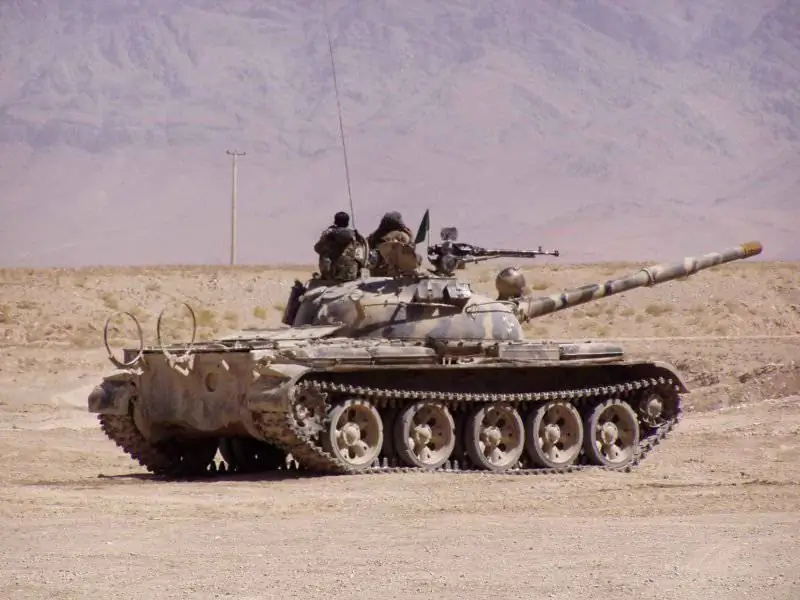
W 1955 r. podjęto decyzję rządu o utworzeniu biura projektowego specjalnej inżynierii diesla w Charkowskim Zakładzie Inżynierii Transportu i o stworzeniu nowego czołgowego silnika diesla. Profesor AD Charomsky został mianowany głównym projektantem biura projektowego.

O wyborze schematu konstrukcyjnego przyszłego silnika wysokoprężnego zadecydowało głównie doświadczenie w pracy na 2-suwowych silnikach wysokoprężnych OND TsIAM i silniku U-305, a także chęć spełnienia wymagań konstruktorów nowego T Czołg -64, opracowany w tym zakładzie pod kierownictwem głównego projektanta AA… Morozov: zapewnienie minimalnych wymiarów silnika wysokoprężnego, zwłaszcza wysokości, w połączeniu z możliwością umieszczenia go w zbiorniku w pozycji poprzecznej między pokładowymi przekładniami planetarnymi. Wybrano dwusuwowy układ diesla z poziomym układem pięciu cylindrów z tłokami poruszającymi się w nich przeciwnie. Postanowiono wykonać silnik z pompowaniem i wykorzystaniem energii spalin w turbinie.
Jakie było uzasadnienie wyboru 2-suwowego silnika wysokoprężnego?
Wcześniej, w latach 20.-1930., stworzenie 2-suwowego silnika wysokoprężnego do pojazdów lotniczych i naziemnych zostało wstrzymane z powodu wielu nierozwiązanych problemów, których nie można było rozwiązać przy poziomie wiedzy, doświadczenia i możliwości krajowego przemysłu zgromadzonego przez ten czas.
Badania i badania dwusuwowych silników wysokoprężnych niektórych firm zagranicznych doprowadziły do wniosku o znacznej trudności w opanowaniu ich w produkcji. Tak więc na przykład badanie Centralnego Instytutu Motoryzacji Lotniczej (CIAM) w latach 30-tych nad silnikiem wysokoprężnym Jumo-4 zaprojektowanym przez Hugo Juneckersa wykazało znaczne problemy związane z rozwojem takich silników w produkcji takich silników przez krajową przemysł tego okresu. Wiadomo było również, że Anglia i Japonia, po zakupie licencji na ten silnik wysokoprężny, poniosły awarie w rozwoju silnika Junkersa. Jednocześnie w latach 30. i 40. prowadzono już w naszym kraju prace badawcze nad 2-suwowymi silnikami wysokoprężnymi i wyprodukowano eksperymentalne próbki takich silników. Wiodąca rola w tych pracach przypadła specjalistom CIAM, aw szczególności jego Działowi Silników Olejowych (OND). CIAM projektował i wykonywał próbki 2-suwowych silników Diesla o różnych wymiarach: OH-2 (12/16, 3), OH-16 (11/14), OH-17 (18/20), OH-4 (8/ 9) oraz szereg innych oryginalnych silników.
Wśród nich był silnik FED-8, zaprojektowany pod kierunkiem wybitnych naukowców zajmujących się silnikami B. S. Stechkin, N. R. Briling, A. A. Bessonov. Był to 2-suwowy 16-cylindrowy lotniczy silnik wysokoprężny w kształcie litery X z rozdziałem gazu zaworowo-tłokowego, o wymiarach 18/23, rozwijający moc 1470 kW (2000 KM). Jednym z przedstawicieli 2-suwowych silników wysokoprężnych z doładowaniem jest 6-cylindrowy turbotłokowy silnik wysokoprężny w kształcie gwiazdy o mocy 147…220 kW (200…300 KM) produkowany w CIAM pod kierownictwem BS Steczkin. Moc turbiny gazowej przenoszona była na wał korbowy poprzez odpowiednią skrzynię biegów.
Decyzja podjęta wówczas podczas tworzenia silnika FED-8 w zakresie samego pomysłu i schematu projektowego była znaczącym krokiem naprzód. Jednak proces roboczy, a zwłaszcza proces wymiany gazowej przy wysokim ciśnieniu i przedmuchiwaniu pętli, nie zostały wstępnie opracowane. Dlatego też diesel FED-8 nie doczekał się dalszego rozwoju i w 1937 roku prace nad nim przerwano.
Po wojnie niemiecka dokumentacja techniczna przeszła na własność ZSRR. Wpada w AD Charomsky jako twórca silników lotniczych i interesuje go walizka Junkersa.
Walizka Junkersa - seria lotniczych dwusuwowych silników turbotłokowych Jumo 205 z przeciwbieżnie poruszającymi się tłokami powstała na początku lat 30-tych XX wieku. Charakterystyka silnika Jumo 205-C jest następująca: 6-cylindrowy, 600 KM. skok 2 x 160 mm, pojemność skokowa 16,62 litra, stopień sprężania 17:1, przy 2200 obr/min
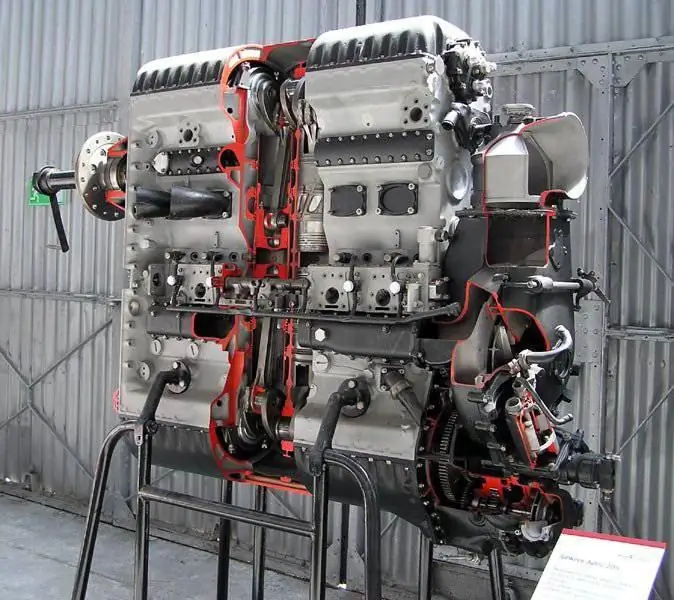
Silnik Jumo 205
W czasie wojny wyprodukowano około 900 silników, które z powodzeniem stosowano na wodnosamolotach Do-18, Do-27, a później na szybkich łodziach. Wkrótce po zakończeniu II wojny światowej, w 1949 roku, postanowiono zamontować takie silniki na wschodnioniemieckich łodziach patrolowych, które służyły do lat 60-tych.
Na podstawie tych osiągnięć AD Charomsky w 1947 r. W ZSRR stworzył dwusuwowy samolot wysokoprężny M-305 i jednocylindrową komorę tego silnika U-305. Ten silnik wysokoprężny rozwijał moc 7350 kW (10 000 KM) o niskim ciężarze właściwym (0, 5 kg/h.p.) i niskim jednostkowym zużyciu paliwa -190 g/kWh (140 g/h.p.h). Przyjęto układ 28 cylindrów w kształcie litery X (cztery 7-cylindrowe bloki). Wybrano wymiar silnika równy 12/12. Wysokie doładowanie zapewniała turbosprężarka połączona mechanicznie z wałem Diesla. Aby sprawdzić główne cechy określone w projekcie M-305, opracować proces pracy i konstrukcję części, zbudowano eksperymentalny model silnika, który miał indeks U-305. G. V. Orlova, N. I. Rudakov, L. V. Ustinova, N. S. Zolotarev, SM Shifrin, N. S. Sobolev, a także technolodzy i pracownicy zakładu pilotażowego CIAM i warsztatu OND.
Projekt pełnowymiarowego samolotu z silnikiem wysokoprężnym M-305 nie został zrealizowany, ponieważ prace CIAM, podobnie jak całego przemysłu lotniczego kraju, już w tym czasie koncentrowały się na rozwoju silników turboodrzutowych i turbośmigłowych oraz potrzebie Zniknął silnik wysokoprężny o mocy 10 000 koni mechanicznych dla lotnictwa.
Wysokie wskaźniki uzyskane na silniku wysokoprężnym U-305: litrowa moc silnika 99 kW/l (135 KM/l), litrowa moc z jednego cylindra prawie 220 kW (300 KM) przy ciśnieniu doładowania 0,35 MPa; wysoka prędkość obrotowa (3500 obr/min) oraz dane z szeregu udanych długoterminowych testów silnika - potwierdziły możliwość stworzenia efektywnego małogabarytowego 2-suwowego silnika wysokoprężnego do celów transportowych o podobnych wskaźnikach i elementach konstrukcyjnych.
W 1952 r. laboratorium nr 7 (dawne OND) CIAM zostało przekształcone decyzją rządu w Laboratorium Badawcze Silników (NILD) podporządkowane Ministerstwu Inżynierii Transportu. Grupa inicjatywna pracowników - wysoko wykwalifikowani specjaliści od silników Diesla (G. V. Orlova, N. I. Rudakov, S. M. Shifrin itp.), kierowana przez profesora A. D. Charomsky'ego, jest już w NILD (później - NIID). 2-suwowy silnik U-305.
Diesel 5TDF
W 1954 r. A. D. Charomsky złożył rządowi propozycję stworzenia dwusuwowego silnika wysokoprężnego. Ta propozycja zbiegła się z wymaganiami głównego projektanta nowego czołgu A. A. Morozow i A. D. Charomsky został mianowany głównym projektantem zakładu. V. Malyshev w Charkowie.
Ponieważ biuro projektowania silników czołgów tego zakładu pozostało głównie w Czelabińsku, A. D. Charomsky musiał stworzyć nowe biuro projektowe, stworzyć bazę eksperymentalną, uruchomić produkcję pilotażową i seryjną oraz opracować technologię, której zakład nie miał. Prace rozpoczęto od wyprodukowania jednostki jednocylindrowej (OTsU), podobnej do silnika U-305. W OTsU opracowywano elementy i procesy przyszłego pełnowymiarowego czołgowego silnika wysokoprężnego.
Głównymi uczestnikami tej pracy byli A. D. Charomsky, G. A. Volkov, L. L. Golinets, B. M. Kugel, M. A., Meksin, I. L. Rovensky i inni.
W 1955 r. Pracownicy NILD dołączyli do prac projektowych w zakładzie diesla: G. V. Orlova, NI Rudakov, VG Lavrov, IS Elperin, IK Lagovsky i inni specjaliści NILD L. M. Belinsky, LI Pugachev, LSRoninson, SM Shifrin przeprowadzili prace eksperymentalne w OTsU w Charkowie Zakład Inżynierii Transportu. Tak wygląda sowiecki 4TPD. Był to sprawny silnik, ale z jedną wadą - moc wynosiła nieco ponad 400 KM, co nie wystarczało na czołg. Charomsky zakłada kolejny cylinder i otrzymuje 5TD.
Wprowadzenie dodatkowego cylindra poważnie zmieniło dynamikę silnika. Powstała nierównowaga, która spowodowała intensywne drgania skrętne w układzie. W jego rozwiązanie zaangażowane są wiodące siły naukowe Leningradu (VNII-100), Moskwy (NIID) i Charkowa (KhPI). 5TDF został doprowadzony do stanu EKSPERYMENTALNIE, metodą prób i błędów.
Wymiar tego silnika został wybrany równy 12/12, tj. taki sam jak w silniku U-305 i OTsU. Aby poprawić reakcję przepustnicy silnika wysokoprężnego, zdecydowano się mechanicznie połączyć turbinę i sprężarkę z wałem korbowym.
Diesel 5TD miał następujące cechy:
- duża moc - 426 kW (580 KM) przy stosunkowo niewielkich gabarytach;
- zwiększona prędkość - 3000 obr/min;
- efektywność sprężania i wykorzystania energii gazów odlotowych;
- niska wysokość (mniej niż 700 mm);
- zmniejszenie wymiany ciepła o 30-35% w porównaniu z istniejącymi czterosuwowymi (ssącymi) silnikami wysokoprężnymi, a co za tym idzie mniejsza objętość wymagana dla układu chłodzenia elektrowni;
- zadowalająca wydajność paliwowa i możliwość pracy silnika nie tylko na oleju napędowym, ale także na nafcie, benzynie i ich różnych mieszankach;
- przystawka odbioru mocy z obu jego końców i stosunkowo niewielka długość, co umożliwia montaż zbiornika MTO z poprzecznym układem silnika wysokoprężnego pomiędzy dwiema skrzyniami pokładowymi w znacznie mniejszej zajmowanej objętości niż przy układzie wzdłużnym silnik i centralna skrzynia biegów;
- udane umieszczenie takich jednostek jak wysokociśnieniowa sprężarka powietrza z własnymi systemami, rozrusznik-generator itp.
Zachowując poprzeczne ustawienie silnika z dwukierunkową przystawką odbioru mocy i dwiema planetarnymi przekładniami pokładowymi umieszczonymi po obu stronach silnika, konstruktorzy przesunęli się na wolne miejsca po bokach silnika, równolegle do skrzyń biegów, sprężarkę i turbinę gazową, wcześniej montowane w 4TD na szczycie bloku silnika. Nowy układ umożliwił zmniejszenie o połowę objętości MTO w porównaniu z czołgiem T-54 i wykluczono z niego takie tradycyjne elementy, jak centralna skrzynia biegów, skrzynia biegów, główne sprzęgło, pokładowe mechanizmy obrotu planetarnego, zwolnice i hamulce. Jak zauważono w dalszej części raportu GBTU, nowy typ przekładni zaoszczędził 750 kg masy i składał się ze 150 obrobionych części zamiast dotychczasowych 500.
Wszystkie systemy obsługi silnika zostały zablokowane nad silnikiem wysokoprężnym, tworząc „drugie piętro” MTO, którego schemat nazwano „dwupoziomowym”.
Wysoka wydajność silnika 5TD wymagała zastosowania w jego konstrukcji szeregu nowych podstawowych rozwiązań i specjalnych materiałów. Na przykład tłok tego diesla został wyprodukowany przy użyciu podkładki termicznej i przekładki.
Pierwszym pierścieniem tłokowym był ciągły pierścień płomieniowy typu wargowego. Cylindry wykonano ze stali, chromowano.
Możliwość pracy silnika przy wysokim ciśnieniu zapłonu zapewniał obwód zasilania silnika ze stalowymi śrubami wsporczymi, odlewany aluminiowy blok nieobciążony działaniem sił gazu oraz brak złącza gazowego. Usprawnienie procesu przedmuchiwania i napełniania cylindrów (a jest to problem we wszystkich 2-suwowych silnikach wysokoprężnych) ułatwił do pewnego stopnia schemat gazodynamiczny wykorzystujący energię kinetyczną spalin i efekt wyrzutu.
System formowania mieszanki jet-vortex, w którym charakter i kierunek strumieni paliwa jest skoordynowany z kierunkiem ruchu powietrza, zapewnił efektywną turbulizację mieszanki paliwowo-powietrznej, co przyczyniło się do usprawnienia procesu wymiany ciepła i masy.
Specjalnie dobrany kształt komory spalania umożliwił również usprawnienie procesu mieszania i spalania. Główne pokrywy łożysk zostały ściągnięte razem ze skrzynią korbową za pomocą stalowych śrub napędowych, przejmując obciążenie od sił gazu działających na tłok.
Do jednego końca bloku skrzyni korbowej zamocowano płytę z turbiną i pompą wody, a na przeciwległym płytę przekładni głównej i osłony z napędami do doładowania, regulatora, czujnika obrotomierza, sprężarki wysokiego ciśnienia i rozdzielacza powietrza kończyć się.
W styczniu 1957 roku przygotowano do testów na stanowisku pierwszy prototyp czołgowego silnika wysokoprężnego 5TD. Pod koniec testów na stanowisku 5TD w tym samym roku został przekazany do prób obiektowych (morskich) w eksperymentalnym czołgu „Obiekt 430”, a do maja 1958 przeszedł międzyresortowe testy państwowe z dobrą oceną.
Mimo to postanowiono nie przekazywać diesla 5TD do masowej produkcji. Powodem była ponownie zmiana wymagań wojska na nowe czołgi, co po raz kolejny wymagało zwiększenia mocy. Biorąc pod uwagę bardzo wysokie wskaźniki techniczne i ekonomiczne silnika 5TD i tkwiące w nim rezerwy (które również wykazały testy), nowa elektrownia o mocy około 700 KM. postanowiłem stworzyć na jego podstawie.
Stworzenie takiego oryginalnego silnika dla zakładu inżynierii transportu w Charkowie wymagało wyprodukowania znaczącego wyposażenia technologicznego, dużej liczby prototypów silnika wysokoprężnego i długotrwałych powtarzanych testów. Należy pamiętać, że dział konstrukcyjny zakładu stał się później Charkowskim Biurem Projektowym Inżynierii Mechanicznej (KHKBD), a produkcja silników powstała praktycznie od podstaw po wojnie.
Równolegle z projektem silnika wysokoprężnego powstał w zakładzie duży kompleks stanowisk doświadczalnych i różnych instalacji (24 jednostki) do testowania elementów jego konstrukcji i przebiegu pracy. To bardzo pomogło w sprawdzeniu i opracowaniu konstrukcji takich jednostek jak doładowanie, turbina, pompa paliwowa, kolektor wydechowy, wirówka, pompy wody i oleju, blokowa skrzynia korbowa itp. Jednak ich rozwój był kontynuowany.
W 1959 r. na prośbę głównego konstruktora nowego czołgu (AA Morozow), dla którego ten silnik wysokoprężny został zaprojektowany, uznano za konieczne zwiększenie jego mocy z 426 kW (580 KM) do 515 kW (700 KM). KM). Wymuszona wersja silnika została nazwana 5TDF.
Zwiększając prędkość sprężarki doładowania, zwiększono litrową moc silnika. Jednak w wyniku forsowania silnika wysokoprężnego pojawiły się nowe problemy, przede wszystkim w niezawodności podzespołów i zespołów.
Projektanci KhKBD, NIID, VNIITransmash, technolodzy zakładu i instytutów VNITI i TsNITI (od 1965) przeprowadzili ogromną ilość obliczeń, badań, prac projektowych i technologicznych, aby osiągnąć wymaganą niezawodność i czas pracy silnika wysokoprężnego 5TDF.
Najtrudniejszymi problemami okazały się problemy zwiększenia niezawodności grupy tłoków, osprzętu paliwowego i turbosprężarki. Każde, nawet nieznaczne, usprawnienie było wynikiem całego szeregu działań projektowych, technologicznych, organizacyjnych (produkcyjnych).
Pierwsza partia silników wysokoprężnych 5TDF charakteryzowała się dużą niestabilnością jakości części i zespołów. Pewna część silników wysokoprężnych z produkowanych serii (partia) ma przewidziany czas pracy gwarancyjnej (300 godzin). Jednocześnie znaczna część silników została usunięta ze stoisk przed upływem okresu eksploatacji z powodu pewnych usterek.
Specyfika wysokoobrotowego 2-suwowego silnika wysokoprężnego polega na bardziej złożonym układzie wymiany gazu niż w 4-suwowym, zwiększonym zużyciu powietrza i wyższym obciążeniu cieplnym grupy tłoków. W związku z tym sztywność i odporność konstrukcji na wibracje, ściślejsze przestrzeganie kształtu geometrycznego wielu części, wysokie właściwości przeciwzatarciowe i odporność na zużycie cylindrów, odporność cieplna i mechaniczna tłoków, staranne dozowanie i usuwanie smaru z cylindrów i wymagana była poprawa jakości powierzchni trących. Aby uwzględnić te specyficzne cechy silników dwusuwowych, konieczne było rozwiązanie złożonych problemów konstrukcyjnych i technologicznych.
Jednym z najbardziej krytycznych elementów zapewniających precyzyjną dystrybucję gazu i ochronę pierścieni uszczelniających tłok przed przegrzaniem był gwintowany stalowy cienkościenny pierścień płomieniowy typu mankietu ze specjalną powłoką przeciwcierną. W udoskonalaniu silnika wysokoprężnego 5TDF problem funkcjonalności tego pierścienia stał się jednym z głównych. W procesie dostrajania przez długi czas dochodziło do zacierania i pękania pierścieni płomieniowych na skutek deformacji ich płaszczyzny nośnej, nieoptymalnej konfiguracji zarówno samego pierścienia, jak i korpusu tłoka, niezadowalającego chromowania pierścieni, niewystarczającego smarowania, nierównomierny dopływ paliwa przez dysze, odpryskiwanie zgorzeliny i osadzanie się soli tworzących się na wyściółce tłoka, a także na skutek zużycia pyłu związanego z niewystarczającym stopniem oczyszczenia zasysanego przez silnik powietrza.
Dopiero w wyniku długiej i wytężonej pracy wielu specjalistów zakładu i instytutów naukowo-technicznych udoskonalono konfigurację tłoka i pierścienia płomieniowego, udoskonalono technologię wytwarzania, udoskonalono elementy wyposażenia paliwowego, poprawiono smarowanie, praktycznie wyeliminowano zastosowanie skuteczniejszych powłok przeciwciernych, a także udoskonalenie układu oczyszczania powietrza związane z pracą pierścienia płomieniowego.
Wyeliminowano np. awarie trapezowych pierścieni tłokowych poprzez zmniejszenie luzu osiowego między pierścieniem a rowkiem tłoka, poprawę materiału, zmianę konfiguracji przekroju pierścienia (przejście z trapezowego na prostokątny) oraz dopracowanie technologii do produkcji pierścieni. Pęknięcia śrub tulei tłokowej zostały naprawione poprzez ponowne nagwintowanie i zablokowanie, dokręcenie kontroli produkcyjnych, dokręcenie limitów momentu obrotowego i zastosowanie ulepszonego materiału śruby.
Stabilność zużycia oleju osiągnięto poprzez zwiększenie sztywności cylindrów, zmniejszenie rozmiaru wycięć na końcach cylindrów, kontrolę dokręcenia w produkcji pierścieni zbierających olej.
Dzięki dopracowaniu elementów wyposażenia paliwowego i poprawie wymiany gazowej uzyskano pewną poprawę efektywności paliwowej oraz zmniejszenie maksymalnego ciśnienia zapłonu.
Poprawiając jakość zastosowanej gumy i usprawniając szczelinę między cylindrem a blokiem wyeliminowano przypadki wycieku chłodziwa przez gumowe pierścienie uszczelniające.
W związku ze znacznym wzrostem przełożenia od wału korbowego do doładowania niektóre silniki wysokoprężne 5TDF ujawniły takie wady jak poślizg i zużycie tarcz sprzęgła ciernego, awarie koła doładowania oraz awarie jego łożysk, których nie było na Silnik wysokoprężny 5TD. Aby je wyeliminować konieczne było przeprowadzenie takich działań jak: dobór optymalnego dokręcenia pakietu tarcz ciernych, zwiększenie ilości tarcz w pakiecie, wyeliminowanie koncentratorów naprężeń w wirniku doładowania, drgania koła, zwiększenie właściwości tłumiących wsparcie i dobór lepszych łożysk. Umożliwiło to wyeliminowanie wad wynikających z forsowania silnika wysokoprężnego pod względem mocy.
Wzrost niezawodności i czasu pracy silnika wysokoprężnego 5TDF w dużej mierze przyczynił się do zastosowania olejów wyższej jakości ze specjalnymi dodatkami.
Na stoiskach VNIITransmash, przy udziale pracowników KKBD i NIID, przeprowadzono dużą ilość badań dotyczących pracy silnika wysokoprężnego 5TDF w warunkach rzeczywistego zapylenia powietrza dolotowego. Ostatecznie zakończyły się udanym testem „pyłowym” silnika przez 500 godzin pracy. Potwierdziło to wysoki stopień rozwoju grupy cylinder-tłok silnika wysokoprężnego i systemu oczyszczania powietrza.
Równolegle z dostrajaniem samego diesla był on wielokrotnie testowany w połączeniu z systemami elektrowni. Jednocześnie udoskonalano systemy, rozwiązywano kwestię ich wzajemnego połączenia i niezawodnej pracy w zbiorniku.
LL Golinets był głównym projektantem KHKBD w decydującym okresie dostrajania silnika wysokoprężnego 5TDF. Były główny projektant A. D. Charomsky przeszedł na emeryturę i nadal brał udział w dostrajaniu jako konsultant.
Rozwój seryjnej produkcji silnika wysokoprężnego 5TDF w nowych, specjalnie wybudowanych warsztatach zakładu, z nowymi kadrami pracowników i inżynierów, którzy studiowali na tym silniku, spowodował wiele trudności, udział specjalistów z innych organizacji.
Do 1965 roku silnik 5TDF był produkowany w oddzielnych seriach (partiach). Każda kolejna seria zawierała szereg środków opracowanych i przetestowanych na stoiskach, eliminujących wady stwierdzone podczas testów i podczas próbnej eksploatacji w wojsku.
Jednak rzeczywisty czas pracy silników nie przekroczył 100 godzin.
Znaczący przełom w poprawie niezawodności diesla nastąpił na początku 1965 roku. Do tego czasu dokonano wielu zmian w konstrukcji i technologii jego wytwarzania. Wprowadzone do produkcji zmiany umożliwiły wydłużenie czasu pracy kolejnych serii silników do 300 godzin. Wieloletnie testy eksploatacyjne zbiorników z silnikami tej serii potwierdziły znacznie zwiększoną niezawodność diesli: wszystkie silniki podczas tych testów przepracowały 300 godzin, a niektóre z nich (wybiórczo), kontynuując testy, przepracowały 400…500 godzin każdy.
W 1965 roku ostatecznie dopuszczono partię instalacyjną silników Diesla według poprawionej dokumentacji technicznej i technologii do produkcji seryjnej. W 1965 roku wyprodukowano łącznie 200 silników seryjnych. Rozpoczęło się zwiększanie produkcji, osiągając szczyt w 1980 roku. We wrześniu 1966 roku silnik wysokoprężny 5TDF przeszedł testy międzywydziałowe.
Biorąc pod uwagę historię powstania silnika wysokoprężnego 5TDF, należy odnotować postęp jego rozwoju technologicznego jako silnika zupełnie nowego do produkcji zakładu. Niemal równocześnie z produkcją prototypów silnika i dopracowaniem jego konstrukcji prowadzono jego rozwój technologiczny i budowę nowych obiektów produkcyjnych zakładu oraz ich wyposażenie w oprzyrządowanie.
Według zrewidowanych rysunków pierwszych próbek silników już w 1960 r. Rozpoczęto opracowywanie technologii projektowania do produkcji 5TDF, aw 1961 r. Rozpoczęto produkcję działającej dokumentacji technologicznej. Cechy konstrukcyjne dwusuwowego silnika wysokoprężnego, zastosowanie nowych materiałów, wysoka dokładność poszczególnych elementów i komponentów wymagały od technologii zastosowania całkowicie nowych metod przetwarzania, a nawet montażu silnika. Projektowanie procesów technologicznych i ich wyposażenia zostało wykonane zarówno przez służby technologiczne zakładu, kierowane przez A. I. Isaeva, V. D. Dyachenko, V. I. Doschechkina i innych, jak i przez pracowników instytutów technologicznych przemysłu. Specjaliści z Centralnego Instytutu Badawczego Materiałów (dyrektor F. A. Kupriyanov) byli zaangażowani w rozwiązywanie wielu problemów metalurgicznych i materiałoznawczych.
Budowa nowych warsztatów do produkcji silników Zakładu Inżynierii Transportu w Charkowie została przeprowadzona zgodnie z projektem Instytutu Soyuzmashproekt (główny inżynier projektu S. I. Shpynov).
W latach 1964-1967. nowa produkcja diesla została uzupełniona o sprzęt (zwłaszcza maszyny specjalne - ponad 100 sztuk), bez którego zorganizowanie seryjnej produkcji części diesla byłoby praktycznie niemożliwe. Były to wytaczarki diamentowe i wielowrzecionowe do obróbki bloków, specjalne tokarki i maszyny wykańczające do obróbki wałów korbowych itp. Przed uruchomieniem nowych warsztatów i obszarów testowych oraz debugowaniem technologii produkcji szeregu głównych części, a także produkcją partii montażowych i pierwszej serii silnika, tymczasowo zorganizowano przy produkcji kadłuby dużych lokomotyw spalinowych witryny.
Uruchamianie głównych mocy produkcyjnych nowej produkcji diesla odbywało się naprzemiennie w latach 1964-1967. W nowych warsztatach przewidziano pełny cykl produkcji oleju napędowego 5TDF, z wyjątkiem produkcji półfabrykatów zlokalizowanej na głównym terenie zakładu.
Przy tworzeniu nowych zakładów produkcyjnych dużą wagę przywiązywano do podnoszenia poziomu i organizacji produkcji. Produkcja silnika wysokoprężnego została zorganizowana według zasady linii i grupy, z uwzględnieniem najnowszych osiągnięć tego okresu w tej dziedzinie. Zastosowano najbardziej zaawansowane środki mechanizacji i automatyzacji obróbki i montażu części, co zapewniło stworzenie kompleksowo zmechanizowanej produkcji silnika wysokoprężnego 5TDF.
W procesie formowania produkcji przeprowadzono dużą wspólną pracę technologów i projektantów w celu poprawy produkcyjności konstrukcji silnika wysokoprężnego, podczas której technolodzy wystawili do KHKBD około sześciu tysięcy propozycji, z których znaczna część znalazła odzwierciedlenie w dokumentacja projektowa silnika.
Pod względem poziomu technicznego nowa produkcja oleju napędowego znacznie przekroczyła osiągane do tego czasu wskaźniki przedsiębiorstw branżowych, które produkowały podobne produkty. Współczynnik wyposażenia procesów produkcji diesla 5TDF osiągnął wysoką wartość - 6, 22. W ciągu zaledwie 3 lat opracowano ponad 10 tys. procesów technologicznych, zaprojektowano i wyprodukowano ponad 50 tys. Szereg przedsiębiorstw Charkowskiej Rady Gospodarczej było zaangażowanych w produkcję sprzętu i narzędzi, aby wspomóc fabrykę Małyszewa.
W kolejnych latach (po 1965 r.), już w toku seryjnej produkcji silnika wysokoprężnego 5TDF, służby technologiczne zakładu i TsNITI prowadziły prace nad dalszym doskonaleniem technologii w celu zmniejszenia pracochłonności, poprawy jakości i niezawodności silnik. Pracownicy TsNITI (dyrektor Ya. A. Shifrin, główny inżynier B. N. Surnin) w latach 1967-1970. opracowano ponad 4500 propozycji technologicznych, zapewniających zmniejszenie pracochłonności o ponad 530 standardowych godzin oraz znaczne ograniczenie strat ze złomu podczas produkcji. Jednocześnie działania te umożliwiły ponad połowę liczbę operacji dopasowania i selektywnego łączenia części. Efektem wdrożenia kompleksu środków konstrukcyjnych i technologicznych była bardziej niezawodna i wysokiej jakości praca silnika podczas pracy z gwarantowanym czasem pracy 300 godzin. Ale praca technologów zakładu i TsNITI wraz z projektantami KHKBD trwała nadal. Konieczne było zwiększenie czasu pracy silnika 5TDF o 1,5 … 2,0 razy. To zadanie również zostało rozwiązane. Dwusuwowy silnik wysokoprężny 5TDF został zmodyfikowany i wprowadzony do produkcji w Zakładzie Inżynierii Transportu w Charkowie.
Bardzo istotną rolę w organizacji produkcji diesla 5TDF odegrał dyrektor zakładu O. A. produkcji oleju napędowego, a także tych, którzy byli bezpośrednio zaangażowani w rozwiązywanie problemów technicznych i organizacyjnych.
Autonomiczne systemy ogrzewania pochodni i wtrysku oleju umożliwiły po raz pierwszy (w 1978 r.) zapewnienie zimnego rozruchu zbiornikowego silnika wysokoprężnego w temperaturach do -20 stopni C (od 1984 do -25 stopni C). Później (w 1985 r.) za pomocą systemu PVV (nagrzewnicy powietrza dolotowego) stało się możliwe przeprowadzenie zimnego rozruchu czterosuwowego silnika wysokoprężnego (V-84-1) na czołgach T-72, ale tylko do temperatura -20 stopni C, a nie więcej niż dwadzieścia uruchomień w ramach zasobu gwarancyjnego.
Co najważniejsze, 5TDF płynnie przeszło do nowej jakości w dieslach serii 6TD (6TD-1…6TD-4) o zakresie mocy 1000-1500 KM.i przewyższając zagraniczne analogi w wielu podstawowych parametrach.
INFORMACJE O PRACY SILNIKA
Zastosowane materiały operacyjne
Głównym rodzajem paliwa do zasilania silnika jest paliwo do szybkich silników wysokoprężnych GOST 4749-73:
w temperaturze otoczenia nie niższej niż + 5 ° С - marka DL;
w temperaturze otoczenia od +5 do -30 ° С - marki DZ;
w temperaturze otoczenia poniżej -30 ° С - marka DA.
W razie potrzeby dozwolone jest stosowanie paliwa DZ w temperaturze otoczenia powyżej + 50 ° C.
Oprócz paliwa do szybkich silników wysokoprężnych silnik może pracować na paliwie do silników odrzutowych TC-1 GOST 10227-62 lub benzynie silnikowej A-72 GOST 2084-67, a także na mieszankach paliw stosowanych w dowolnych proporcjach.
Olej M16-IHP-3 TU 001226-75 służy do smarowania silnika. W przypadku braku tego oleju dozwolone jest stosowanie oleju MT-16p.
Podczas wymiany z jednego oleju na inny olej resztkowy ze skrzyni korbowej silnika i zbiornika oleju maszyny musi zostać spuszczony.
Zabronione jest mieszanie stosowanych ze sobą olejów, a także stosowanie olejów innych marek. Dopuszcza się mieszanie w układzie olejowym niespływających pozostałości jednego gatunku oleju z innym, ponownie napełnionym.
Podczas spuszczania temperatura oleju nie może być niższa niż + 40 ° C.
Do chłodzenia silnika w temperaturze otoczenia co najmniej + 5 ° C stosuje się czystą świeżą wodę bez zanieczyszczeń mechanicznych, przepuszczaną przez specjalny filtr dostarczany do EC maszyny.
Aby chronić silnik przed korozją i tworzeniem acipe, do wody przepuszczanej przez filtr dodaje się 0,15% trójskładnikowego dodatku (0,05% każdego składnika).
Dodatek składa się z fosforanu trisodowego GOST 201-58, piku chromowo-potasowego GOST 2652-71 i azotynu sodu GOST 6194-69 należy najpierw rozpuścić w 5-6 litrach wody przepuszczonej przez filtr chemiczny i podgrzany do temperatury 60-80 °C. W przypadku tankowania 2-3 litrów dopuszcza się (jednorazowo) użycie wody bez dodatków.
Nie wlewać dodatku antykorozyjnego bezpośrednio do systemu.
W przypadku braku dodatku trójskładnikowego dozwolone jest stosowanie piku czystego chromu 0,5%.
W temperaturze otoczenia poniżej + 50 ° C należy stosować płyn niskozamarzający (przeciw zamarzaniu) „40” lub „65” GOST 159-52. Marka niezamarzająca „40” jest stosowana w temperaturach otoczenia do -35 ° C, w temperaturach poniżej -35 ° C - marka niezamarzająca „65”.
Napełnij silnik paliwem, olejem i płynem chłodzącym zgodnie ze środkami zapobiegającymi przedostawaniu się zanieczyszczeń mechanicznych i pyłu oraz wilgoci do paliwa i oleju.
Zaleca się tankowanie za pomocą specjalnych cystern lub zwykłego urządzenia do tankowania (przy tankowaniu z oddzielnych zbiorników).
Paliwo należy uzupełniać przez jedwabny filtr. Zaleca się wlewanie oleju za pomocą specjalnych wlewów olejowych. Napełnij olej, wodę i płyn o niskiej temperaturze zamarzania przez filtr z siatką nr 0224 GOST 6613-53.
Napełnić systemy do poziomów określonych w instrukcji obsługi maszyny.
Aby całkowicie wypełnić objętości układów smarowania i chłodzenia, po zatankowaniu uruchom silnik na 1-2 minuty, następnie sprawdź poziomy i, jeśli to konieczne, zatankuj układy, Podczas pracy należy kontrolować ilość płynu chłodzącego i oleju w układach silnika i utrzymywać ich poziomy IB w określonych granicach.
Nie pozwól, aby silnik pracował, jeśli w zbiorniku smarowania silnika znajduje się mniej niż 20 litrów oleju.
Jeśli poziom płynu chłodzącego spadnie z powodu parowania lub wycieku do układu chłodzenia, należy odpowiednio dodać wodę lub płyn niezamarzający.
Spuść płyn chłodzący i olej przez specjalne zawory spustowe silnika i maszyny (kocioł grzewczy i zbiornik oleju) za pomocą węża z złączką z otwartymi otworami wlewu. Aby całkowicie usunąć pozostałą wodę z układu chłodzenia, aby uniknąć jej zamarzania, zaleca się zalanie układu 5-6 litrami płynu niskozamarzającego.
Cechy pracy silnika na różnych rodzajach paliwa
Praca silnika na różnych rodzajach paliwa odbywa się za pomocą mechanizmu sterowania podawaniem paliwa, który ma dwa położenia do ustawienia dźwigni wielopaliwowej: praca na paliwie do szybkich silników wysokoprężnych, paliwo do silników odrzutowych, benzyna (ze spadkiem mocy) i ich mieszaniny w dowolnych proporcjach; pracuj tylko na benzynie.
Praca na innych rodzajach paliwa przy takim położeniu dźwigni jest surowo zabroniona.
Montaż mechanizmu sterującego podawaniem paliwa z pozycji „Praca na oleju napędowym” do pozycji „Praca na benzynie” odbywa się poprzez przekręcenie śruby regulacyjnej dźwigni wielopaliwowej zgodnie z ruchem wskazówek zegara do oporu, a z pozycji „Praca wł. benzyna” do pozycji „Praca na oleju napędowym” - przekręcając śrubę regulacyjną dźwigni wielopaliwowej w kierunku przeciwnym do ruchu wskazówek zegara, aż się zatrzyma.
Funkcje uruchamiania i obsługi silnika podczas pracy na benzynie. Co najmniej 2 minuty przed uruchomieniem silnika należy włączyć pompę BCN maszyny i intensywnie pompować paliwo ręczną pompką zalewową maszyny; we wszystkich przypadkach, niezależnie od temperatury otoczenia, przed uruchomieniem należy dwukrotnie wstrzyknąć olej do cylindrów.
Benzynowa pompa odśrodkowa maszyny musi być włączona przez cały czas pracy silnika na benzynie, jej mieszankach z innymi paliwami oraz podczas krótkich postojów (3-5 minut) maszyny.
Minimalna stała prędkość biegu jałowego, gdy silnik pracuje na benzynie, wynosi 1000 na minutę.
CECHY DZIAŁANIA
S. Suworow wspomina zalety i wady tego silnika w swojej książce „T-64”.
W czołgach T-64A produkowanych od 1975 roku wzmocniono również pancerz wieży dzięki zastosowaniu wypełniacza korundowego.
W tych maszynach zwiększono również pojemność zbiorników paliwa z 1093 litrów do 1270 litrów, w wyniku czego z tyłu wieży pojawiło się pudełko do przechowywania części zamiennych. W maszynach poprzednich wersji części zamienne i akcesoria były umieszczane w skrzynkach na prawym błotniku, gdzie zainstalowano dodatkowe zbiorniki paliwa, połączone z układem paliwowym. Gdy kierowca montował zawór dystrybucji paliwa na dowolnej grupie zbiorników (tylnej lub przedniej), paliwo było produkowane głównie ze zbiorników zewnętrznych.
W mechanizmie napinania gąsienic zastosowano parę ślimakową, co pozwoliło na jego eksploatację bez konserwacji przez cały okres eksploatacji zbiornika.
Charakterystyki wydajności tych maszyn zostały znacznie ulepszone. Na przykład próba przed kolejnym serwisem numeru została zwiększona z 1500 i 3000 km do 2500 i 5000 km odpowiednio dla T01 i TO. Dla porównania, na czołgu T-62 TO1 TO2 przeprowadzono po 1000 i 2000 km przebiegu, a na czołgu T-72 - odpowiednio po 1600-1800 i 3300-3500 km przebiegu. Okres gwarancji na silnik 5TDF został wydłużony z 250 do 500 godzin, okres gwarancji na całą maszynę wyniósł 5000 km.
Ale szkoła to tylko preludium, główna operacja zaczęła się w wojsku, gdzie trafiłem po ukończeniu studiów w 1978 roku. Tuż przed maturą poinformowano nas o rozkazie Naczelnego Dowódcy Wojsk Lądowych, aby absolwenci naszej szkoły byli rozprowadzani tylko do tych formacji, w których znajdują się czołgi T-64. Wynikało to z faktu, że w oddziałach dochodziło do masowych awarii czołgów T-64, w szczególności silników 5TDF. Powód - nieznajomość materiału i zasad działania tych zbiorników. Przyjęcie czołgu T-64 było porównywalne z przejściem w lotnictwie z silników tłokowych na silniki odrzutowe - weterani lotnictwa pamiętają, jak to było.
Jeśli chodzi o silnik 5TDF, były dwie główne przyczyny jego awarii w wojsku - przegrzanie i zużycie pyłu. Oba powody wynikały z nieznajomości lub zaniedbania zasad działania. Główną wadą tego silnika jest to, że nie jest on zbyt zaprojektowany dla głupców, czasami wymaga, aby robili to, co jest napisane w instrukcji obsługi. Kiedy byłem już dowódcą kompanii czołgów, jeden z dowódców moich plutonów, absolwent Czelabińskiej Szkoły Pancernej, która szkoliła oficerów do czołgów T-72, zaczął jakoś krytykować elektrownię czołgu T-64. Nie podobał mu się silnik i częstotliwość jego konserwacji. Ale kiedy zadano mu pytanie „Ile razy w ciągu sześciu miesięcy otwierałeś dachy MTO na swoich trzech czołgach treningowych i zaglądałeś do przedziału silnik-przekładnia?” Okazało się, że nigdy. A czołgi poszły, zapewniły szkolenie bojowe.
I tak dalej w kolejności. Przegrzanie silnika nastąpiło z kilku powodów. Najpierw mechanik zapomniał zdjąć matę z chłodnicy, a potem nie patrzył na przyrządy, ale zdarzało się to bardzo rzadko i z reguły zimą. Drugim i głównym jest wypełnienie płynem chłodzącym. Zgodnie z instrukcją ma on napełniać wodę (w okresie letnim eksploatacji) dodatkiem trójskładnikowym, a wodę należy napełniać przez specjalny sulfofiltr, w który były wyposażone wszystkie maszyny przedwczesnego uwalniania, a na nowych maszyn jeden taki filtr został wydany na firmę (10-13 czołgów). Uszkodziły się silniki, głównie czołgów z grupy szkoleniowej, które były eksploatowane co najmniej pięć dni w tygodniu i zwykle znajdują się na strzelnicach w parkach polowych. Jednocześnie „podręczniki” mechanika-kierowcy (tzw. mechanika maszyn treningowych), z reguły ciężko pracowici i sumienni faceci, ale nie znający zawiłości silnika, mogli sobie czasem pozwolić na wlanie wody do układ chłodzenia tylko z kranu, zwłaszcza że sulfofiltr (czyli jeden na kompanię) był zwykle trzymany w kwaterach zimowych, gdzieś w szafce szefa technicznego firmy. Skutkiem tego jest tworzenie się kamienia w cienkich kanałach układu chłodzenia (w rejonie komór spalania), brak cyrkulacji cieczy w najgorętszej części silnika, przegrzewanie i awaria silnika. Tworzenie się kamienia pogarszał fakt, że woda w Niemczech jest bardzo twarda.
W sąsiedniej jednostce silnik został usunięty z powodu przegrzania z winy kierowcy. Po znalezieniu niewielkiego wycieku płynu chłodzącego z chłodnicy, za radą jednego z „ekspertów”, aby dodać musztardę do systemu, kupił w sklepie paczkę musztardy i wlał ją do systemu, w wyniku czego - zatkanie kanałów i awarii silnika.
Były też inne niespodzianki związane z systemem chłodzenia. Nagle zaczyna usuwać płyn chłodzący z układu chłodzenia przez zawór parowo-powietrzny (PVK). Niektórzy, nie rozumiejąc o co chodzi, próbują uruchomić go z holownika - efekt zniszczenia silnika. Tak więc zastępca szefa mojego batalionu zrobił mi „prezent” na Nowy Rok i 31 grudnia musiałem wymienić silnik. Miałem czas przed Nowym Rokiem, bo wymiana silnika na czołgu T-64 nie jest bardzo skomplikowaną procedurą i, co najważniejsze, nie wymaga osiowania podczas montażu. W większości przypadków wymiana silnika w zbiorniku T-64, podobnie jak we wszystkich zbiornikach domowych, odbywa się poprzez procedurę spuszczania i uzupełniania oleju i płynu chłodzącego. Gdyby nasze czołgi miały złącza z zaworami zamiast połączeń durit, jak w Leopardach lub Leclercs, to wymiana silnika w czołgach T-64 lub T-80 na czas zajęłaby tylko wymianę całego zespołu napędowego w czołgach zachodnich. Na przykład tego pamiętnego dnia, 31 grudnia 1980 roku, po spuszczeniu oleju i płynu chłodzącego, chorąży E. Sokolov i ja „wyrzuciliśmy” silnik z MTO w zaledwie 15 minut.
Drugim powodem awarii silników 5TDF jest zużycie pyłu. System oczyszczania powietrza. Jeśli nie sprawdzisz poziomu chłodziwa w odpowiednim czasie, ale należy go sprawdzać przed każdym wyjściem z maszyny, to może nadejść moment, w którym w górnej części płaszcza chłodzącego nie będzie cieczy i nastąpi miejscowe przegrzanie. W tym przypadku najsłabszym punktem jest dysza. W takim przypadku spalają się uszczelki wtryskiwacza lub sam wtryskiwacz ulega awarii, wtedy przez pęknięcia w nim lub spalone uszczelki do układu chłodzenia przedostają się gazy z cylindrów i pod ich ciśnieniem ciecz jest wypychana przez PVCL. Wszystko to nie jest śmiertelne dla silnika i jest eliminowane, jeśli w jednostce znajduje się kompetentna osoba. W konwencjonalnych silnikach rzędowych i w kształcie litery V w podobnej sytuacji „prowadzi” uszczelkę głowicy cylindrów iw tym przypadku będzie więcej pracy.
Jeśli w takiej sytuacji silnik zostanie zatrzymany i nie zostaną podjęte żadne środki, to po chwili cylindry zaczną napełniać się płynem chłodzącym, silnik to ruszt bezwładnościowy i cyklonowy filtr powietrza. Filtr powietrza, zgodnie z instrukcją obsługi, jest płukany w razie potrzeby. Na czołgach typu T-62 myto go zimą po 1000 km, a latem po 500 km. Na czołgu T-64 - w razie potrzeby. I tu pojawia się przeszkoda - niektórzy przyjęli to jako fakt, że w ogóle nie trzeba jej myć. Potrzeba pojawiła się, gdy olej dostał się do cyklonów. A jeśli przynajmniej jeden ze 144 cyklonów zawiera olej, to filtr powietrza należy przepłukać, ponieważ przez ten cyklon nieoczyszczone powietrze z kurzem dostaje się do silnika, a następnie, jak szmergiel, tuleje cylindrowe i pierścienie tłokowe są ścierane. Silnik zaczyna tracić moc, wzrasta zużycie oleju, a następnie całkowicie przestaje się uruchamiać.
Sprawdzenie wnikania oleju do cyklonów nie jest trudne - wystarczy spojrzeć na wloty cyklonów na filtrze powietrza. Zwykle patrzyli na rurę odprowadzającą kurz z oczyszczacza powietrza, a jeśli znalazł się na niej olej, to patrzyli na oczyszczacz powietrza i w razie potrzeby myli go. Skąd wziął się olej? To proste: szyjka wlewu zbiornika oleju układu smarowania silnika znajduje się obok siatki wlotu powietrza. Podczas tankowania oleju zwykle używa się konewki, ale ponieważ znowu na maszynach treningowych z reguły nie było konewek (ktoś zgubił, ktoś położył go na pasie gąsienicowym, zapomniał i przejechał przez niego itp.), potem mechanicy po prostu wylali olej z wiader, podczas gdy olej się rozlał, najpierw spadła na siatkę wlotu powietrza, a następnie do filtra powietrza. Nawet podczas napełniania olejem przez konewkę, ale przy wietrznej pogodzie, wiatr rozpryskiwał olej na siatce filtra powietrza. Dlatego tankując olej zażądałem od moich podwładnych, aby na siatkę wlotu powietrza założyć matę z części zamiennych i osprzętu zbiornika, dzięki czemu uniknęłam kłopotów z pyłowym zużyciem silnika. Należy zauważyć, że najbardziej zakurzone warunki panujące w Niemczech w okresie letnim były najcięższe. Tak więc na przykład podczas ćwiczeń dywizyjnych w sierpniu 1982 r., gdy maszerował przez polany leśne Niemiec, z powodu wiszącego kurzu nie było nawet widać, gdzie kończy się lufa działa własnego czołgu. Odległość między samochodami w kolumnie była utrzymywana dosłownie zapachem. Kiedy do czołowego czołgu zostało dosłownie kilka metrów, można było wyczuć zapach jego spalin i zahamować na czas. A więc 150 kilometrów. Po marszu wszystko: czołgi, ludzie i ich twarze, kombinezony i buty były tego samego koloru - koloru kurzu drogowego.
Olej napędowy 6TD
Równolegle z projektowaniem i udoskonalaniem technologicznym silnika wysokoprężnego 5TDF, zespół projektowy KKBD rozpoczął prace nad kolejnym modelem 2-suwowego silnika wysokoprężnego już w wersji 6-cylindrowej o zwiększonej mocy do 735 kW (1000 KM). Ten silnik, podobnie jak 5TDF, był silnikiem wysokoprężnym z poziomo ułożonymi cylindrami, przeciwbieżnymi tłokami i bezpośrednim nadmuchem. Diesel został nazwany 6TD.
Turbodoładowanie odbywało się ze sprężarki mechanicznie (sprężyny) połączonej z turbiną gazową, zamieniając część energii cieplnej spalin na pracę mechaniczną napędzającą sprężarkę.
Ponieważ moc wytwarzana przez turbinę nie wystarczała do napędzania sprężarki, połączono ją z obydwoma wałami korbowymi silnika za pomocą skrzyni biegów i mechanizmu przekładni. Przyjęto, że stopień kompresji wynosił 15.
Aby uzyskać wymagany rozrząd, przy którym zapewnione byłoby niezbędne oczyszczenie cylindra ze spalin i wypełnienie sprężonym powietrzem, przewidziano kątowe przemieszczenie wałów korbowych (jak w silnikach 5TDF) w połączeniu z asymetrycznym rozmieszczeniem wlotu oraz otwory wylotowe cylindrów wzdłuż ich długości. Moment pobierany z wałów korbowych wynosi 30% dla wału ssącego i 70% dla momentu wydechowego silnika. Moment obrotowy wytworzony na wale ssącym był przenoszony przez przekładnię zębatą na wał wydechowy. Całkowity moment obrotowy można było przejąć z obu końców wału wydechowego przez sprzęgło odbioru mocy.
W październiku 1979 roku silnik 6TD, po poważnej rewizji grupy cylindrowo-tłokowej, wyposażenia paliwowego, układu zasilania powietrzem i innych elementów, pomyślnie przeszedł testy międzywydziałowe. Od 1986 roku wyprodukowano pierwsze silniki serii 55. W kolejnych latach produkcja seryjna rosła i osiągnęła szczyt w 1989 roku.
Odsetek jednostkowej unifikacji 6TD z silnikiem wysokoprężnym 5TDF wyniósł ponad 76%, a niezawodność działania nie mniejsza niż w przypadku seryjnego od wielu lat 5TDF.
Kontynuowano prace KHKBD pod kierownictwem głównego projektanta N. K. Ryazantseva w celu dalszej poprawy 2-suwowego silnika wysokoprężnego. Finalizowano jednostki, mechanizmy i systemy, według których identyfikowano poszczególne usterki w eksploatacji. Poprawiono system ciśnieniowy. Przeprowadzono liczne testy stanowiskowe silników wraz z wprowadzeniem zmian konstrukcyjnych.
Opracowywana była nowa modyfikacja silnika wysokoprężnego 6TD-2. Jego moc nie wynosiła już 735 kW (1000 KM), jak w 6TD, ale 882 kW (1200 KM). Jego szczegółową unifikację z silnikiem wysokoprężnym 6TD zapewniło ponad 90%, a z silnikiem wysokoprężnym 5TDF - ponad 69%.
W przeciwieństwie do silnika 6TD, silnik 6TD-2 wykorzystywał dwustopniową, osiową sprężarkę odśrodkową układu ciśnieniowego i zmiany w konstrukcji turbiny, mieszków, odśrodkowego filtra oleju, rury rozgałęźnej i innych zespołów. Nieznacznie obniżono również stopień sprężania - z 15 do 14,5 oraz zwiększono średnie ciśnienie efektywne z 0,98 MPa do 1,27 MPa. Jednostkowe zużycie paliwa silnika 6TD-2 wynosiło 220 g/(kW*h) (162 g/(KM*h)) zamiast 215 g/(kW*h) (158 g/(KM*H)) - dla 6TD. Z punktu widzenia montażu w zbiorniku silnik wysokoprężny 6TD-2 był całkowicie zamienny z silnikiem 6DT.
W 1985 roku Diesel 6TD-2 przeszedł testy międzywydziałowe i dostarczono dokumentację projektową do przygotowania i organizacji produkcji seryjnej.
W KKBD, przy udziale NIID i innych organizacji, kontynuowano prace badawczo-rozwojowe nad 2-suwowym silnikiem wysokoprężnym 6TD w celu zwiększenia jego mocy do 1103 kW (1500 KM), 1176 kW (1600 KM), 1323 kW (1800 KM). z testowaniem na próbkach, a także stworzeniem na jej podstawie rodziny silników do maszyn VGM i gospodarki narodowej. Dla VGM lekkiej i średniej kategorii wagowej opracowano silniki wysokoprężne 3TD o mocy 184 … 235 kW (250-320 KM), 4TD o mocy 294 … 331 kW (400 … 450 KM). Opracowano również wariant silnika wysokoprężnego 5DN o mocy 331…367 kW (450-500 KM) do pojazdów kołowych. Dla transporterów ciągników i pojazdów inżynieryjnych opracowano projekt silnika wysokoprężnego 6DN o mocy 441…515 kW (600-700 KM).
Olej napędowy 3TD
Silniki ZTD o konstrukcji trzycylindrowej należą do jednej zunifikowanej serii z silnikami seryjnymi 5TDF, 6TD-1 i 6TD-2E. Na początku lat 60. w Charkowie stworzono rodzinę silników opartych na 5TDF dla pojazdów lekkich (transportery opancerzone, bojowe wozy piechoty itp.) i kategorii ciężkiej (czołgi, 5TDF, 6TD).
Te silniki mają jeden schemat konstrukcyjny:
- cykl dwusuwowy;
- poziomy układ cylindrów;
- wysoka zwartość;
- niski transfer ciepła;
- możliwość stosowania w temperaturach otoczenia
środowiska od minus 50 do plus 55 ° С;
- niska moc obniżania wartości znamionowych w wysokich temperaturach
środowisko;
- wielopaliwowe.
Oprócz obiektywnych przyczyn popełniono błędy przy tworzeniu rodziny dwusuwowych bokserów 3TD w połowie lat 60-tych. Pomysł na silnik 3-cylindrowy został przetestowany w oparciu o silnik 5-cylindrowy, w którym wytłumiono dwa cylindry. Jednocześnie ścieżka powietrze-gaz i jednostki ciśnieniowe nie były skoordynowane. Naturalnie zwiększono również moc strat mechanicznych.
Główną przeszkodą w stworzeniu zunifikowanej rodziny silników w latach 60. i 70. był brak jasnego programu rozwoju budowy silników w kraju, przywództwo polegało na „przerzucaniu” różnych koncepcji silników wysokoprężnych i silników z turbiną gazową. W latach 70., kiedy Leonid Breżniew objął kierownictwo kraju, sytuacja jeszcze się pogorszyła, równoległa produkcja czołgów z różnymi silnikami - T-72 i T-80, które ze względu na swoje cechy były „analogowymi czołgami” już wyprodukowany T-64. Nie było już mowy o unifikacji silników czołgu, bojowych wozów piechoty i transporterów opancerzonych.
Niestety, taka sama sytuacja miała miejsce w innych oddziałach kompleksu wojskowo-przemysłowego - w tym samym czasie powstawały różne biura projektowe w dziedzinie rakietowej, budowy samolotów, przy czym wśród nich nie wybierano najlepszych, ale podobne produkty z różnych Biur Projektowych (Biuro projektowe) były produkowane równolegle.
Taka polityka była początkiem końca gospodarki krajowej i przyczyną opóźnienia w budowie czołgów, zamiast zjednoczenia w „jedną pięść”, wysiłki zostały rozproszone na równoległym rozwoju konkurencyjnych biur projektowych.
Pojazdy lekkie (LME), produkowane w latach 60….80. ubiegłego wieku, mają silniki o przestarzałej konstrukcji, zapewniające gęstość mocy w zakresie 16-20 KM/t. Nowoczesne maszyny powinny mieć określoną moc 25-28 KM/t, co zwiększy ich zwrotność.
W latach 90. i 2000. istotna stała się modernizacja LME - BTR-70, BTR-50, BMP-2.
W tym okresie przeprowadzono testy tych maszyn, które wykazały wysokie parametry nowego silnika, ale jednocześnie duża liczba silników UTD-20S1 była przechowywana i produkowana na terenie Ukrainy po upadku ZSRR.
Generalny projektant budowy czołgów Ukrainy M. D. Borisyuk (KMDB) zdecydował się wykorzystać istniejące seryjne silniki - SMD-21 UTD-20 i niemiecki "Deutz" do modernizacji tych maszyn.
Każdy pojazd miał własne silniki, które nie były ze sobą zunifikowane iz silnikami już w wojsku. Powodem jest to, że zakładom naprawczym MON opłaca się korzystać z silników dostępnych w magazynach klienta, co obniża koszty pracy.
Ale to stanowisko pozbawione pracy Przedsiębiorstwa Państwowego „Zakład im. V. A. Malysheva”, a przede wszystkim kruszywa.
Stanowisko to okazało się niejednoznaczne - z jednej strony oszczędności, z drugiej utrata perspektywy.
Warto zauważyć, że w KMDB w odniesieniu do 3TD zgłoszono szereg roszczeń (za hałas i dym), które zostały zaakceptowane i wyeliminowane.
W celu zmniejszenia zadymienia podczas rozruchu i w stanach przejściowych, w silniku ZTD zainstalowano zamknięty osprzęt paliwowy i znacznie zmniejszono zużycie oleju. Redukcję hałasu zapewnia zmniejszenie maksymalnego ciśnienia spalania oraz zmniejszenie luzu w parze tłok-cylinder w silnikach o mocy 280 i 400 KM, a także zmniejszenie zakresu drgań skrętnych
Zmniejszenie zużycia oleju w silnikach ZTD osiągnięto dzięki następującym czynnikom:
- zmniejszenie liczby cylindrów;
- zastosowanie tłoka z korpusem żeliwnym zamiast stopu aluminium;
- zwiększenie ciśnienia właściwego pierścienia zgarniającego olej o
ściana cylindra.
W wyniku podjętych działań względne zużycie oleju na silnikach ZTD zbliża się do zużycia na silnikach dla celów gospodarki narodowej.