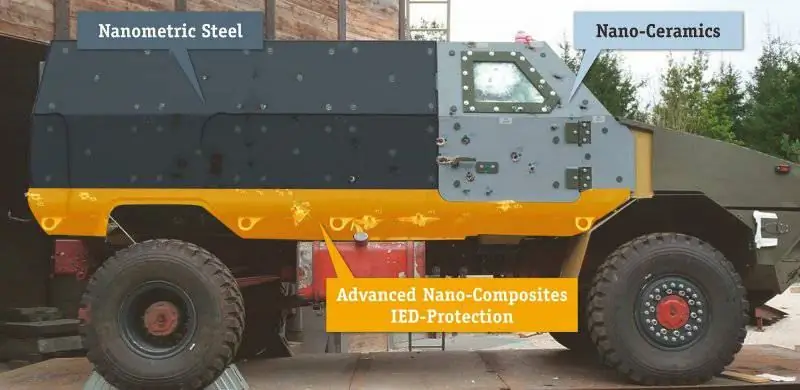
W MPV Iveco zastosowano najnowsze rozwiązania ochronne IBD Deisenroth, głównie oparte na nanotechnologii
Pancerz pasywny: Ostatnia Bariera
Kadłuby pojazdów opancerzonych nadal są wykonane ze stali, do której przykręcane są dodatkowe zestawy opancerzenia. Jednak im więcej podstawowa konstrukcja może zapewnić w zakresie ochrony balistycznej i przeciwwybuchowej, tym wyższy będzie ostateczny poziom ochrony. Ponadto, nawet przy instalacji systemów aktywnej ochrony, które niszczą atakujące pociski nawet przy zbliżaniu się, powstałe odłamki o wysokiej energii mogą spowodować poważne uszkodzenie pojazdu, co ponownie wymaga dobrej ochrony podstawowej
Szwedzka firma SSAB jest jednym z renomowanych specjalistów w dziedzinie materiałów pancernych, a jej rodzina stali pancernych Armox jest dobrze znana na całym świecie. Rodzina obejmuje sześć różnych typów, liczba w oznaczeniu gatunku stali wskazuje średnią twardość Brinella. Podczas gdy twardość bezpośrednio wpływa na ochronę balistyczną, wytrzymałość jest potrzebna do pochłaniania energii podmuchu - dwóch cech, które w rzeczywistości nie mogą istnieć razem. Formowalność zaostrza ten konflikt, ponieważ stale o wysokiej wytrzymałości są na ogół mniej podatne na formowanie i często mają problemy ze spawalnością.
Z biegiem czasu właściwości balistyczne stali SSAB stopniowo się poprawiały: w 1990 r. potrzebna była stal Armox 500T o grubości 9 mm, aby zatrzymać pocisk M193/SS92 lecący z prędkością 937 m/s, ale dziesięć lat później z Armoxem Stop 600T, tylko 6 było potrzebnych do zatrzymania mm. Kolejne dziesięć lat i 4,5 mm Armox Advance robi to samo, chociaż liczba ta nie jest już tego warta, ponieważ twardość przekracza skalę Brinella! Z początkowych 70,7 kg/m2, SSAB zdołało obniżyć wagę do 47,1 kg/m2 w ciągu dziesięciu lat i do 35,3 kg/m2 w następnej dekadzie. Według ekspertów SSAB nie przewiduje się dalszego znaczącego spadku, rzeczywista wartość na 2020 r. to 30 kg/m2. Dział badawczo-rozwojowy firmy pracuje bardziej nad poprawą wytrzymałości i odkształcalności istniejącego materiału niż nad jego twardością, zwłaszcza że obecnie głównym zagrożeniem jest eksplozja. Jego stal Armox 440T 420-480 HB Brinell została nazwana preferowanym pochłaniaczem energii, a jej wytrzymałość ułatwia uzyskanie dowolnego kształtu, na przykład litego dna. Nawet twardsza stal Armox 500T, o twardości 480-540 HB, jest uważana za materiał do ochrony przed wybuchem.
Jak wspomniano powyżej, główną cechą Armox Advanced jest twardość, dlatego stal ta jest uważana przez SSAB za de facto ceramikę. Dlatego firma zdecydowanie odradza formowanie lub spawanie, ponieważ nie należy go podgrzewać powyżej 100 ° C, aby zachować jego twardość. Jak osiągnąć podobny poziom ochrony i wagi w przyszłości przy użyciu bardziej formowalnych materiałów, jest dziś bardzo trudnym zadaniem.
Wśród nowych stali pancernych należy oczywiście zwrócić uwagę na Super Bainite, wprowadzony jesienią 2011 roku. Nowa stal, opracowana przez brytyjskie Laboratorium Nauki i Technologii Obronnych DSTL, jest produkowana w Tata Steel UK. Wykazuje znacznie lepsze parametry niż standardowa stal pancerna. Cechy te wynikają nie tylko ze składu chemicznego, ale również z procesu produkcyjnego, w szczególności obróbki cieplnej z chłodzeniem powietrzem i stopionymi solami. Produkt końcowy ma dwukrotnie lepsze parametry balistyczne niż walcowany pancerz jednorodny.
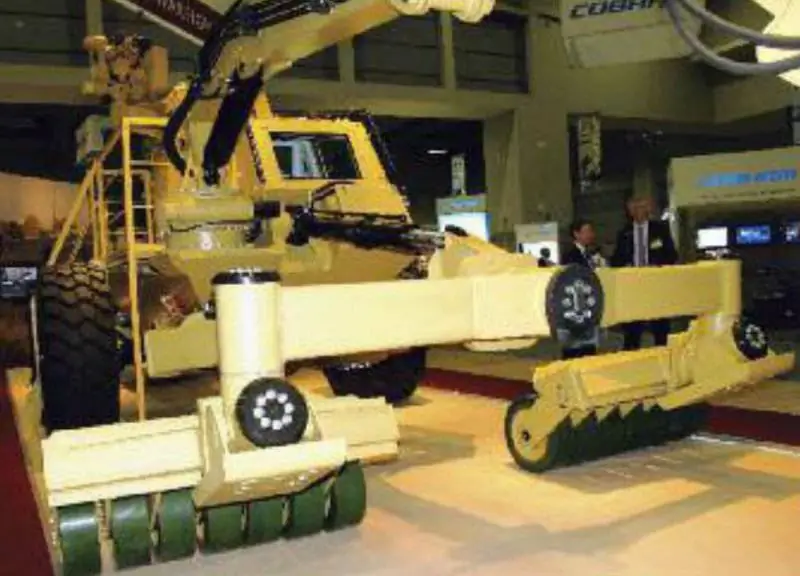
Południowoafrykańska firma Aardvark Perroc intensywnie wykorzystuje w swoich produktach stal SSAB Armox 500. To pokazuje, że nawet ta stal o wysokiej twardości jest w stanie pochłaniać duże ilości energii.
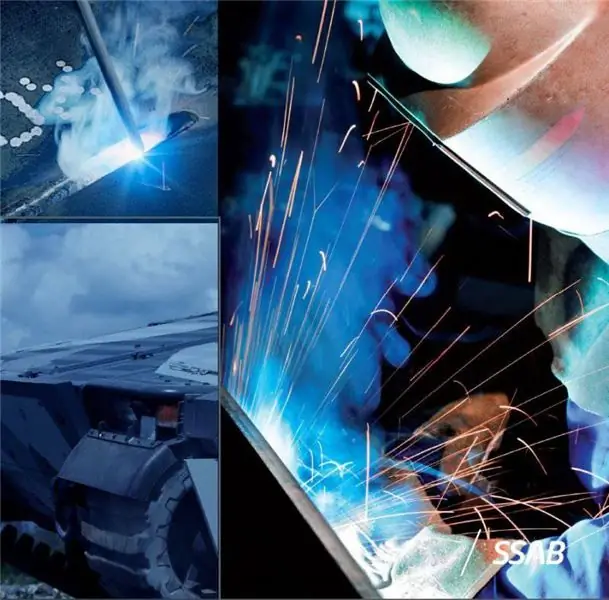
SSAB produkuje skomplikowane kształty ze swojej stali Armox 440T, często określanej mianem „pożeracza energii”. Bardzo dobrze nadaje się do konstrukcji narażonych na IED. SSAB pracuje obecnie nad zwiększeniem możliwości formowania stali pancernej.
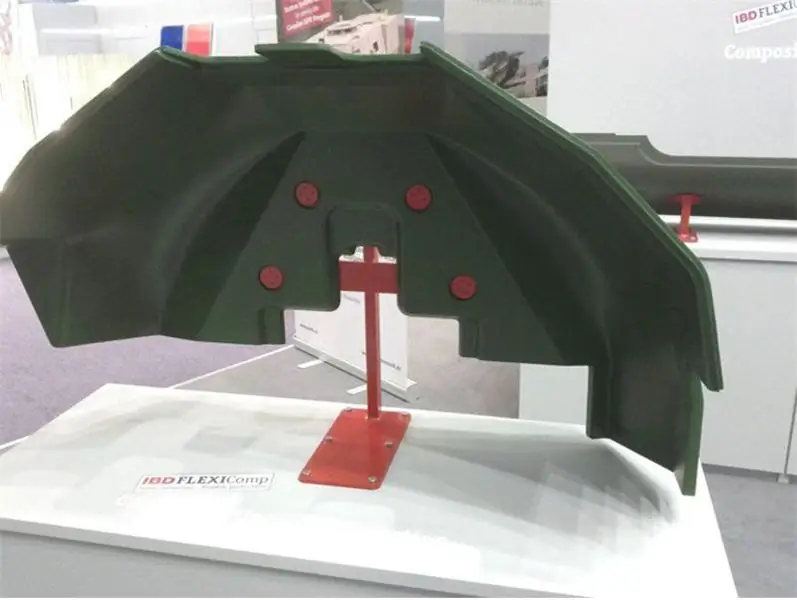
Zastosowanie podszewki IBD FlexiComp pozwala na produkcję wolumetrycznych elementów zabezpieczających, redukując liczbę słabych punktów w całym systemie zabezpieczeń
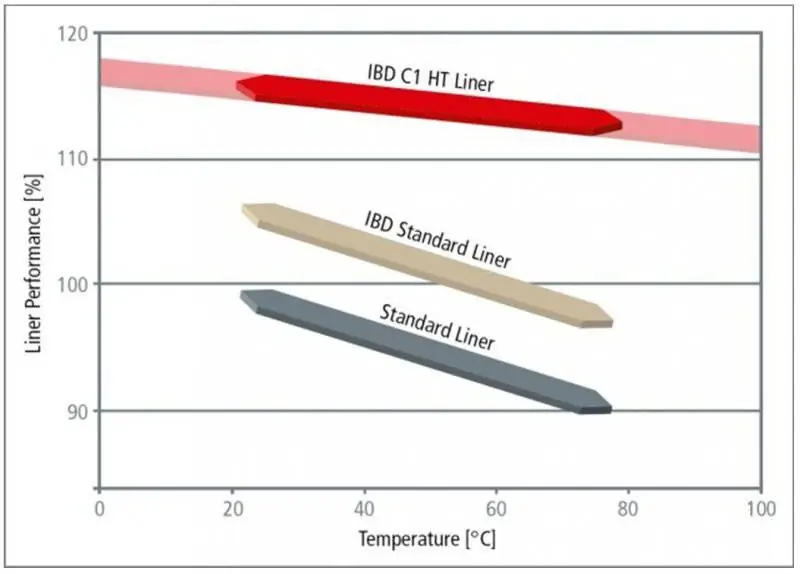
Wykres charakterystyki wkładek IBD w funkcji temperatury. Wpływ wysokich temperatur jest głównym problemem podczas wdrażania maszyn w gorącym klimacie
W grudniu 2012 roku Lockheed Martin UK i University of Surrey ogłosiły nową, prostszą metodę poprawy ochrony i przeżywalności pojazdów opancerzonych. Naukowcy opracowali metodę obróbki materiałów ceramicznych w celu poprawy siły adhezji ceramiki z tlenku glinu i ceramiki z węglika krzemu do podłoża kompozytowego, co znacznie zwiększa wytrzymałość pancerza. Piętą achillesową tej technologii od zawsze było mocowanie płytek ceramicznych do ich podłoża. Wyniki pokazały, że nowa technika poprawia siły trakcyjne. Testy wykazały, że gdy przeciwpancerny pocisk zapalający kalibru 14,5 mm zostanie wystrzelony w płytę pancerza, pozostaje on nienaruszony.
Rozwój technologiczny pozostaje podstawową działalnością IBD Deisenroth Engineering, podczas gdy rozwiązania pasywne są obecnie zlecane na zewnątrz firmie Rheinmetall Chempro, która w 51% należy do Rheinmetall Defence, aw 49% do rodziny Deisenroth.
Kiedy dr Ulf Deisenroth opracował technologie opancerzenia czwartej generacji dla różnych rodzajów materiałów, zadaniem było zmniejszenie masy przy zachowaniu poziomu ochrony lub odwrotnie, zwiększenie poziomu ochrony dla danej masy, podczas gdy nowe technologie obiecują oszczędności ponad 40%. Opierają się na najnowszych przełomach w dziedzinie pasywnej ochrony związanej z nanomateriałami, do których należą ceramika nanokrystaliczna, stal nanometryczna i włókna o wysokiej wytrzymałości. We współpracy z producentami stali firma IBD opracowała wysokowytrzymałe stale azotowe, które są prawie takie same jak standardowe materiały ceramiczne. Te nowe rodzaje stali mogą być stosowane do elementów konstrukcyjnych, a jednocześnie mogą osiągnąć jeszcze większą oszczędność masy, jeśli zostaną zastosowane na wczesnych etapach projektowania. Jeśli chodzi o włókna o wysokiej wytrzymałości, np. IBD C1 HT Liner, mają one właściwości prawie 20% wyższe nie tylko w porównaniu do standardowej podszewki, ale nawet o 10% wyższe niż inne podszewki IBD; pogarszanie się ich parametrów wraz ze wzrostem temperatury jest również wolniejsze, co jest szczególnie ważne w obliczu ekstremalnych temperatur panujących na współczesnych polach bitew. Oprócz stali nanoskalowych i nanoceramiki stosowanych na nowo opracowanych maszynach, firma IBD opracowała również nowe rozwiązania z materiałów kompozytowych, które pozwalają na produkcję elementów o złożonej zakrzywionej geometrii, co pozwala na osiągnięcie 100% pokrycia chronionego obszaru prawie bez szczelin balistycznych. Rozwiązanie to stosuje się w szczególności przy produkcji elementów dolnych, gdzie najmniejsza szczelina może zagrozić całej ochronie.
Firma IBD odniosła również sukces w opracowaniu laminatów nanokompozytowych, których wytrzymałość jest tak znacznie zwiększona, że mogą zastąpić elementy konstrukcyjne maszyny, jednocześnie służąc jako ochrona balistyczna na wysokim poziomie. Ze względu na niską gęstość powierzchniową, całkowita waga tego poziomu ochrony jest w ten sposób znacznie zmniejszona. Kompozyty te są oparte na wspomnianych materiałach nanotechnologicznych firmy IBD. Opracowano specyficzne procesy spajania, które są wykorzystywane do wytwarzania nanokompozytowych laminatów materiałów konstrukcyjnych, znanych jako IBD FlexiComp, o zwiększonej wytrzymałości strukturalnej i właściwościach balistycznych. Przy gęstości mniejszej o 10% w porównaniu ze standardowymi laminatami, właściwości sprężyste tych materiałów są dwukrotnie wyższe. Ta wysoka wytrzymałość pozwala na zintegrowanie ich z konstrukcją maszyny, podczas gdy właściwości balistyczne pozwalają na radzenie sobie z zagrożeniami wysokiego poziomu, podczas gdy materiały FlexiComp mają dobry potencjał w zakresie redukcji masy. Ich zastosowanie można zrealizować na dwa różne podejścia. Bezpośrednim podejściem jest wykorzystanie ich do ochrony przed minami i IED jako dodatkowego pancerza w nadkolach, błotnikach, jako płyty minowe i rozmieszczone podłogi wewnętrzne. Podczas formowania części wolumetrycznych mogą zastąpić inne rozwiązania, takie jak zespoły składane przez spawanie lub skręcanie. Drugie podejście to integracja części kompozytowych, takich jak włazy, włazy silnika, tylne drzwi i rampy. Stanowią one dużą część całkowitej powierzchni pojazdu, przez co bezwzględna redukcja masy będzie bardzo znacząca. Dla STANAG 4569 poziom 4 ta redukcja wagi wynosi 1500 kg dla maszyny 8x8 (patrz tabela). Pod względem kosztów wytwarzania procesy opracowane przez IBD pozwalają na produkcję części kompozytowych bez użycia autoklawów, zapewniając znaczne oszczędności, zwłaszcza w przypadku dużych elementów, ich koszt jest porównywalny z kosztem elementów wytwarzanych przy użyciu standardowych technologii.
Komponenty te są obecnie produkowane przez firmę Rheinmetall Chempro, której zadaniem jest opanowanie technologii IBD Deisenroth Engineering, rozwinięcie ich w proces produkcyjny w celu uzyskania konkurencyjnych cen, dalsze rozwijanie specjalistycznych rozwiązań i kontynuowanie ich aż do procesu kwalifikacji maszyn. Dostawy komponentów wykonanych przy użyciu najnowszych zaawansowanych technologii rozpoczęły się na początku 2013 roku, przede wszystkim maszyn AMPV firmy KMW-Rheinmetall oraz Medium Protected Vehicle firmy Iveco DV-KMW. Kilkunastu producentów oryginalnego sprzętu na całym świecie wkrótce otrzyma komponenty, które pozwolą im naprawdę zmniejszyć wagę maszyn, zwiększając w ten sposób ładowność i obniżając koszty cyklu życia, powiedział Dział Ochrony Rheinmetall.
Portfolio pasywne Rheinmetall Chempro obejmuje różne wersje rodziny Amap (Advanced Modular Armor Protection). Ta rodzina wykorzystuje najnowszą technologię opracowaną przez IBD. Produkty Amap są zazwyczaj łączone w celu zapewnienia pożądanej ochrony przed szeroką gamą zagrożeń. Wśród różnych nieprzezroczystych produktów widzimy rozwiązanie balistyczne Amap-B, które zapewnia ochronę przed bronią strzelecką i amunicją średniego kalibru, ochronę przeciwminową Amap-M, Amap-IED przeznaczony do zwalczania IED, wkładki Amap-L chroniące przedział bojowy poprzez pochłanianie odłamków wtórnych, Amap-SC przed pociskami HEAT i wreszcie rozwiązanie Amap-X, które chroni przed zagrożeniami typowymi dla warunków miejskich.
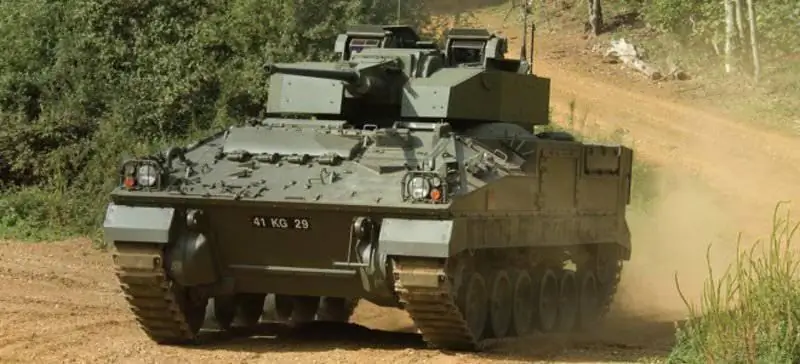
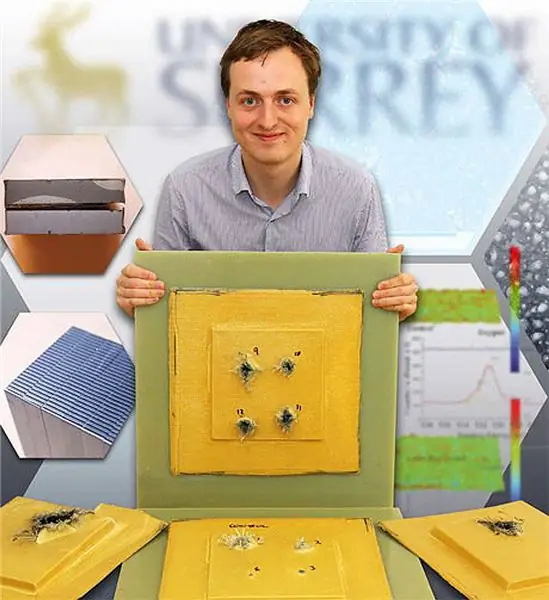
Nowa technologia spajania opracowana przez Lockheed Martin UK i University of Surrey może znacznie poprawić ochronę pojazdów opancerzonych, takich jak Warrior BMP (powyżej)
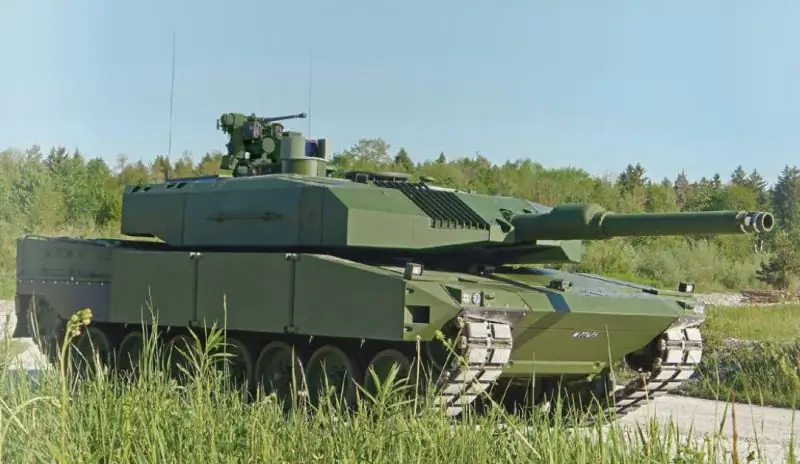
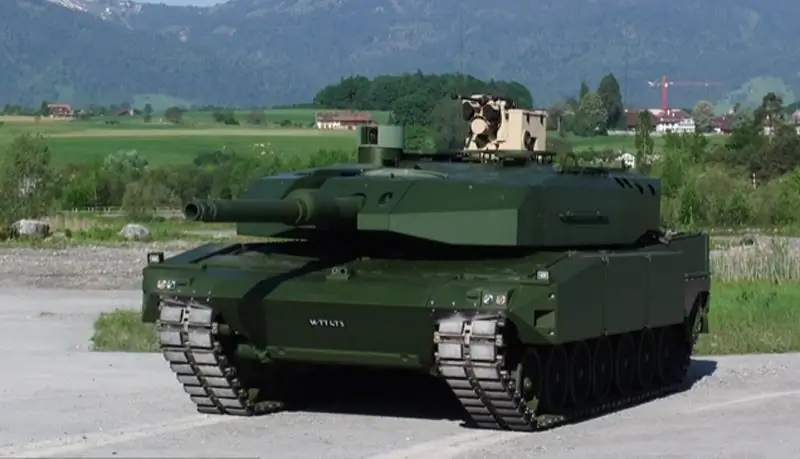
Dodatkowe moduły SidePro-ATR dla MBT Leopard
Należy zauważyć, że w ramach Grupy Rheinmetall ochroną bierną zajmuje się inna firma, Rheinmetall Ballistic Protection GmbH, która 1 stycznia 2013 roku otrzymała nową nazwę. Wcześniej nosiła nazwę Rheinmetall Verseidag Ballistic Protection GmbH. W pełni należąca do Rheinmetall firma specjalizuje się w projektowaniu i produkcji rozwiązań opancerzenia dla lekkich pojazdów wojskowych z materiałów takich jak ceramika, zaawansowane metale i specjalistyczne tkaniny.
Chociaż Ruag Defense nadal ma w swoim portfolio rozwiązania z zakresu ochrony dynamicznej (pancerz aktywno-reaktywny), nie patrzy już w oczy konsumentów jako ultranowoczesna firma zdolna do zwiększenia przeżywalności pojazdów średnich i ciężkich. W związku z tym szwajcarska firma zwróciła uwagę na doskonalenie całkowicie pasywnych rozwiązań, które radzą sobie z ładunkami kinetycznymi i kumulacyjnymi. System SidePro-ATR wykracza daleko poza agresywność RPG-7, ponieważ radzi sobie z ładunkami kumulowanymi używanymi w scenariuszach symetrycznych, podczas gdy wersja podstawowa gwarantuje ochronę balistyczną na poziomie 5. SidePro-ATR po raz pierwszy zaprezentowano publiczności w 2012 roku, system ten jest skalowalny, dzięki czemu może być stosowany zarówno na transporterach opancerzonych, jak i na czołgach. W wersji podstawowej ma grubość 400 mm, a jego masa jest porównywalna z masą roztworu reaktywnego (czyli około 300 kg/m2). System ten został zakwalifikowany do czołgu Leopard 2A4. Poziom ochrony balistycznej można znacznie zwiększyć do tego stopnia, że system wytrzyma uderzenie wydłużonego rdzenia o średnicy 120 mm, chociaż nie podano żadnych danych w tym zakresie.
Skalowalność SidePro-ATR pozwala na wykorzystanie go w symetrycznych i asymetrycznych scenariuszach walki. Inne rozwiązanie do zwalczania amunicji kinetycznej i IED pod oznaczeniem SidePro-KE/IED przetestowano na opancerzonym wozie rozpoznawczym Fennek, który służy w Niemczech i Holandii. Oparte głównie na ceramice rozwiązanie to było przeznaczone do zwalczania IED pierwszej generacji. Nowe bomby przydrożne, używane w różnych teatrach, generują tysiące odłamków o dużej prędkości, dlatego potrzebne są bardzo dobre właściwości wielouderzeniowe. Od tego czasu Ruag dopracował system KE/IED, odchodząc od ceramiki i stosując nierozprężalne wielowarstwowe worki. Nowe rozwiązanie SidePro-KE / IED, dostępne od 2012 roku, oferuje ochronę poziomu 4 / 5 przed bronią kinetyczną i ma wyjątkowo wysoką wydajność przy wielu uderzeniach. Zakładając, że podwozie jest wykonane ze stali balistycznej 7 mm, 30 mm panel może zapewnić pełną wymaganą ochronę, a system KE / IED pozwala na najmniejszy przyrost masy, w zależności tylko od typu pojazdu. Na to rozwiązanie czeka kilku producentów.
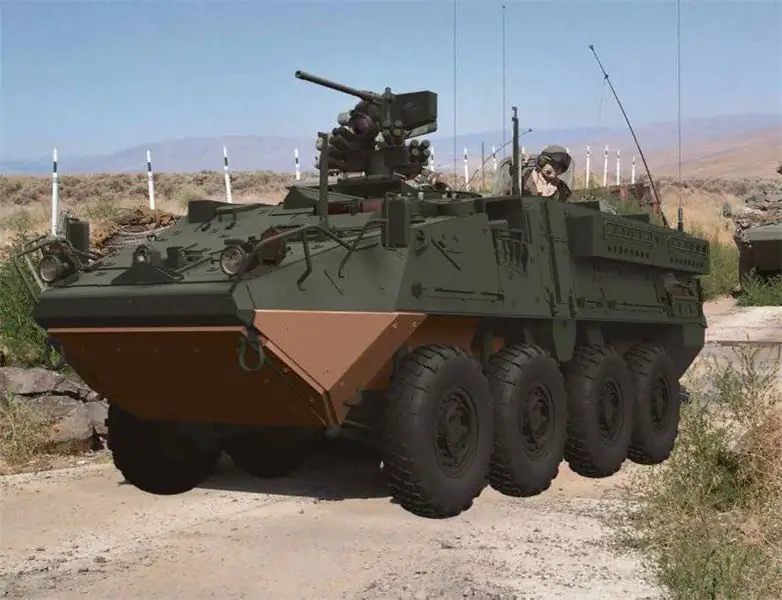
Ruag sfinalizował SidePro KE / IED. Fotomontaż przedstawia elementy systemu zaprojektowanego do przeciwdziałania nowym urządzeniom generującym wiele fragmentów.
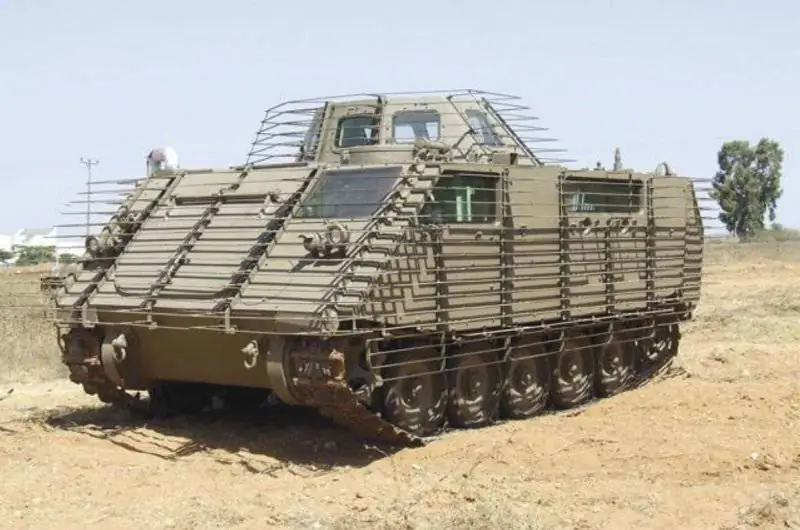
BTR M113, wyposażony w pasywny system anty-RPG Iron Wall z Israel Military Industries, łączący pasywny i kratowy pancerz
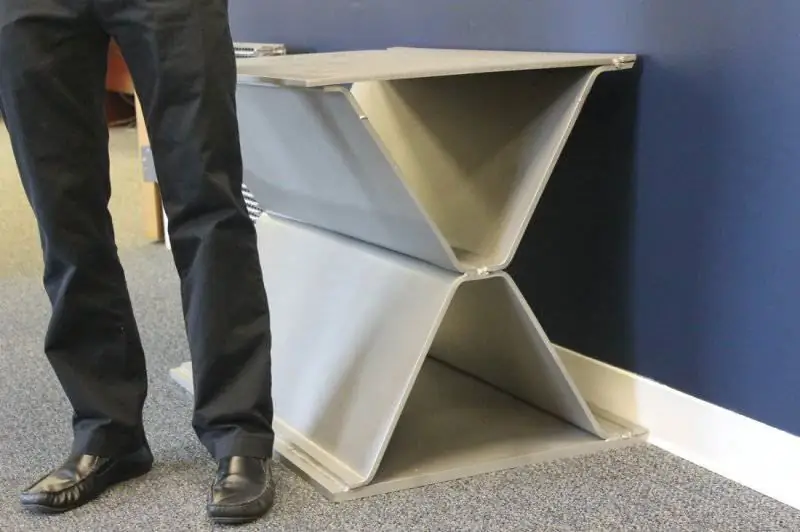
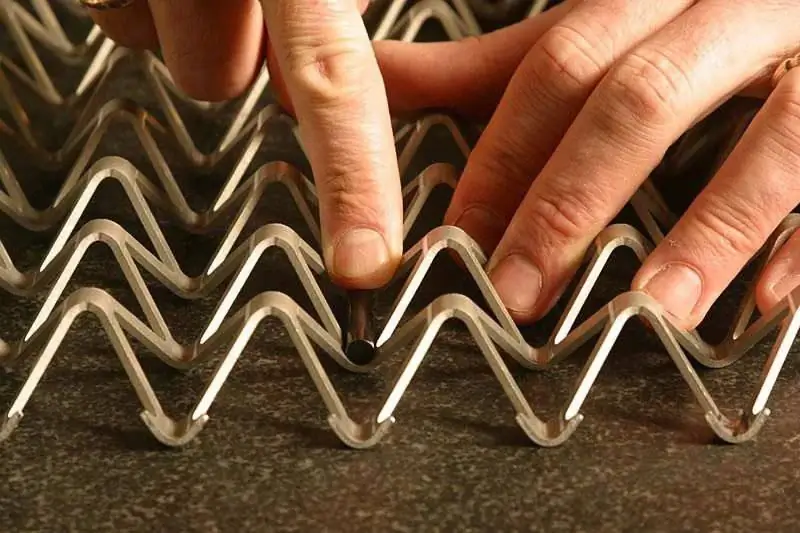
Ceradyne i Cellular Materials International opracowały dolną osłonę opartą na strukturze plastra miodu z aluminium CMI MicroTruss, która pochłania do jednej trzeciej energii generowanej przez eksplozję. Poniżej znajduje się zbliżenie materiału MicroTruss.
Przykład redukcji wagi dla maszyny 8 x 8 z komponentami wykonanymi z IBD FLEXICOMP
Waga w kg
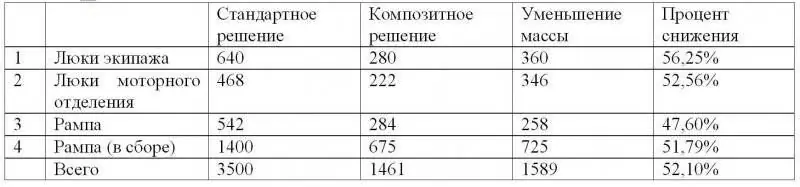
Plasan Sasa pozostaje jednym z kluczowych graczy w branży rezerwacji pasywnych. W tym zakresie nie są podawane żadne szczegóły technologiczne, natomiast firma jest aktywna zarówno w rezerwacjach dodatkowych, jak iw budynkach prefabrykowanych. Drugie podejście zostało podjęte przy opracowaniu Mrap od Navistar MaxxPro i M-ATV od Oshkosh. „Pozwala nam to zwiększyć produkcję przy użyciu siły roboczej bez umiejętności spawalniczych, ponieważ nasze podejście w stylu Lego opiera się na blokach zawierających wszystkie komponenty, które można zmontować w minimalnym czasie” - mówi źródło firmy. Część z ponad dwustu inżynierów firmy pracuje nad nowymi rozwiązaniami, które mogą wynikać z pojawienia się nowych materiałów lub innowacyjnych rozwiązań geometrycznych. Podejście systemowe pozostaje w centrum cyklu ochrony.
Firma IMI opracowała ostatnio szereg pasywnych i reaktywnych rozwiązań do przeciwdziałania najnowszym typom urządzeń IED, w tym różnego rodzaju „rdzeniem wstrząsowym” EFP lub SFF (Self Formed Fragmentation) oraz najnowszym modelom RPG. Firma zaproponowała pasywne rozwiązanie Iron Wall oparte na połączeniu metalu i kompozytów uzupełnionych pancerzem kratowym. W zależności od wymaganego poziomu ochrony grubość może wynosić od 110 do 150 mm, a ciężar od 200 do 230 kg/m2. Żelazny Mur przechodzi obecnie próby wojskowe z armią izraelską.
IMI oferuje również swoją zbroję kratownicową jako samodzielny system. L-VAS (Light Vehicle Armor System - system opancerzenia lekkich pojazdów) przeznaczony jest do ochrony pojazdów takich jak transportery opancerzone. W celu zmniejszenia wagi system oparty jest na materiałach kompozytowych i elementach reaktywnych, które zawierają minimum materiałów energetycznych. Zmniejsza to straty pośrednie, a rodzaj materiału zapobiega ryzyku wtórnej detonacji sąsiednich elementów. Według IMI system L-VAS chroni również przed pociskami przeciwpancernymi kal. 14,5 mm i odłamkami artyleryjskimi. System został w pełni zakwalifikowany w Izraelu do swojego transportera opancerzonego M113 i ma ciężar właściwy około 200 kg/m2.
Oferowany jest również cięższy system falochronów. Ten pancerz reaktywny, składający się z elementów metalowych i kompozytowych, jest przeznaczony do zwalczania trzech głównych zagrożeń: RPG, SFF i EFP. IMI przeprowadziło szeroko zakrojone testy i obecnie prowadzi kwalifikacje do rozpoczęcia produkcji rozwiązania o grubości 350 - 400 mm i gramaturze 430 - 450 kg/m2 pod koniec 2013 roku.
Ceradyne jest kolejnym ważnym graczem w rezerwacjach pasywnych. Według Marka Kinga, prezesa Ceradyne, stal pozostaje głównym materiałem w branży rezerwacji, a jej celem jest poprawa wydajności i obniżenie kosztów. „W Stanach Zjednoczonych czynnikiem napędzającym jest głównie koszt nabycia pojazdu, a nie koszt jego żywotności, a to działa przeciwko modernizacji” - powiedział King na konferencji AUSA w 2012 r. podczas gdy w Stanach Zjednoczonych nacisk położono na ilość, która wyprzedziła amerykańskich twórców systemów ochrony. King podkreślił jednak, że obecnie Ameryka rozwija się, koncentrując się głównie na przeciwwybuchowej ochronie podwozia, ponieważ ochrona balistyczna jest postrzegana jako rozwiązany problem. Zainteresowanie armii amerykańskiej, ponownie okazywane rozwiązaniem problemu ochrony dna takich pojazdów, jak np. Humvee (20 mln dolarów tylko na rozwój), jest pozytywnie oceniane przez Kinga. Ceradyne należy do tych, którzy z pewnością powalczą o kontrakt na ich modernizację. Wymóg zapewnia maksymalną ochronę przy znacznych oszczędnościach masy w celu zmniejszenia wpływu na wydajność maszyny.
Ceradyne opracowała rozwiązanie MicroTruss firmy Cellular Materials International Inc (CMI). Ten porowaty materiał ze stopu aluminium ma gęstość 58 kg/m2 w porównaniu z gęstością 112 kg/m2 równoważnego roztworu metalu monolitycznego. To rozwiązanie różni się kątem „V” korpusu równym tylko 5°, co wystarcza do odbicia fali uderzeniowej i ma masę 300 kg. MicroTruss gwarantuje pochłonięcie do 30% energii wybuchu, co nie tylko ogranicza uderzenie w kapsułę załogi, ale również ogranicza ruch pionowy pojazdu. Ceradyne jest również mocno zaangażowana w program rezerwacji Flyer Gen.2, którego celem jest projekt Sił Operacji Specjalnych dla GMV 1.1. Aby utrzymać możliwość transportu wewnątrz śmigłowców V-22, CH-47D i CH-53E, gdy masa i szerokość muszą być utrzymane w określonych granicach, firma opracowała zestaw, który zapewnia poziom B6 (.357 Magnum) ochrony balistycznej drzwi i dach.
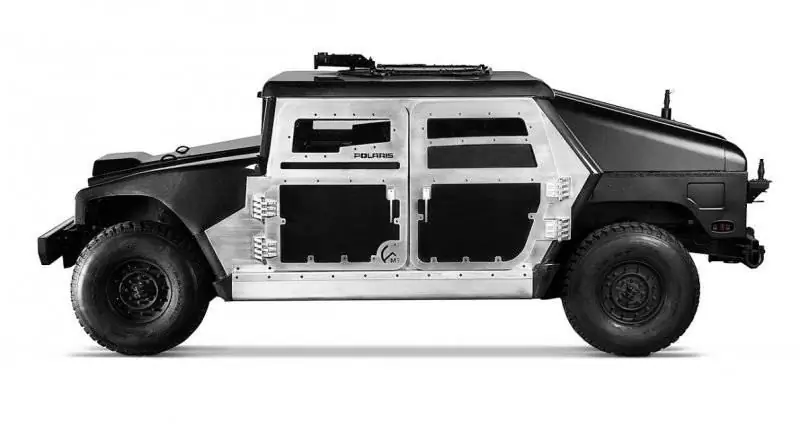
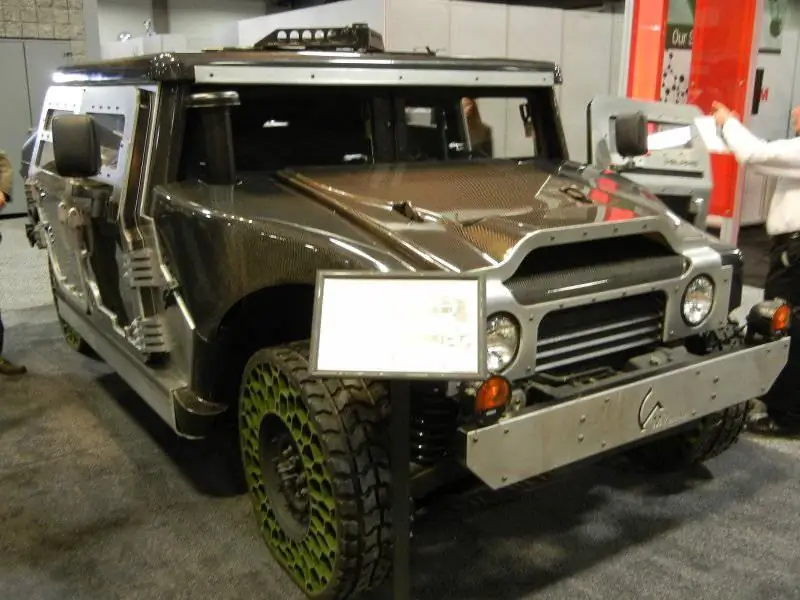
Polaris Defense i M9 Defense Armor Technology opracowały hybrydowy stalowy, kompozytowy pancerz strukturalny, który może znacznie zmniejszyć masę własną Humvee przy jednoczesnym zachowaniu poziomu ochrony. Prototyp przedstawiony po prawej stronie ma masę własną wynoszącą zaledwie 3400 kg, czyli prawie o 50% mniej niż Humvee z ochroną na poziomie 3.(Zwróć uwagę na koła samochodu na dole)
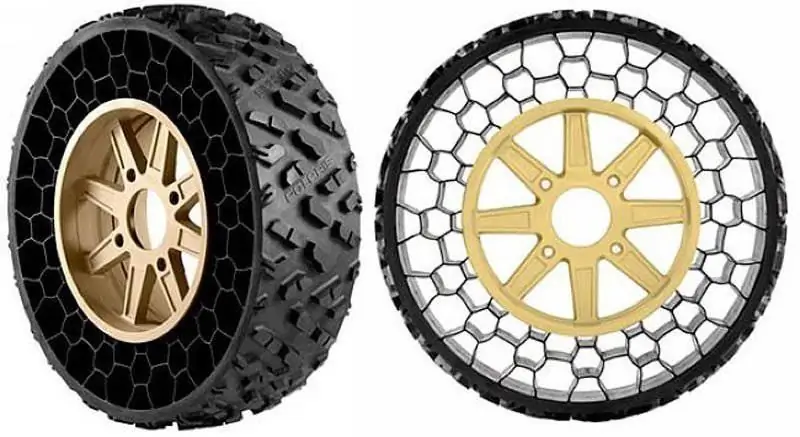
Ochrona polega również na tym, aby nie zostać na polu bitwy w przypadku przebicia koła. Niepneumatyczne koła Polaris Defence gwarantują znacznie lepszą trwałość w porównaniu do standardowych opon i wytrzymują kulę 12,7mm. Obecnie dostępne są nie tylko do samochodów, w tym do klasy Hummer, ale teraz te felgi są również opracowywane do cięższych aut klasy Mrps.
Ceradyne uczestniczy również w programie Marines Personnel Carrier we współpracy z Lockheed Martin i Patria na pojeździe piechoty morskiej opartym na fińskim Patria AMV. Warto dodać, że 28 listopada 2012 r. ogłoszono, że Ceradyne została przejęta przez Grupę 3M, co pozwoli jej więcej inwestować w badania i rozwój oraz innowacyjne rozwiązania.
Integracja projektu i ochrony to bardzo poszukiwane rozwiązanie dla lekkich pojazdów. Na AUSA 2012 Polaris Defense pokazał prototyp pojazdu Humvee z nową koncepcją, którą opracował we współpracy z M9 Defense. Wyzwaniem jest zmniejszenie masy własnej przy jednoczesnym utrzymaniu i zwiększeniu poziomu ochrony. Aby to zrobić, zespół Polaris-M9 usunął cały górny pancerz, aby przyjrzeć się koncepcji pancerza strukturalnego. Potem wszystko zostało usunięte z samochodu, pozostało tylko gołe podwozie, a następnie położono na nim lekką konstrukcję hybrydową (stalowo-kompozytowy materiał). Ten pancerz strukturalny może zapewnić ochronę na poziomie 3 przy masie 70 kg/m2, a przy masie 83 kg/m2 jest w stanie wytrzymać pocisk 12,7 x 99 mm, chociaż grupa Polaris-M9 jest przekonana, że może osiągnąć poziom 3+ (12, 7 mm pocisk przeciwpancerny). Rozwiązanie Polaris-M9 chroni również silnik. Podczas gdy standardowy transporter opancerzony Hummer waży około 6350 kg, proponowane rozwiązanie pozwala zmniejszyć jego wagę do 3400 kg. Hybrydowy pancerz strukturalny wykorzystuje nieegzotyczny materiał, co pozwala zespołowi Polaris-M9 mówić o kosztach nowego rozwiązania, porównywalnych z kosztami obecnych rozwiązań. Ponadto materiał ten jest formowany w skomplikowane kształty, co skutkuje m.in. bezszwowymi spodniami w kształcie litery V. Osiągnięcie pożądanego kształtu uzyskuje się poprzez formowanie hydrauliczne - szybki proces, który pomaga obniżyć koszty. Według zespołu Polaris-M9 technologia ta może zmniejszyć wagę o 40 procent.
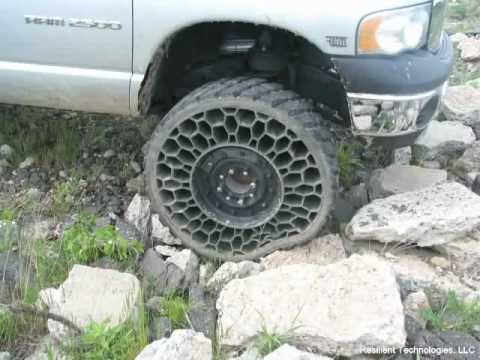
Pokaz niepneumatycznych kół firmy Polaris Defence
Równanie obrony zawiera inny termin, który bezpośrednio odnosi się do mobilności - koło. Po przejęciu Resilient Technologies, Polaris Defense oferuje teraz koła niepneumatyczne (NPT). Zużycie kół jest jednym z najważniejszych problemów logistycznych w silniku turbinowym, a rozwiązanie NPT w wielu przypadkach pomoże go rozwiązać. Według dowództwa sił operacji specjalnych w Afganistanie konwencjonalne opony pokonują około 1300 km, podczas gdy koło NPT przebite kulą 12,7 mm może przebyć ponad 8 000 km i tym samym wypierać koła zapasowe z łańcucha dostaw, jednocześnie poprawiając jakość jazdy. Prototypy NPT zostały już wykonane dla pojazdów Hummer. Obecnym celem jest zestaw kół NPT do maszyny o masie 7,7 ton, co stanowi prawie całkowitą wagę wariantu JLTV General Purpose. Według przedstawicieli firmy, modelowanie pokazało, że masa może osiągnąć 18 ton, czyli koła są w stanie wytrzymać samochód klasy Mrap. Wraz ze wzrostem ładowności technologia pozostaje taka sama, a programy symulacyjne firmy pozwalają na bardzo dokładne prognozy. To, co się zmieni, to materiał, który musi się dostosować do masy, która z kolei nie pojawi się w przyszłości.