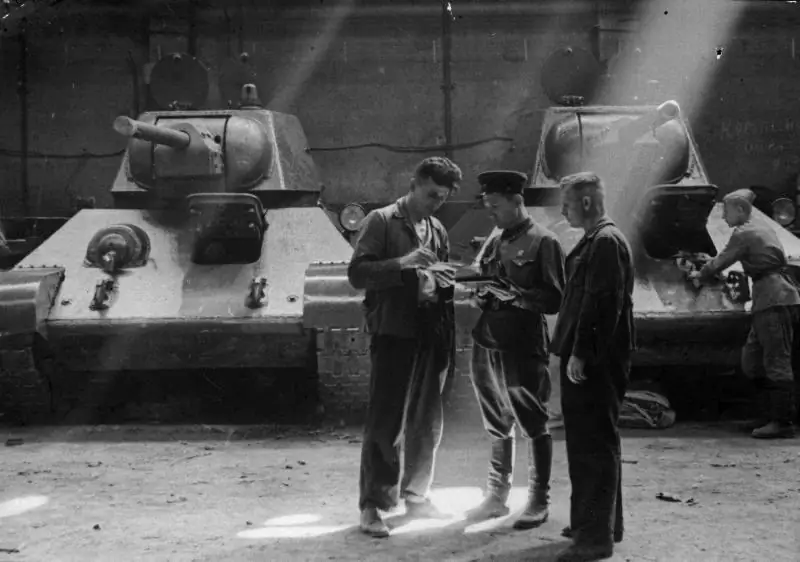
Wszystko na wojnę z trzaskiem
Wysoce solidna jednorodna stal pancerna 8C, która stała się główną stalą dla czołgu średniego T-34, wprowadziła wiele trudności w procesie produkcyjnym. Należy zauważyć, że taki solidny pancerz był używany na czołgach tylko w Związku Radzieckim podczas całej II wojny światowej. I w tym oczywiście były zarówno pozytywne, jak i negatywne aspekty. W poprzednich częściach cyklu omówiliśmy już liczne pęknięcia towarzyszące spawaniu kadłubów i wież radzieckich czołgów średnich. Jednocześnie ciężkie KV, a następnie IS zostały tego pozbawione: bardziej plastyczny pancerz o średniej twardości znosił nadmierne naprężenia przy znacznie łatwiejszym spawaniu części. Od początku 1942 r. inżynierowie Armored Institute zaproponowali zestaw środków mających na celu uproszczenie produkcji kadłubów pancernych i unowocześnienie technologii spawania. Postanowiono w ogóle nie spawać niektórych węzłów: na przykład mocowanie tylnej i przedniej ramy zostało przeniesione na nitowanie. Pod wieloma względami była to pożyczka po dokładnym przestudiowaniu niemieckich pojazdów opancerzonych.
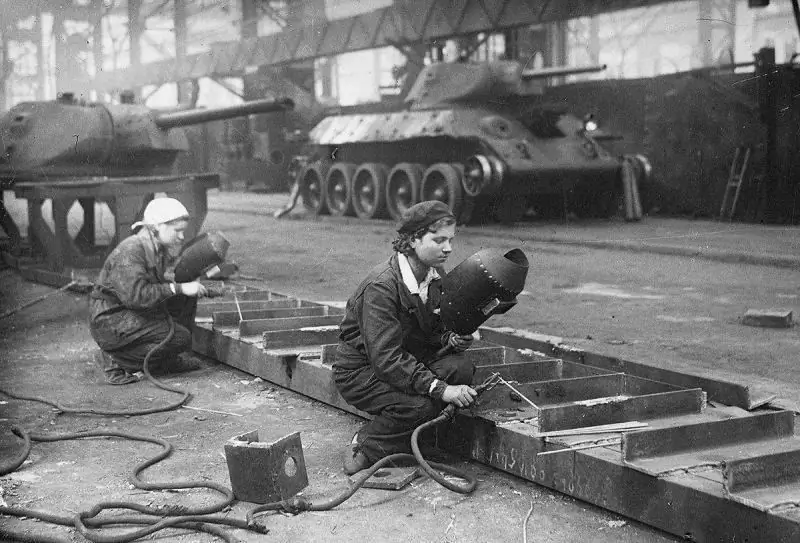
Przednie i boczne części czołgu były teraz spawane na życzenie TsNII-48 tylko za pomocą elektrod austenitycznych, lepiej przystosowanych do trudnych do spawania gatunków metali żelaznych. W sumie teraz do 10% (lub więcej) wszystkich elektrod zużywanych przez pojazd opancerzony to austenit. Jeśli skupisz się na danych podanych w książce Nikity Melnikowa „Przemysł czołgów ZSRR podczas Wielkiej Wojny Ojczyźnianej”, to na jeden T-34-76 zużyto około 400 elektrod, a 55 z nich było austenitami. Wśród wymagań dotyczących stosowania takich elektrod był zakaz ich pracy w trybach wysokoprądowych - do 320A. Przekroczenie tego wskaźnika groziło dużym nagrzewaniem się obszaru spoiny z późniejszym odkształceniem podczas stygnięcia i powstawaniem pęknięć. Przypominamy, że podobne funkcje do krajowego „Instytutu Pancernego” w Niemczech pełnił VI Wydział Zarządu Uzbrojenia Wojsk Lądowych. To jemu fabryki czołgów miały przedstawić do zatwierdzenia na piśmie metody spawania kadłubów i wież. Z kolei specjaliści VI Oddziału sprawdzali dostarczone materiały pod kątem zgodności z tymczasowymi specyfikacjami na pancerze spawalnicze T. L.4014, T. L.4028 i T. L.4032. Wymagania te zostały obliczone na spawanie niemieckiego pancerza o grubości od 16 do 80 mm. Jak już wspomniano w artykule „Spawanie pancerzy czołgów: niemieckie doświadczenie”, w Niemczech nie stosowano automatycznego spawania. To oczywiście poważnie spowolniło niemiecki przemysł czołgów, ale w Związku Radzieckim pojawiły się pewne problemy ze spawarkami. Wraz z niewątpliwą wysoką jakością spoiny automatyzacja spawania wymagała wysokiej jakości spoiw oraz ścisłego przestrzegania technologii pracy. Była to jednak nieunikniona cena za wprowadzenie rewolucyjnej metody produkcji, która miała tak znaczący wpływ na jakość i szybkość montażu czołgów.
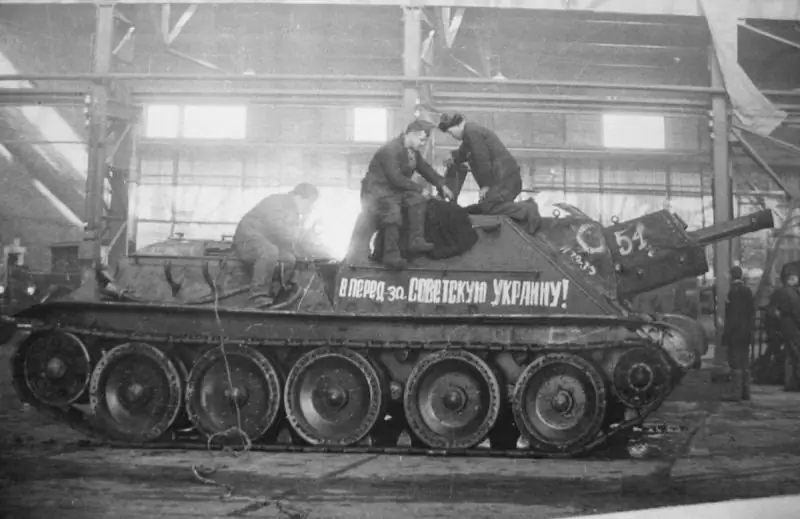
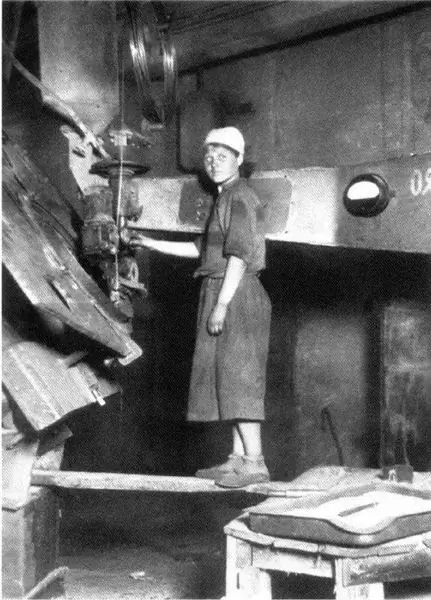
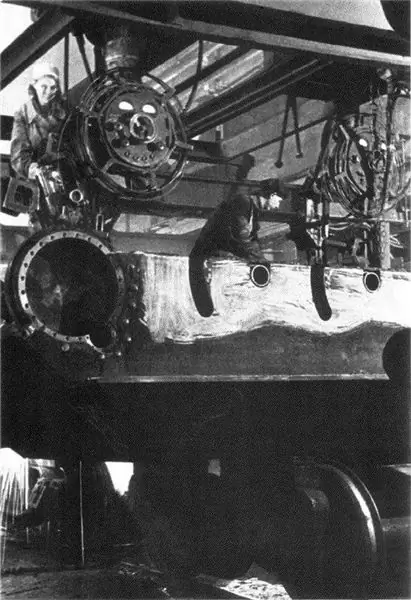
Jeżeli elektroda główna i drut spawalniczy okazały się nadmiernie zanieczyszczone siarką, węglem i fosforem (lub odwrotnie, brakowało w nim manganu lub tlenku manganu), prowadziło to do powstawania pęknięć bezpośrednio w spoinie. Ważne było staranne przygotowanie wyrobów do spawania pod topnikiem. Wymagania były surowe: części muszą mieć prawidłowe wymiary, bez naruszania tolerancji. W przeciwnym razie do spawania część na pochylni musiała zostać „wyciągnięta”, tworząc w ten sposób poważne naprężenia wewnętrzne. A proste nieprzestrzeganie siły i napięcia prądu spawania doprowadziło do wadliwości szwów: porowatości, nozdrzy i braku penetracji. Biorąc pod uwagę niski poziom kwalifikacji pracowników pozwalających na dostęp do spawarek, łatwo uwierzyć w możliwość wystąpienia takich wad. Wszyscy wysoko wykwalifikowani spawacze zajmowali się spawaniem ręcznym i nie mogli wpływać na jakość spawania "maszyn Patona". Chociaż byli zaangażowani w naprawę usterek w spawarkach.
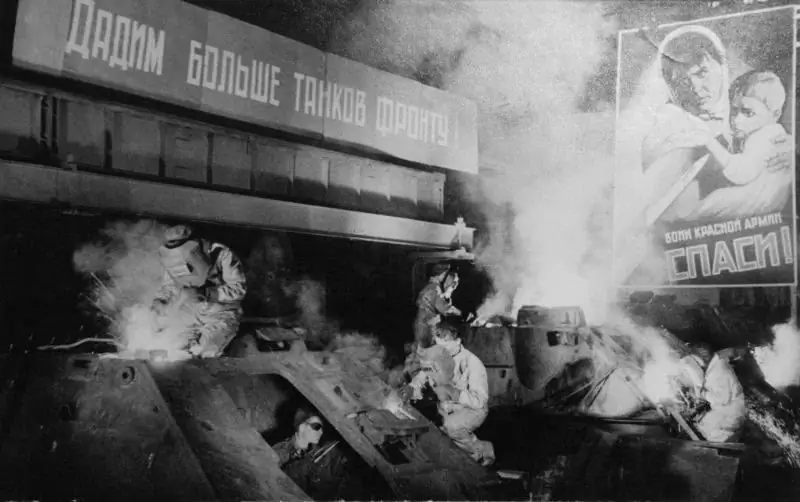
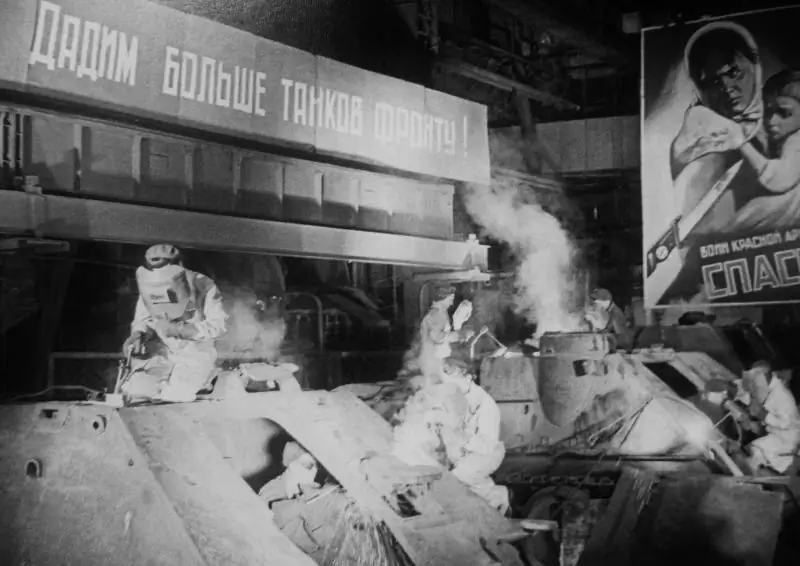
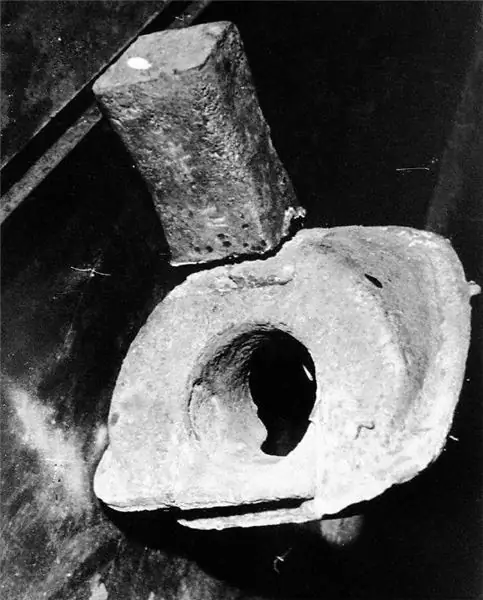
Dramatyczny wzrost wydajności fabryk czołgów doprowadził w 1943 roku do nieoczekiwanego problemu. Okazało się, że reszta produkcji nie zawsze nadążała za budową czołgów. Maszyny pracowały na zużycie, czasami brakowało amperomierzy do kontroli natężenia prądu na maszynach, brakowało wysokiej jakości elektrod spawalniczych. Wszystko to powodowało okresowe „wybuchy” pęknięć wśród seryjnych T-34. Aby zgasić te fale małżeństwa, musiały zostać wykonane przez siły operacyjne technologów i inżynierów z TsNII-48.
Rewizja projektu
Twardy pancerz i pęknięcia w nim zmusiły inżynierów do zmiany nie tylko technologii automatycznego spawania, ale także ręcznego podejścia. W szczególności duże naprężenia spawalnicze i termiczne wystąpiły w górnej części czołowej, gdy podczas linii montażowej spawano na niej ochronę karabinu maszynowego DT, oczka, pętlę włazu kierowcy, pręt ochronny i inne drobiazgi. Wokół osłony karabinu maszynowego, która została bardzo starannie wyparzona, często pojawiały się pęknięcia o długości do 600 mm! Spawanie było obszerne w obszarze dziobu boków, gdzie były mocowane za pomocą mocnych dwustronnych szwów z przednimi górnymi i dolnymi płytami, a także za pomocą wsporników leniwych. Często szczelina między częściami w tych częściach nie odpowiadała normatywnym, dlatego konieczne było umieszczenie szczególnie masywnego szwu spawalniczego, pozostawiając poważne naprężenia wewnętrzne. Wymagano zmniejszenia sztywności niektórych węzłów i zmniejszenia całkowitego udziału spawania w złączach, co zostało wykonane przez specjalistów TsNII-48 w możliwie najkrótszym czasie. W szczególności zmieniono sposób łączenia nadkoli z przednią częścią dachu kadłuba. Za pomocą specjalnej listwy „buforowej” wykonanej z miękkiej stali, która była wcześniej przyspawana do okładziny błotnika, udało się zmniejszyć poziom naprężeń końcowych wewnątrz szwu i wokół pancerza. Następnie wymyśliliśmy wspomnianą „infrastrukturę” na przedniej płycie czołgu. Teraz, zgodnie z nowymi warunkami technicznymi, można było spawać śruby oczkowe, osłonę karabinu maszynowego i zawiasy włazu tylko elektrodami 5-6 mm w kilku warstwach: co najmniej czterech! W podobny sposób połączono błotniki z dachem, przednią płytę z bokami, błotniki i dach. Wszystko inne zostało ugotowane w 2-3 przejściach z elektrodami 7-10 mm.
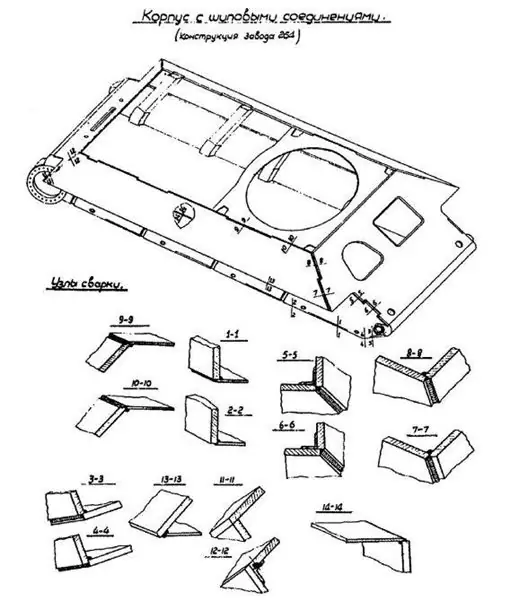
Zmieniono również technologię łączenia części kadłuba czołgu T-34. Początkowo wszystkie połączenia, poza interfejsem VLD i NLD, wykonano w ciągu kwartału, jak wynika z rysunków. Ale wkrótce po wybuchu wojny zmieniono je na kolce, ale to też nie usprawiedliwiało - w miejscach przecięcia szwów pojawiło się zbyt wiele pęknięć. Połączenie kolców do pancerza o wysokiej twardości nie było do końca odpowiednie również ze względu na silne lokalne naprężenia skurczowe po spawaniu. To, co było dobre dla plastikowych niemieckich pancerzy, nie pasowało do krajowych T-34. Dopiero w 1943 r. na „czołgu zwycięstwa” pojawiły się ostateczne opcje przegubu, które zadowoliły specjalistów TsNII-48 - nakładanie się i plecy do siebie.
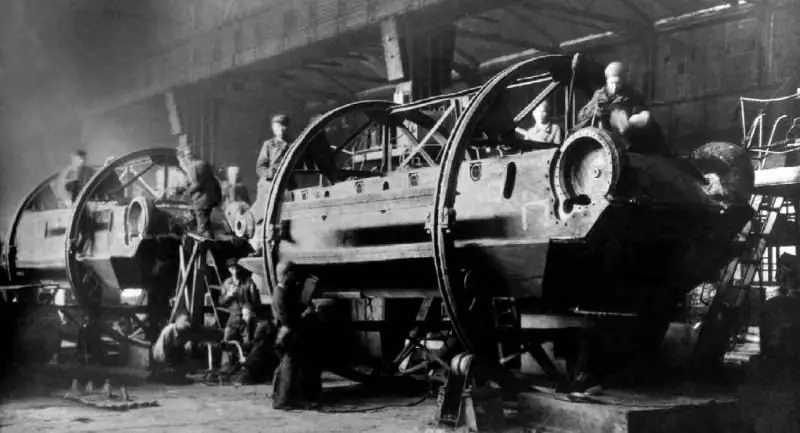
Kadłuby ciężkich radzieckich czołgów przeszły najprostszy proces optymalizacji operacji spawalniczych. Połączenie płyt pancernych w ćwiartce na KV pozostało niezmienione, ale wewnętrzne kolanka wzmacniające zostały zastąpione wewnętrznymi spoinami pachwinowymi. Już w trakcie wojny dla czołgów ciężkich wybrano najbardziej optymalne konfiguracje współpracujących płyt pancernych (przede wszystkim ostrzeliwując). Jeśli kąt połączenia był bliski 90 stopni, lepiej było zastosować metodę „w cierniu” lub w ćwiartce, a we wszystkich innych wariantach - w kręgosłupie lub w zębie. W wyniku tych badań w TsNII-48 narodził się osobliwy kształt górnej części zespołu dziobowego czołgu IS-2, kiedy to pancerz o grubości 100-110 mm zapewniał wszechstronną ochronę przed Pociski 88-105 mm. Połączenie elementów w tę solidną konstrukcję było prostą niespodzianką.