Najpierw popracujmy nad błędami z poprzedniego artykułu. W nim autor przekonywał, że przed wojną ZSRR opanował produkcję tokarko-wiercących maszyn zdolnych do obróbki pasów naramiennych czołgów o dużej średnicy, podczas gdy pierwsze maszyny o średnicy płyty czołowej 2000 mm zostały wyprodukowane w 1937 roku.
Niestety, jest to (przynajmniej częściowo) niepoprawne. Niestety historia budowy obrabiarek w ZSRR nie jest dobrze opisana w naszym kraju i niezmiernie trudno jest znaleźć odpowiednią literaturę. Autorowi tego artykułu w końcu udało się zdobyć bardzo szczegółową pracę L. A. Aizenstadt. oraz Chikhacheva S. A. pt. „Eseje o historii budowy obrabiarek w ZSRR” (Maszgiz, 1957). Według LA Aizenstadt. oraz Chikhacheva S. A. pierwsza jednokolumnowa tokarka tokarsko-wytaczarska o średnicy płyty czołowej 800 mm została wyprodukowana w zakładzie Sedin (Krasnodar) w 1935 roku. Podobno mówimy o maszynie 152, choć to niestety nieścisłe - autorzy Szkiców, niestety nie podał nazw tokarek pionowych produkowanych przed wojną. Jednocześnie, jak wynika z porównania „Szkiców” z danymi o historii zakładu zamieszczonymi na jego oficjalnej stronie internetowej, mimo wyprodukowania pierwszej próbki w 1935 r., maszyna 152 została przyjęta przez komisję państwową z rezolucja „przydatna do użytku” dopiero w 1937 r.
Jeśli chodzi o inne modele tokarek wytaczarskich, „Szkice” podają, że w 1940 roku wyprodukowano jeszcze dwa modele maszyn: jednokolumnową o średnicy płyty czołowej 1450 mm i maszynę dwukolumnową o średnicy płyty czołowej 2000 mm. Niestety zupełnie nie wiadomo, czy mówimy o produkcji eksperymentalnej, czy masowej.
Chociaż nie dotyczy to omawianego tematu, to ciekawe, że w zakładzie nazwanym jego imieniem. Sedin w 1941 roku zakończono produkcję gigantycznej tokarko-wytaczarki o masie 520 ton o średnicy płyty czołowej 9 m - ta maszyna została zmontowana przez zakład im. S. Swierdłow w Leningradzie.
Wracając do tematu czołgów, stwierdzamy, że dwie bardzo ważne kwestie pozostają nierozwiązane. Po pierwsze, niestety, autorowi nigdy nie udało się ustalić, czy przed wybuchem wojny i w jej trakcie w ZSRR powstała seryjna produkcja tokarek karuzelowych o średnicy tarczy 2000 mm, a jeśli powstała, to ile maszyny były produkowane w całości w latach przedwojennych i wojennych. Jak wiesz, posadź je. Sedina przebywała na okupowanym terytorium od 9 sierpnia 1942 r. do 12 lutego 1943 r., ale przed odwrotem Niemcy prawie całkowicie zniszczyli fabrykę. Ale co to może nam powiedzieć? Można było na nim wykonać pewną liczbę obrabiarek przed „zajęciem” zakładu, ponadto sprzęt potrzebny do produkcji obrabiarek mógł zostać wyjęty podczas ewakuacji, a następnie produkcja tokarek i wytaczarek zostały już gdzieś ustalone. Z drugiej strony autor tego artykułu nie znalazł o tym żadnej wzmianki. Oto LA Aisenstadt. oraz Chikhachev S. A. nic nie mówią o wojskowej produkcji wytaczarek. Ale jednocześnie szanowani autorzy piszą, że podczas Wielkiej Wojny Ojczyźnianej przemysł obrabiarkowy ZSRR opanował produkcję dużej liczby obrabiarek o nowych konstrukcjach, podają wiele przykładów, ale wskazują wprost, że jest to absolutnie niemożliwe jest ich szczegółowe wymienienie w ramach jednej pracy. Może produkcja tokarek pionowych pozostawała poza zakresem ich pracy?
Drugie pytanie: niestety nie wiadomo, czy było możliwe zorganizowanie produkcji pasów naramiennych do czołgów na tych maszynach, skoro, jak słusznie zauważyło wielu szanownych czytelników w komentarzach do poprzedniego artykułu, fakt, że średnica płyty czołowej jest większa niż średnica paska na ramię nie gwarantuje takiej możliwości.
Chodzi o to, że średnica paska na ramię do zbiornika to jedno, ale wymiary części, którą należy umieścić na płycie czołowej, aby przetworzyć pasek na ramię na zbiornik, są zupełnie inne. Niemniej jednak na drugie pytanie najprawdopodobniej można odpowiedzieć twierdząco, ponieważ nie należy zakładać, że do obróbki paska naramiennego czołgu konieczne było osadzenie całej wieży na wytaczarce. W końcu pasek na ramię wieży był jedną z jego części i, jak widać na zdjęciu z tamtych lat, był przetwarzany oddzielnie od wieży. A więc na przykład na cytowanym wcześniej zdjęciu nudnej tokarki.
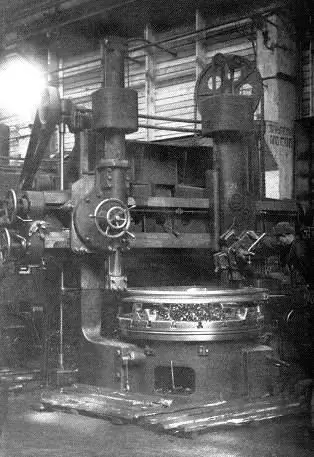
Właśnie uchwycono procedurę obróbki pasa naramiennego dla czołgu T-34 w fabryce nr 183 w 1942 r. Kolejne zdjęcie.
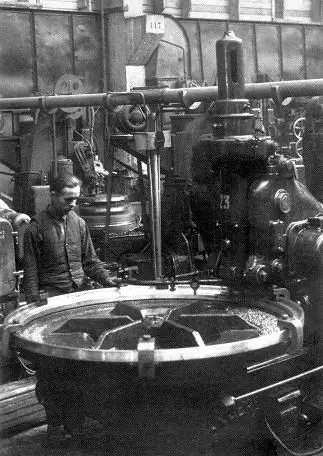
Pokazuje procedurę wycinania zębów paska na ramię wieży w tym samym zakładzie nr 183 w tym samym 1942 roku, ale oczywiście na innym typie maszyny. Jak widać na obu zdjęciach, rozmiar obrabianych części jest znacznie mniejszy od wieży T-34 i być może dość zbliżony do średnicy paska naramiennego.
W związku z tym pytanie, czy tokarko-wiertarki odpowiednie do obróbki szerokich pasów naramiennych wież T-34M i T-34-85 były produkowane w ZSRR przed wojną, pozostaje kontrowersyjne. Ale nie ma wątpliwości, że jeszcze przed wybuchem Wielkiej Wojny Ojczyźnianej nasze fabryki dysponowały dużą flotą takich maszyn o dużej średnicy płyty czołowej, ponieważ pozostałe rozważania autora wyrażone w poprzednim artykule pozostają aktualne. Oczywiście potrzebowaliśmy obrabiarek do produkcji kół lokomotyw, koparek i innego sprzętu, a jeśli nie były produkcji radzieckiej, to oczywiście kupowaliśmy za granicą. Przypomnijmy też list podpułkownika I. Panowa, który w 1940 r. donosił, że zakład nr 183 posiada wystarczający park maszynowy do produkcji czołgów z przedłużonymi pasami naramiennymi. Przypomnijmy, że zamówienia z 1941 r. na zakup sprzętu importowanego z fabryk nr 183 i 75 oraz STZ nie zawierały maszyn tokarskich. I to pomimo faktu, że zakład nr 183 miał rozpocząć produkcję T-34M z szerokim pierścieniem wieży w 1941 roku, a STZ musiał być gotowy do wprowadzenia T-34 do serii od 1 stycznia, 1942. Przypomnijmy, że produkcja T-34-85 rozpoczęła się w naszych fabrykach wcześniej niż miały przybyć importowane maszyny w ramach Lend-Lease itp. I oczywiście do produkcji 250 zbiorników IS-2 miesięcznie Zakład nr 200 potrzebował 7 wytaczarek o dużej średnicy płyty czołowej, a ile z nich było potrzebnych do Zakładu nr 183, który wyprodukował do 750 T-34-85 miesięcznie? Czy jego potrzeby mogłyby zaspokoić kilka maszyn, które otrzymaliśmy w ramach Lend-Lease?
A jeśli pamiętacie też, że do tej pory nikt nie podał do publicznej wiadomości danych o wielkościach dostaw tokarek pionowych w ramach Lend-Lease, to okazuje się to całkiem interesujące. Wiemy, że ZSRR zamierzał zamawiać takie maszyny za granicę, aby zrealizować program produkcyjny z 1944 roku, ale nie wiemy, czy zostały zamówione, a jeśli tak, to czy zostały dostarczone, kiedy iw jakiej ilości. Podobnie nie wiadomo, czy takie maszyny były dostarczane w ramach Lend-Lease wcześniej, czy innymi kanałami: w latach wojny ZSRR nabył produkty, które nie znalazły się na listach dozwolonych w ramach Lend-Lease, czyli jako część zwykłych transakcji kupna i sprzedaży.
Zakończmy ten temat na tokarkach pionowych i przejdźmy do specyfiki produkcji T-34 w latach 1941-42.
Tak więc, jak powiedzieliśmy wcześniej, w momencie wprowadzenia do masowej produkcji projekt T-34 zawierał szereg niedociągnięć, z których głównymi była niewystarczająca liczebność załogi, słaba widoczność z czołgu i znaczne niedociągnięcia w skrzyni biegów. Ponadto czołg cierpiał na sporo „choroby wieku dziecięcego”, które można było łatwo wyeliminować zgodnie z wynikami eksperymentalnej eksploatacji. I jakby tego było mało, fabryki, w których planowano uruchomić produkcję T-34, nie produkowały wcześniej czołgów średnich, ponieważ lekkie czołgi BT były produkowane w fabryce nr 183, a w STZ nie produkowano wcześniej żadnych czołgów..
Wady T-34 zostały dobrze zrozumiane przez nasze kierownictwo, mimo to podjęto decyzję o skierowaniu czołgu do masowej produkcji. Są 2 główne powody tej decyzji. Pierwszym z nich było to, że nawet w obecnej formie T-34 zdecydowanie przewyższał pod względem bojowym czołgi lekkie BT-7, nie wspominając o żadnym T-26 i tak dalej. Po drugie, nie było możliwe zorganizowanie produkcji tak nowej i złożonej maszyny, jaką był T-34, dla fabryk nr 183 i STZ jednocześnie, konieczne było zbudowanie efektywnego łańcucha produkcyjnego w przedsiębiorstwach i nie mniej efektywna interakcja z kontrahentami-dostawcami.
Dlatego zdecydowano się produkować T-34 w jego obecnej formie, ale jednocześnie opracować ulepszoną, zmodernizowaną konstrukcję czołgu, która oszczędziłaby znanych wad konstrukcyjnych. Projekt tego czołgu znany jest jako T-34M - oto kopuła dowódcy i pięciu członków załogi oraz wieża z szerokim pasem naramiennym i nowa skrzynia biegów… W tym samym czasie T-34M był ma wejść do masowej produkcji w 1941 roku i stopniowo wypierać model T-34 1940
Oczywiście takie rozwiązanie pozwalało zabić nie dwa, ale kilka ptaków jednym kamieniem. Z jednej strony Armia Czerwona natychmiast zaczęła otrzymywać czołgi średnie z działem 76, 2 mm i pancerzem przeciwdziałowym. Żołnierze zaczęli przygotowywać dla nich nowy, nietypowy sprzęt. Fabryki - rozwijanie procesów produkcyjnych i efektywności ich łańcuchów dostaw. Ceną za to było to, że T-34 został dostarczony żołnierzom ze znanymi, ale nie wyeliminowanymi niedociągnięciami. Oczywiście można było obrać inną ścieżkę i odłożyć wydanie T-34, dopóki wszystkie jego niedociągnięcia nie zostaną wyeliminowane, ale najwyraźniej kierownictwo Armii Czerwonej słusznie uważało, że lepiej mieć w oddziałach niedoskonały czołg niż nie mieć dobrego… A poza tym, skoro projekt T-34M i jego jednostki są gotowe, rodzimy przemysł byłby w miarę możliwości przygotowany do jego seryjnej produkcji.
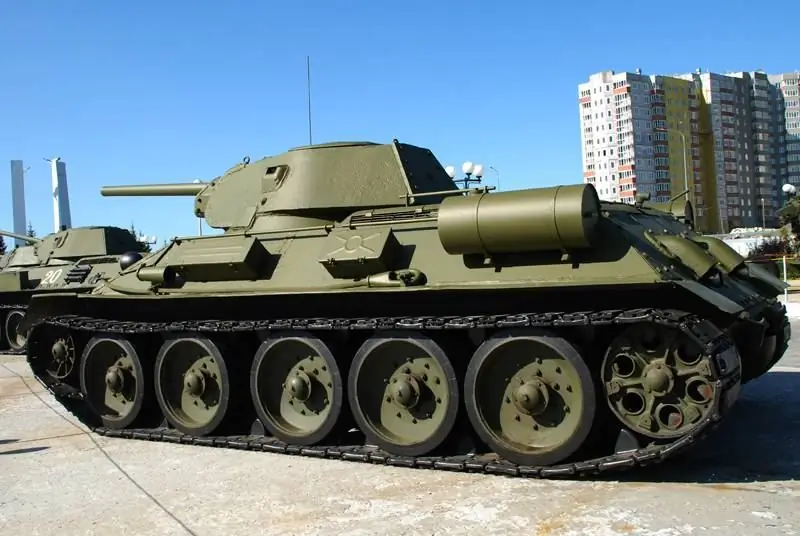
Widzimy więc, że produkcja „wilgotnego” T-34 przed wojną ma całkiem rozsądne wyjaśnienia. Ale tutaj pojawia się kolejne pytanie. Z podejściem opisanym powyżej, odrzucenie jakiejkolwiek poważnej modernizacji T-34 mod. 1940 - nie miało to sensu, bo już w 1941 miał trafić do serii T-34M. Ale wojna się rozpoczęła, nowy silnik wysokoprężny do T-34M nigdy nie był gotowy i stało się jasne, że żaden „trzydzieści cztery” nie trafi do wojska. Po co więc pierwsze zmiany na lepsze - nowy punkt kontrolny, kopuła dowódcy itp. pojawił się na seryjnych T-34 dopiero w 1943 roku? Co wcześniej powstrzymało cię przed zrobieniem tego?
Bardzo często w opisach T-34 zwraca się uwagę na prostotę konstrukcji czołgu, dzięki której możliwe było uruchomienie jego masowej produkcji w wojującym ZSRR. Jest to niewątpliwie słuszne, ale należy zauważyć, że T-34 nie zdobył tej zasługi od razu. Oczywiście twórcy czołgu, M. I. Koskin i AA Morozow, włożył wiele wysiłku w osiągnięcie znakomitego wyniku bez uciekania się do skomplikowanych rozwiązań technicznych. Niemniej jednak konstrukcja T-34 z 1940 roku okazała się bardzo trudna dla naszych fabryk, które miały go produkować, zwłaszcza w czasie wojny. Na przykład „Historia budowy czołgów w fabryce czołgów Ural №183 o nazwie. Stalin „wskazuje, że „Projekt części pancernych… przeprowadzono bez uwzględnienia możliwości technologicznych, w wyniku czego zaprojektowano takie części… których produkcja w produkcji seryjnej byłaby niemożliwa…”. Jednocześnie niestety początkowo „…technologia produkcji została zaprojektowana z myślą o dostępności wykwalifikowanych pracowników, którzy mogliby przy użyciu uniwersalnego sprzętu, w małych partiach, wykonywać obróbkę skomplikowanych części zbiorników, a jakość obróbki zależała od kwalifikacji pracownika."
Mówiąc najprościej, konstruktorzy stworzyli obiecujący projekt czołgu, ale szybko okazało się, że jego konstrukcja jest daleka od optymalnej do produkcji na sprzęcie dostępnym w Zakładzie nr 183 lub wymaga wysoko wykwalifikowanego personelu, którego brakowało lub nie posiadało przedsiębiorstwo w ogóle. W niektórych innych procesach zakład mógł mieć wystarczająco dużo sprzętu i wykwalifikowanych pracowników, ale przy stosunkowo niewielkich ilościach masowej produkcji, a czołg miał stać się naprawdę masywny. W związku z tym należało znaleźć kompromis - gdzieś zmienić konstrukcję maszyny lub jej poszczególnych części, a gdzieś kupić i zainstalować nowe maszyny, zmienić technologię produkcji.
Łatwo o tym mówić w przypadku jednego przedsiębiorstwa, ale w niektórych przypadkach takie zmiany konstrukcyjne dotyczyły nie tylko zakładu, w którym wykonywany jest montaż końcowy zbiorników, ale także jego podwykonawców. A teraz pamiętajmy też, że fabryka T-34 nie była osamotniona, a oczywiście park maszynowy i kwalifikacje zatrudnionych na nich pracowników znacznie się różniły.
„O czym myślałeś przed wojną?” Drogi czytelnik zapyta i oczywiście będzie miał rację. Ale pamiętajmy, że wielkość produkcji w 1941 roku wcale nie przerażała wyobraźni: 1800 czołgów dla fabryki nr 183 i 1000 czołgów dla STZ. To tylko 150 i 84 samochody miesięcznie. W przypadku tego programu produkcyjnego kierownictwo przedsiębiorstw określiło potrzebę dodatkowego parku maszynowego, personelu itp. Jednocześnie z początkiem wojny konieczne było kilkukrotne zwiększenie wielkości produkcji, do czego oczywiście park maszynowy i personel STZ i zakładu nr 183 nie był w pełni zaprojektowany.
A mówimy tylko o tych fabrykach, w których planowano produkować T-34 jeszcze przed wojną, a zatem przeprowadzono różne działania przygotowawcze. Ale nie zapominajmy, że w latach 1941-42. produkcję T-34 opanowano w 4 kolejnych zakładach: nr 112, 174, a także UZTM i ChKZ.
Przed wojną zdecydowanie liderem w produkcji T-34 była fabryka nr 183, więc np. w pierwszych 6 miesiącach 1941 r. wyprodukowała 836 czołgów, podczas gdy w STZ tylko 294. W czerwcu 1941 r. fabryka nr 183 wyprodukował 209 pojazdów, a STZ tylko 93. Ale fabryka nr 183 znajdowała się na Ukrainie, w Charkowie i oczywiście pilnie wymagała ewakuacji (do Niżnego Tagila), co nastąpiło między wrześniem a październikiem 1941 r. Oczywiste jest, że coś takiego „przeprowadzka”, nawet w tak krótkim czasie, stałoby się niezwykle trudne nawet w czasie pokoju, ale w czasie wojny był to prawdziwy wyczyn pracy. Biorąc pod uwagę wszystkie powyższe, konieczne było jednoczesne zarządzanie i zwiększenie wielkości produkcji … W grudniu 1941 r. Zakład nr 183 wyprodukował tylko 25 czołgów, w marcu 1942 r. - już 225, przewyższając tym samym wszelkie miesięczna produkcja z okresu przedwojennego, aw kwietniu - 380 pojazdów, czyli o 42,8% wyższa od najlepszej produkcji w Charkowie (266 czołgów w sierpniu 1941 r.).
Jeśli chodzi o STZ, to w przeciwieństwie do fabryki w Charkowie nigdzie się nie przenosiło, ale było na nim wiele problemów nawet bez ewakuacji. Przód „toczył się” coraz bliżej, znaczna część podwykonawców przestała pracować lub nie miała już możliwości dostarczania części zamiennych i komponentów do STZ. Tak więc zakład musiał opanować coraz większą liczbę zakładów produkcyjnych bezpośrednio w domu, a jednocześnie - aby zwiększyć tempo produkcji … co zrobił STZ - produkcja T-34 na nim trwała do momentu rozpoczęcia bitew samo terytorium zakładu (a nawet nieco ponad Togo).
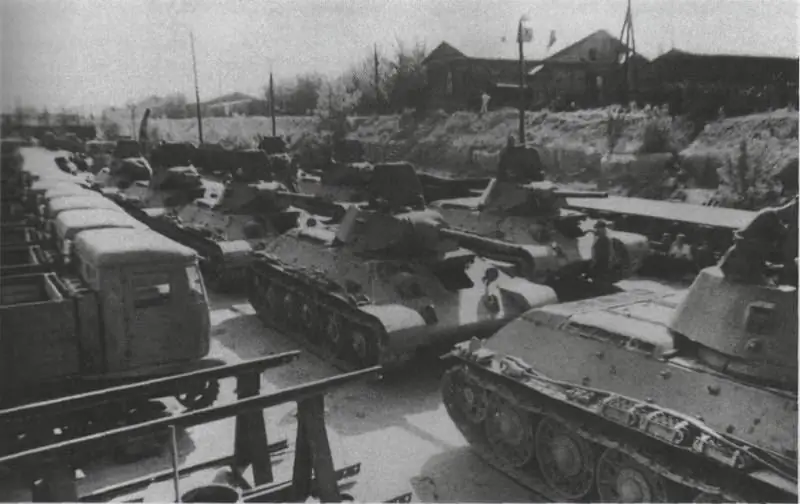
Co do pozostałych fabryk, stanęło przed nimi równie tytaniczne zadanie - w czasie wojny powinni byli opanować produkcję dla nich zupełnie nowego sprzętu. Zakład nr 112 rozpoczął produkcję seryjną we wrześniu 1941 r., pozostałe trzy ww. zakłady - w czerwcu-wrześniu 1942 r.
Jest więc oczywiste, że w takich warunkach wszelkie wysiłki powinny być skoncentrowane właśnie na doprowadzeniu konstrukcji T-34 do poziomu, który umożliwiłby zorganizowanie jego masowej produkcji, a nie opóźnianiu tego wydania przez dalsze komplikowanie jego konstrukcji. Dlatego od co najmniej od zimy 1941 r. (a właściwie nawet wcześniej) projektanci i technolodzy zakładu nr 183 skupili się na pracach w następujących obszarach:
1. Maksymalna możliwa redukcja części drugorzędnych w czołgu, których wyłączenie nie powinno obniżać walorów technicznych i bojowych pojazdu.
2. Redukcja normalnych części używanych w zbiorniku, zarówno pod względem ilości, jak i wielkości.
3. Zmniejszenie miejsc do obróbki na częściach, przy jednoczesnej rewizji czystości obrabianych części.
4. Przejście do produkcji części metodą tłoczenia na zimno i odlewania zamiast stosowanego tłoczenia na gorąco i kucia.
5. Zmniejszenie asortymentu części wymagających obróbki cieplnej, różnego rodzaju powłok antykorozyjnych i dekoracyjnych czy specjalnej obróbki powierzchni.
6. Redukcja zespołów i części pozyskiwanych na zlecenie współpracy z zewnątrz.
7. Zmniejszenie zakresu gatunków i profili materiałów użytych do produkcji zbiornika.
8. Przeniesienie części wykonanych z materiałów deficytowych do produkcji z materiałów zastępczych.
9. Rozbudowa, o ile pozwalają na to warunki eksploatacji, dopuszczalne odchylenia od warunków technicznych.
Tak więc w latach 1941-1942. w tych obszarach osiągnięto niesamowite rezultaty. Od stycznia 1942 r. dokonano zmian w rysunkach 770 części i całkowicie zrezygnowano z używania 1265 nazw części. Wydaje się, że to fantastyczna figura, ale w 1942 roku udało się wykluczyć 4972 kolejne nazwy części z projektu T-34!
Oczywiście uproszczenie czy eliminacja detali nie wystarczyły. Zmieniły się również procesy technologiczne. I tak np. do końca 1941 roku można było zrezygnować z obróbki spawanych krawędzi elementów pancernych. Spowodowało to, że złożoność wykonania jednego zestawu zmniejszyła się z 280 do 62 maszynogodzin, liczba prac wykończeniowych o połowę, a walców prostujących o połowę.
Oczywiście upraszczanie technologii było mieczem obosiecznym. Z jednej strony produkcja została uproszczona i tańsza, z drugiej niestety jakość spadała: np. odrzucenie obróbki skrawaniem spowodowało wzrost wymagań co do jakości spawów części pancernych itp. Jednak krajowi projektanci i technolodzy doskonale rozumieli te relacje, starając się zrekompensować uproszczenia w konstrukcji T-34 najnowszymi technologiami, takimi jak wprowadzenie automatycznego spawania, które testowano jeszcze przed wojną, ale było masowo wprowadzane już podczas działań wojennych. Lub, na przykład, takie jak walcowanie pasków pomiarowych o szerokości równej gotowym częściom. Często zastosowanie takich technologii nie tylko kompensowało uproszczenie konstrukcji, ale również samo w sobie przynosiło znaczne oszczędności. Spawanie automatyczne znacznie obniżyło więc wymagania dotyczące kwalifikacji pracowników i ich kosztów pracy, a wynajem pasków pomiarowych obniżył koszty robocizny na uzyskiwane z nich części o 36%, obniżył zużycie stali pancernej o 15%, a także obniżył zużycie sprężonego powietrza o 15 tysięcy metrów sześciennych. m. dla 1000 budynków. Oczywiście, dzięki drastycznemu uproszczeniu konstrukcji i technologii trzydziestu czterech, możliwe było drastyczne obniżenie jego kosztów, na przykład koszt T-34-76 wyprodukowany przez fabrykę nr 183:
Wydanie z 1939 r. - 596.373 ruble;
Wydanie z 1940 r. - 429 256 rubli;
Wydanie z 1941 r. - 249 256 rubli;
I wreszcie 1942 - 165.810 rubli.
Niestety, z dużym prawdopodobieństwem nie zawsze było możliwe połączenie uproszczeń i technologii, które je kompensują w odpowiednim czasie i należy założyć, że poszczególne partie T-34 wyprodukowane w tym okresie mogły być znacznie bardziej wrażliwe niż „referencyjne” czołgi mod. 1940, wyprodukowany przed jakimikolwiek uproszczeniami.
Oczywiście w latach 1941-42. ZSRR zdołał rozwiązać problem wybuchowego wzrostu produkcji T-34. W 1941 roku wyprodukowano "trzydzieści cztery" 3 016 aut, w 1942 - 12 535 aut. Maksymalna miesięczna produkcja czołgów tego typu w 1941 r. została osiągnięta w maju i wyniosła 421 pojazdów/miesiąc, a w 1942 r. minimalna produkcja miesięczna była wyższa i wyniosła 464 czołgi (w styczniu). W grudniu 1942 r. udało im się podnieść go do 1568 pojazdów!
Jednocześnie historycy słusznie twierdzą, że niezwykle trudno jest jakoś rozdzielić ten przepływ między modyfikacje czołgów. Dla Niemców wszystko było proste - produkowany jest czołg o określonej konstrukcji i niech będzie dla siebie. Potem wymyślili, jak go ulepszyć, wprowadzili zmiany - dodali literę do nazwy czołgu i to jest modyfikacja. Wymyślili nowe ulepszenia - kolejną literą oznaczyli ulepszony samochód itp. Inaczej było w przypadku T-34 w ZSRR. Faktem jest, że ciągłe zmiany w konstrukcji i technologii, a także dostosowywanie konstrukcji czołgu do możliwości każdego konkretnego zakładu doprowadziły do tego, że T-34 o tym samym czasie produkcji, ale różnych zakładach lub różnych partiach te same zakłady były często daleko od tych samych maszyn… Wiele zależało od technologii, które opanował dany zakład, więc w 1942 r. T-34 z fabryki nr 183 kosztował, jak wspomniano powyżej, 165.810 rubli, ale T-34, wyprodukowany w „sąsiednim” UZTM (Czelabińsk). - 273 800 rubli.
Innymi słowy, o „trzydziestu czterech” z lat 1941-42. wydanie można powiedzieć nie jako pojedynczy czołg T-34 o różnych modyfikacjach, ale na całą rodzinę czołgów, w przybliżeniu o tych samych parametrach wydajności, ale mających znaczne różnice w konstrukcji, stale dostosowujące się do równie stale zmieniającej się technologii produkcji w różnych fabrykach.
Czy możliwe było wprowadzenie jakichkolwiek zmian w konstrukcji czołgu T-34? Zapewne jest to możliwe, ale takie zmiany z pewnością spowodowałyby spadek wydajności - ich opanowanie zajęłoby trochę czasu. Czy stać nas na zmniejszenie produkcji T-34? Przypomnijmy, że w 1942 roku wyprodukowaliśmy (bez dział samobieżnych) 24 448 czołgów, w tym:
KV wszystkich modyfikacji - 2 553 szt. (10,4% całości emisji);
T-34-76 - 12 535 (51, 3%);
T-60 - 4 477 (18,3%);
T-70 - 4 883 (20%).
Jak wiecie, jeszcze przed wybuchem Wielkiej Wojny Ojczyźnianej kierownictwo Armii Czerwonej i kraj doskonale rozumiało, że czołgi z pancerzem kuloodpornym są kategorycznie przestarzałe, a jeśli nadawały się do czegoś innego, to tylko do wykonywania jakiegoś pomocniczego Funkcje. Niemniej jednak, w 1942 r. 38, 3% wszystkich wyprodukowanych czołgów stanowiły lekkie T-60 i T-70 z 15-milimetrowymi bokami, załoga złożona odpowiednio z dwóch i 20-mm i 45-mm dział.
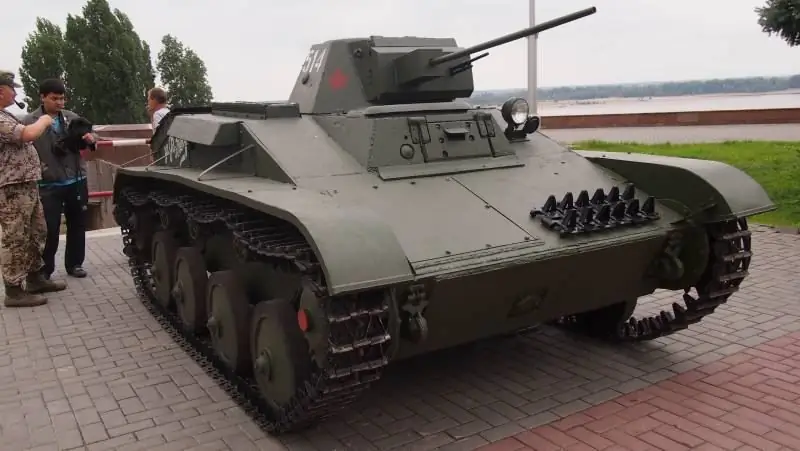
Taki przepływ można wytłumaczyć niezwykle prosto - Armii Czerwonej kategorycznie brakowało czołgów, a każdy, nawet najgorszy czołg, jest znacznie lepszy niż jego brak. Ale w rezultacie nasza armia została zmuszona do używania T-60 i T-70 jako, że tak powiem, głównych czołgów bojowych, chociaż oczywiście taka koncepcja nie istniała w tamtych latach. Oczywiście skutkiem tego, że w tym czasie lekkie pojazdy opancerzone były zmuszone do wykonywania całego szeregu zadań, jakie stawały przed siłami czołgów tamtych czasów, były niezwykle wysokie straty zarówno pojazdów opancerzonych, jak i ich załóg.
Czy można było w tym czasie zmniejszyć produkcję T-34, który w tamtych czasach (1941-42) nadal zachowywał tytuł czołgu z opancerzeniem przeciwdziałowym?
Często w komentarzach do niektórych publikacji trzeba przeczytać, że, jak mówią, masowa produkcja niezmodernizowanych T-34, a często nawet nie najlepszej jakości, „doskonała” charakteryzuje kanibalistyczny charakter ówczesnego kierownictwa ZSRR i, oczywiście towarzysz Stalin osobiście. Ale gdyby pracownicy produkcyjni terminowo zajęli się nowym punktem kontrolnym i kopułą dowódcy, to straty w załogach T-34 byłyby znacznie mniejsze niż w rzeczywistości.
Oczywiście straty wśród czołgistów byłyby w tym przypadku mniejsze. Ale w oddziałach będzie mniej czołgów. A kto może policzyć, ilu dodatkowych strzelców, strzelców maszynowych, artylerzystów i innych żołnierzy, którzy pozostali bez wsparcia czołgów w wyniku zmniejszenia ich produkcji w stosunku do tego, co faktycznie osiągnięto, spadłoby na ziemię?
Arytmetyka to w rzeczywistości koszmar. I trudno przewidzieć nawet teraz, dla nas ludzi, w następstwie analizy wydarzeń tamtych krwawych dni. I decydować, co jest słuszne, a co nie, w tamtych latach … Być może oczywiście kierownictwo nie działało całkiem optymalnie. Może wprowadzenie wież tego samego dowódcy nie spowolniłoby tak bardzo produkcji, kto wie? Tutaj konieczna jest analiza zmian pracochłonności, a także możliwości parku maszynowego każdego zakładu… wszystko to daleko wykracza poza wiedzę autora tego artykułu. Ale nie ma wątpliwości co do jednego - stawka na wszechstronne rozszerzenie produkcji T-34, która została wykonana w najtrudniejszych warunkach 1941-42. dopiero później, po osiągnięciu przez 5 zakładów produkcyjnych zdolności projektowych, modernizacja T-34 wydaje się całkiem rozsądną alternatywą dla każdej innej decyzji, która mogła zostać podjęta w tamtym czasie.