opancerzonych, a także wyroby cywilne. Ale do tej pory takie części są używane tylko do prototypów, na przykład były używane przy tworzeniu czołgu Armata i jego testach. W Koncernie Kałasznikowa, a także w TsNIITOCHMASH, na zlecenie rosyjskich wojskowych, projektanci wykonują różne części broni strzeleckiej z metalowych i polimerowych chipów za pomocą drukarek 3D. Biuro projektowe Tula Instrument, nazwane na cześć Shipunowa, słynnego CPB, znanego z bogatego asortymentu produkowanej broni: od pistoletów po precyzyjne pociski, nie pozostaje w tyle. Na przykład obiecujący pistolet i karabin szturmowy ADS, który ma zastąpić siły specjalne AK74M i APS, składa się z elementów z tworzywa sztucznego o wysokiej wytrzymałości, które są drukowane na drukarce. W przypadku niektórych wyrobów wojskowych CPB była już w stanie wykonać formy, obecnie trwają prace nad montażem seryjnym wyrobów.
W warunkach, gdy na świecie obserwuje się nowy wyścig zbrojeń, ważny staje się termin wypuszczania nowych rodzajów broni. Na przykład w pojazdach opancerzonych sam proces tworzenia modelu i przenoszenia go z rysunków do prototypu trwa zwykle rok lub dwa. Przy opracowywaniu okrętów podwodnych okres ten jest już 2 razy dłuższy. „Technologia druku 3D skróci ten czas kilkukrotnie do kilku miesięcy” - zauważa Aleksiej Kondratyew, ekspert w dziedzinie marynarki wojennej. - Projektanci będą mogli zaoszczędzić czas na rysunkach podczas projektowania modelu 3D na komputerze i natychmiast wykonać prototyp pożądanej części. Bardzo często części są przerabiane z uwzględnieniem przeprowadzonych testów oraz w trakcie rewizji. W takim przypadku możesz zwolnić zespół zamiast części i sprawdzić wszystkie właściwości mechaniczne, jak części współdziałają ze sobą. Ostatecznie czas prototypowania pozwoli projektantom skrócić całkowity czas, w którym pierwsza gotowa próbka wchodzi na etap testów. Obecnie stworzenie atomowej łodzi podwodnej nowej generacji zajmuje około 15-20 lat: od szkicu do ostatniej śruby podczas montażu. Wraz z dalszym rozwojem przemysłowego druku trójwymiarowego i uruchomieniem w ten sposób masowej produkcji części, ramy czasowe mogą ulec skróceniu co najmniej 1,5-2 razy.”
Według ekspertów, nowoczesne technologie są od roku do dwóch lat od masowej produkcji części tytanowych na drukarkach 3D. Można śmiało powiedzieć, że do końca 2020 roku przedstawiciele wojskowi w przedsiębiorstwach kompleksu wojskowo-przemysłowego przyjmą sprzęt, który zostanie zmontowany w 30-50% przy użyciu technologii druku 3D. Jednocześnie największe znaczenie dla naukowców ma tworzenie na drukarce 3D części ceramicznych, które wyróżniają się wysoką wytrzymałością, lekkością oraz właściwościami osłony termicznej. Materiał ten jest bardzo szeroko stosowany w przemyśle kosmicznym i lotniczym, ale może być stosowany w jeszcze większych ilościach. Na przykład stworzenie silnika ceramicznego na drukarce 3D otwiera horyzont dla tworzenia samolotów hipersonicznych. Z takim silnikiem samolot pasażerski mógłby w ciągu kilku godzin przelecieć z Władywostoku do Berlina.
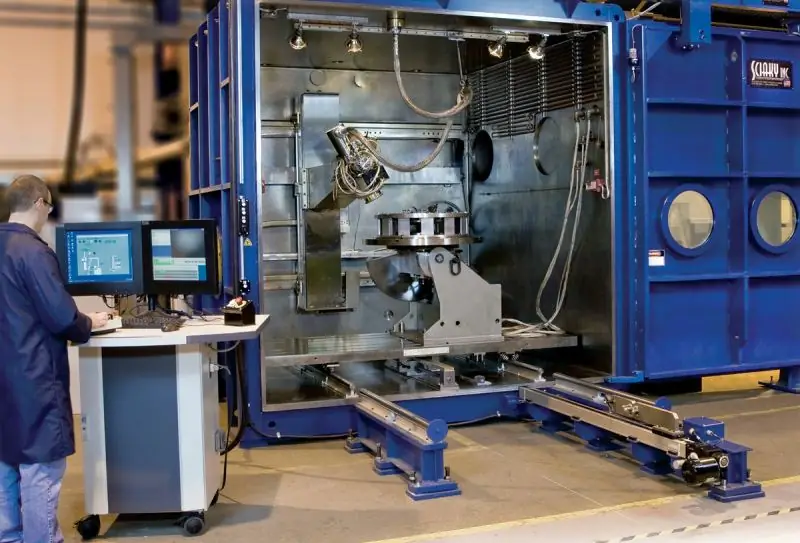
Doniesiono również, że amerykańscy naukowcy wynaleźli formułę żywicy specjalnie do drukowania w drukarkach 3D. Wartość tej formuły polega na wysokiej wytrzymałości otrzymanych z niej materiałów. Na przykład taki materiał może wytrzymać krytyczne temperatury przekraczające 1700 stopni Celsjusza, czyli dziesięciokrotnie więcej niż odporność wielu nowoczesnych materiałów. Stephanie Tompkins, dyrektor naukowy ds. zaawansowanych badań nad obronnością, szacuje, że nowe materiały tworzone za pomocą drukarek 3D będą miały unikalne kombinacje cech i właściwości, których nigdy wcześniej nie widziano. Tompkins twierdzi, że dzięki nowej technologii będziemy w stanie wyprodukować trwałą część, która jest zarówno lekka, jak i ogromna. Naukowcy uważają, że produkcja części ceramicznych na drukarce 3D będzie oznaczać przełom naukowy, także w produkcji wyrobów cywilnych.
Pierwszy rosyjski satelita 3D
Obecnie technologia druku 3D już z powodzeniem produkuje części bezpośrednio na pokładach stacji kosmicznych. Ale krajowi eksperci postanowili pójść jeszcze dalej, od razu postanowili stworzyć mikrosatelitę za pomocą drukarki 3D. Rocket and Space Corporation Energia stworzyła satelitę, korpus, wspornik i szereg innych części, które wydrukowano w 3D. Jednocześnie ważnym wyjaśnieniem jest to, że mikrosatelitę stworzyli inżynierowie Energii wraz ze studentami Politechniki Tomskiej (TPU). Pierwszy satelita drukarski otrzymał pełną nazwę „Tomsk-TPU-120” (numer 120 w nazwie na cześć 120-lecia uczelni, które obchodzono w maju 2016 r.). Został pomyślnie wystrzelony w kosmos wiosną 2016 roku wraz z sondą kosmiczną Progress MS-02, satelita został dostarczony do ISS, a następnie wystrzelony w kosmos. To urządzenie jest pierwszym i jedynym na świecie satelitą 3D.
Satelita stworzony przez studentów TPU należy do klasy nanosatelitów (CubSat). Ma następujące wymiary 300x100x100 mm. Ten satelita był pierwszym statkiem kosmicznym na świecie, który miał wydrukowany korpus w 3D. W przyszłości technologia ta może stać się prawdziwym przełomem w tworzeniu małych satelitów, a także sprawić, że ich wykorzystanie stanie się bardziej dostępne i rozpowszechnione. Projekt statku kosmicznego został opracowany w Centrum Naukowo-Edukacyjnym TPU „Nowoczesne Technologie Produkcyjne”. Materiały, z których wykonano satelitę, stworzyli naukowcy z Politechniki Tomskiej oraz Instytutu Fizyki Wytrzymałości i Materiałoznawstwa Syberyjskiego Oddziału Rosyjskiej Akademii Nauk. Głównym celem satelity było przetestowanie nowych technologii nauki o materiałach kosmicznych, pomoże on rosyjskim naukowcom przetestować kilka osiągnięć tomskiego uniwersytetu i jego partnerów.
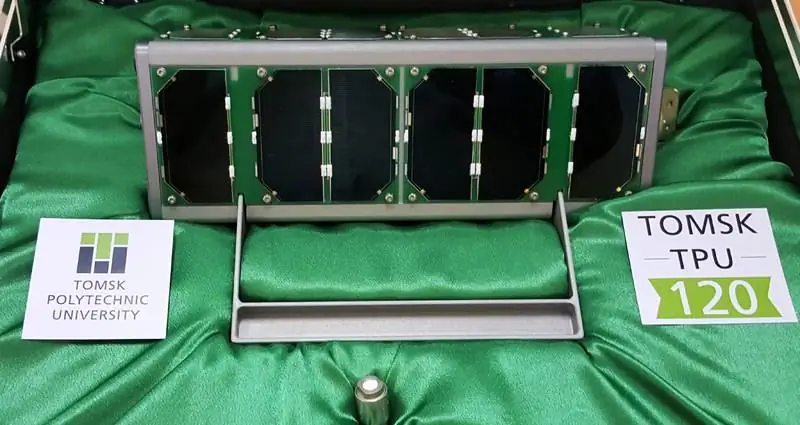
Jak poinformowała służba prasowa uczelni, wystrzelenie nanosatelity Tomsk-TPU-120 miało się odbyć podczas spaceru kosmicznego z ISS. Satelita jest dość kompaktowym, ale jednocześnie pełnoprawnym statkiem kosmicznym, wyposażonym w baterie, panele słoneczne, pokładowy sprzęt radiowy i inne urządzenia. Ale jego główną cechą było to, że jego ciało zostało wydrukowane w 3D.
Różne czujniki nanosatelity będą rejestrować temperaturę na pokładzie, na bateriach i płytkach oraz parametry elementów elektronicznych. Wszystkie te informacje zostaną następnie przesłane na Ziemię online. Na podstawie tych informacji rosyjscy naukowcy będą mogli przeanalizować stan materiałów satelitarnych i zdecydować, czy w przyszłości wykorzystają je w rozwoju i budowie statków kosmicznych. Należy zauważyć, że ważnym aspektem rozwoju małych statków kosmicznych jest również szkolenie nowych kadr dla przemysłu. Dziś studenci i nauczyciele Politechniki Tomskiej własnymi rękami opracowują, produkują i ulepszają projekty wszelkiego rodzaju małych statków kosmicznych, zdobywając nie tylko wysokiej jakości podstawową wiedzę, ale także niezbędne umiejętności praktyczne. To właśnie sprawia, że absolwenci tej instytucji edukacyjnej są wyjątkowymi specjalistami w przyszłości.
W planach na przyszłość rosyjskich naukowców i przedstawicieli przemysłu jest stworzenie roju satelitów uniwersyteckich. „Dzisiaj mówimy o potrzebie motywowania naszych studentów do studiowania wszystkiego, co w taki czy inny sposób jest związane z kosmosem - może to być energia, materiały, tworzenie silników nowej generacji itp. Mówiliśmy wcześniej, że zainteresowanie kosmosem w kraju nieco osłabło, ale można je ożywić. Aby to zrobić, trzeba zacząć nawet nie od ławki studenckiej, ale od szkolnej. W ten sposób wkroczyliśmy na ścieżkę rozwoju i produkcji CubeSata - małych satelitów”, - zauważa służba prasowa Tomskiego Instytutu Politechnicznego w odniesieniu do rektora tej wyższej uczelni, Petera Chubika.