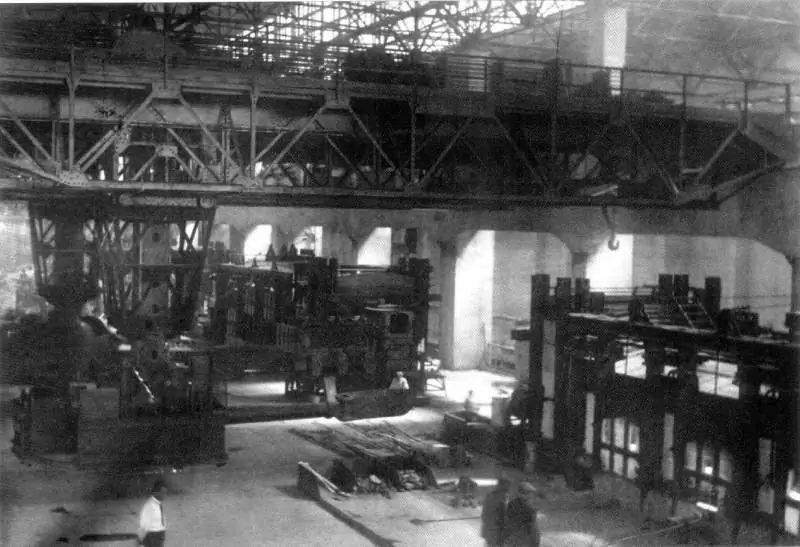
Zasób strategiczny
Trudno przecenić produkcję wysokiej jakości stali dla kompleksu wojskowo-przemysłowego w warunkach wojennych. To jeden z najważniejszych czynników sukcesu armii na polu bitwy.
Jak wiecie, metalurdzy Kruppa byli jednymi z pierwszych, którzy nauczyli się wytwarzać wysokiej jakości stal do broni.
Niemcy przyjęli proces produkcyjny Thomasa pod koniec XIX wieku. Ten sposób wytopu stali umożliwił usunięcie z rudy zanieczyszczeń fosforowych, co automatycznie podniosło jakość produktu. Wysokiej jakości stal pancerna i zbrojeniowa podczas I wojny światowej często zapewniała Niemcom przewagę na polu bitwy.
Aby zorganizować taką produkcję, potrzebne były nowe materiały ogniotrwałe, które wyściełały wewnętrzne powierzchnie pieców. Niemcy stosowali na swój czas najnowsze magnezytowe materiały ogniotrwałe, wytrzymujące temperatury powyżej 2000 stopni. Takie substancje o podwyższonej ogniotrwałości bazują na tlenkach magnezu z niewielkimi domieszkami tlenków glinu.
Na początku XX wieku kraje posiadające technologie masowej produkcji magnezytowych materiałów ogniotrwałych mogły sobie pozwolić na produkcję wysokiej jakości zbroi i luf armat. Można to porównać do przewagi strategicznej.
Niższe pod względem odporności ogniowej były tzw. materiały wysoce ogniotrwałe, które wytrzymują temperatury od 1750 do 1950 stopni. Są to materiały ogniotrwałe dolomitowe i wysokoglinowe. Materiały ogniotrwałe szamotowe, półkwasowe, kwarcowe i dynasowe mogą wytrzymać temperatury od 1610 do 1750 stopni.
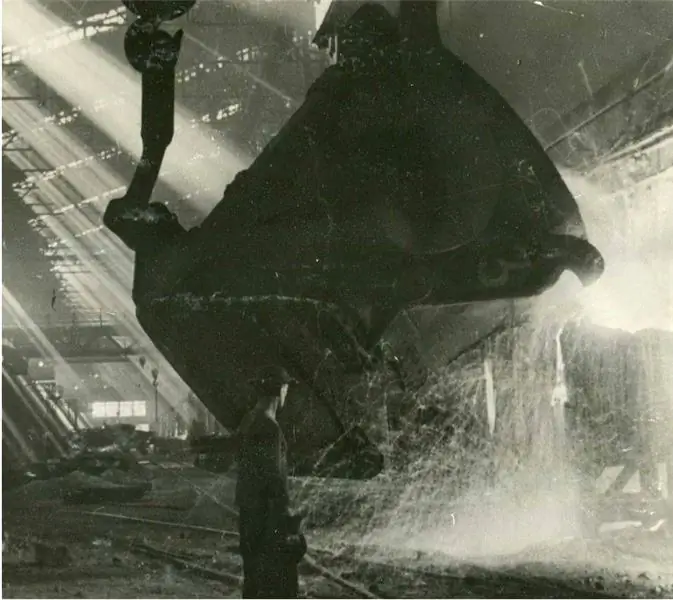
Nawiasem mówiąc, technologie i miejsca do produkcji magnezytowych materiałów ogniotrwałych pojawiły się po raz pierwszy w Rosji w 1900 roku.
Cegła ogniotrwała magnezytowa Satka w 1905 roku została nagrodzona złotym medalem na Światowej Wystawie Przemysłowej w Liege. Został wyprodukowany w pobliżu Czelabińska w mieście Satka, gdzie znajdowało się unikalne złoże magnezytu.
Minerał peryklazowy, z którego w fabryce wykonano materiały ogniotrwałe, był wysokiej jakości i nie wymagał dodatkowego wzbogacania. W rezultacie magnezytowy materiał ogniotrwały firmy Satka przewyższał swoje odpowiedniki z Grecji i Austrii.
Wypełnianie luki
Pomimo dość wysokiej jakości cegły magnezytowej z Satka, do lat 30. głównymi materiałami ogniotrwałymi sowieckich metalurgów były materiały dinasowe z gliny. Oczywiście nie udało się uzyskać wysokiej temperatury do wytapiania stali zbrojeniowej - wymurowanie wnętrz pieców martenowskich kruszyło się i wymagało nadzwyczajnych napraw.
Zabrakło cegieł Satka, a w okresie porewolucyjnym utracono główne technologie produkcji.
W tym samym czasie Europejczycy poszli naprzód - na przykład austriacki magnezyt Radex wyróżniał się doskonałą odpornością na ogień.
Związek Radziecki zakupił ten materiał. Ale nie można było uzyskać analogu bez tajemnicy produkcji. Problem ten podjął absolwent Moskiewskiego Państwowego Uniwersytetu Technicznego. N. E. Bauman Aleksiej Pietrowicz Panarin. W zakładzie Magnet (dawniej Kombinat Satka) w 1933 kierował Centralnym Laboratorium Zakładowym. A pięć lat później rozpoczął masową produkcję peryklazowo-chromitowych lub chromomagnezytowych materiałów ogniotrwałych do pieców martenowskich.
W Zakładzie Metalurgicznym Zlatoust i Moskiewskim Młocie i Sierpu przestarzałe diny zastąpiono materiałem ogniotrwałym Panarina.
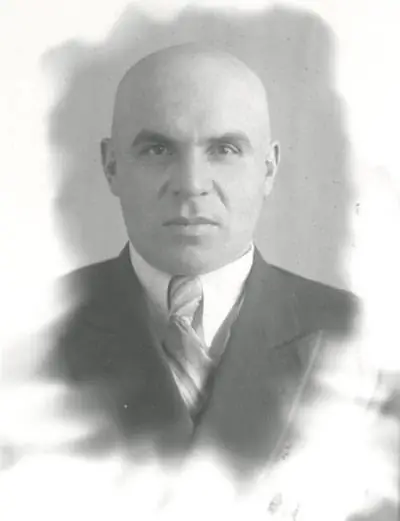
Technologia, która przez kilka lat była rozwijana w laboratorium "Magnezita", polegała na specjalnym składzie i wielkości cząstek.
Wcześniej zakład produkował konwencjonalne cegły chromowo-magnezytowe, składające się z magnezytu i rudy chromowo-żelazowej, w proporcji 50/50. Sekret ujawniony przez grupę Panarina był następujący:
„Jeżeli do zwykłego wsadu magnezytowego dodaje się rudę chromitową o grubych ziarnach granulometrycznych o minimalnej zawartości frakcji mniejszej niż 0,5 mm, to nawet przy 10% dodatku takiej rudy, stabilność termiczna cegły gwałtownie wzrasta.
Wraz ze wzrostem dodatku rudy chromitowej o gruboziarnistej granulometrii wzrasta stabilność cegły i osiąga maksimum przy określonym stosunku składników.”
Chromit do nowego materiału ogniotrwałego pobrano w kopalni Saranowskoje, a peryklaz kontynuowano w Satka.
Dla porównania, zwykła „przedrewolucyjna” cegła magnezytowa wytrzymywała temperatury 5-6 razy mniej niż nowość Panarina.
W hucie miedzi w Kirowogradzie materiał ogniotrwały chromowo-magnezytowy w dachu pieca rewerberacyjnego wytrzymywał temperatury do 1550 stopni przez 151 dni. Wcześniej materiały ogniotrwałe w takich piecach musiały być wymieniane co 20-30 dni.
Do 1941 r. opanowano produkcję materiałów ogniotrwałych na dużą skalę, co umożliwiło stosowanie materiałów w dużych piecach hutniczych w temperaturach do 1800 stopni. Ważny wkład w to wniósł dyrektor techniczny „Magnezita” Alexander Frenkel, który opracował nową metodę mocowania materiału ogniotrwałego do dachów pieców.
Materiały ogniotrwałe dla zwycięstwa
Pod koniec 1941 roku hutnicy Magnitki dokonali tego, co wcześniej nie do pomyślenia - po raz pierwszy w historii opanowali wytop stali pancernej na czołgi T-34 w głównych ciężkich piecach martenowskich.
Głównym dostawcą materiałów ogniotrwałych do tak ważnego procesu była Satka „Magnezit”. Nie trzeba mówić o trudnościach wojny, kiedy jedna trzecia robotników fabrycznych została wezwana na front, a państwo zażądało przepełnienia planu. Mimo to zakład wykonywał swoją pracę, a Panarin w 1943 r.
„Za opanowanie produkcji wyrobów wysokoogniotrwałych z lokalnych surowców dla hutnictwa żelaza”
otrzymał Nagrodę Stalina.
W 1944 roku ten metalurg-badacz opracuje technologię produkcji wysokiej jakości proszku magnezytowego „Extra”. Ten półfabrykat posłużył do przygotowania prasowanego materiału ogniotrwałego stosowanego w szczególnie ważnej produkcji stali pancernej w piecach elektrycznych. Granica temperatury dla takich materiałów ogniotrwałych osiągnęła 2000 stopni.
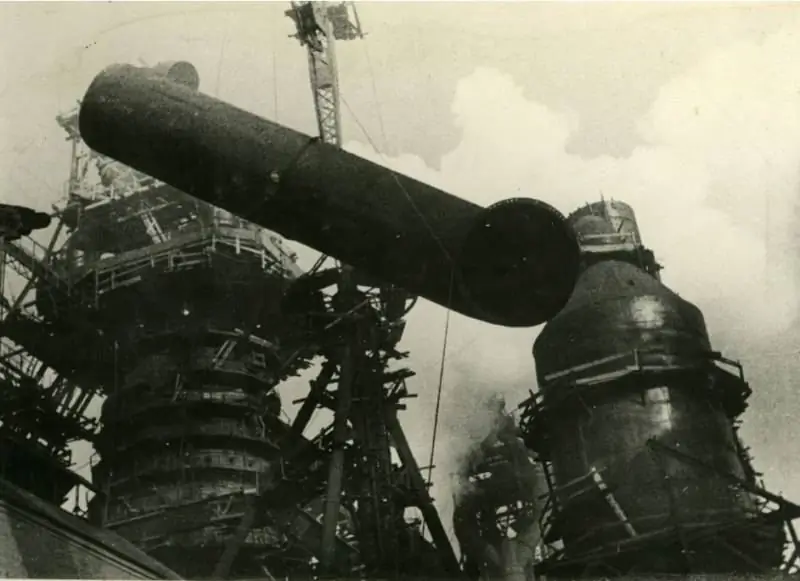
Ale nie należy zakładać, że przykład ogólnie odnoszącej sukcesy fabryki Magnezit rozciągał się na cały przemysł materiałów ogniotrwałych Związku Radzieckiego.
Szczególnie trudna sytuacja zaistniała na Uralu, gdzie w latach 1941-1942 ewakuowano praktycznie całą krajową budowę czołgów.
Zakłady metalurgiczne w Magnitogorsku i Nowotagilsku zostały przeorientowane na produkcję zbroi, dostarczając produkty do Swierdłowska Uralmasz, Czelabińska „Tankograd” i Niżny Tagił fabrykę czołgów nr 183. W tym samym czasie zakłady metalurgiczne posiadały własną produkcję materiałów ogniotrwałych z lokalnych surowców.
Na przykład w Magnitce fabryka dinas-szamot produkowała 65-70 tysięcy ton cegieł rocznie. To nie wystarczało nawet na własne potrzeby, nie mówiąc już o dostawach do innych przedsiębiorstw.
Pierwsze trudności pojawiły się, gdy fabryki czołgów zaczęły budować własne piece grzewcze i cieplne. Metalurgia Uralu ledwo miała już dość materiałów ogniotrwałych, a następnie produkcja kadłubów fabryk czołgów wymagała wysokiej jakości materiałów do wykładania pieców.
Nie było tu mowy o jakichkolwiek chromomagnezytowych materiałach ogniotrwałych - tego materiału brakowało, a nawet eksportowano w zamian za amerykańską pożyczkę Lend-Lease. Przynajmniej o tym wspomina wiele źródeł. Historycy Uralu piszą, że kosztowny chromomagnezyt Panarina mógłby wyjechać za granicę w zamian za rzadkie żelazostopy na opancerzenie czołgów. Ale nie ma na to jeszcze bezpośrednich dowodów.
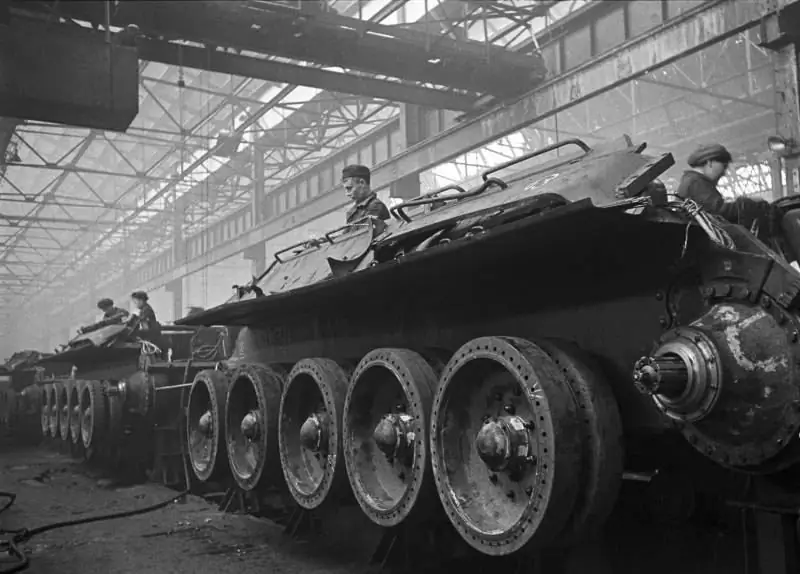
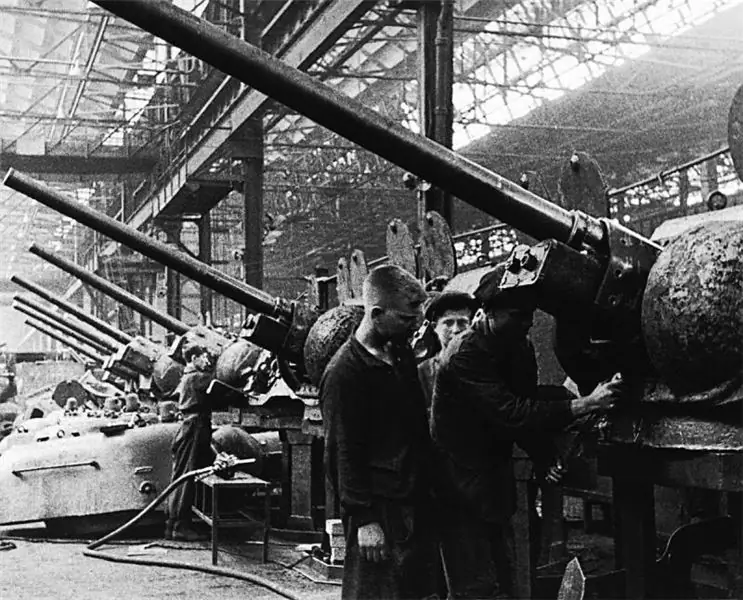
Fabryki czołgów opierały się głównie na materiale ogniotrwałym dinas produkowanym przez fabrykę Pervouralsk. Ale, po pierwsze, produkowano go tylko 12 tysięcy ton miesięcznie, a po drugie, lwią część wzięli metalurdzy.
Rozwój produkcji w zakładzie w Pervouralsku przebiegał bardzo powoli. A do połowy 1942 roku pojawiły się tylko 4 nowe piece. Reszta albo nie była gotowa, albo generalnie istniała tylko w projektach.
Materiały ogniotrwałe do pieców martenowskich w fabrykach czołgów często były złej jakości, nie w pełni iw niewłaściwym czasie. Tylko do naprawy pieców Uralmash w czwartym kwartale 1942 r. potrzebnych było 1035 ton cegieł ogniotrwałych, a otrzymano tylko około 827 ton.
W 1943 r. Zasadniczo sklep z otwartym paleniskiem Uralmash prawie zatrzymał się z powodu braku materiałów ogniotrwałych do naprawy.
Jakość materiałów ogniotrwałych dostarczanych przez całą wojnę pozostawiała wiele do życzenia. Jeśli w normalnych warunkach cegła dynasowa pieca martenowskiego mogła wytrzymać 400 żarów, to w czasie wojny nie przekroczyła 135 żarów. A do marca 1943 r. ten parametr spadł do 30-40 biegów.
Ta sytuacja wyraźnie pokazuje, jak brak jednego zasobu (w tym przypadku ogniotrwałego) może poważnie spowolnić pracę całego przemysłu obronnego. Jak pisze w swoich pracach kandydat nauk historycznych Nikita Mielnikow, w marcu 1943 r. Trzy piece martenowskie Uralmasza nadal zatrzymały się i przeprowadziły pełny cykl prac naprawczych. Zajęło 2346 ton dinas, 580 ton szamotu i 86 ton deficytowego magnezytu.
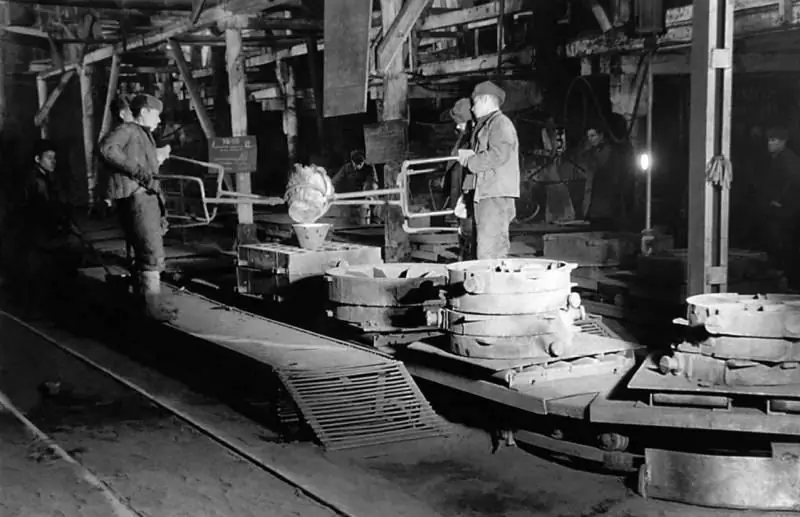
W połowie 1942 r. w fabryce czołgów nr 183 sytuacja rozwijała się podobnie - produkcja stali pozostawała w tyle za montażem mechanicznym. I musieliśmy „importować” kadłuby T-34 z Uralmasha.
Jednym z powodów był brak materiałów ogniotrwałych do remontu pieców martenowskich, które wiosną 1942 r. pracowały na granicy wytrzymałości. W efekcie jesienią pracowały tylko 2 z 6 pieców martenowskich, a hutnictwo przywrócono dopiero w drugiej połowie 1943 roku.
Sytuacja z materiałami ogniotrwałymi w strukturze sowieckiego kompleksu obronnego podczas Wielkiej Wojny Ojczyźnianej wyraźnie ilustruje złożoność sytuacji na tyłach kraju.
Chroniczny niedobór na ogół nie najnowocześniejszego produktu wpłynął bezpośrednio na tempo produkcji pojazdów opancerzonych.