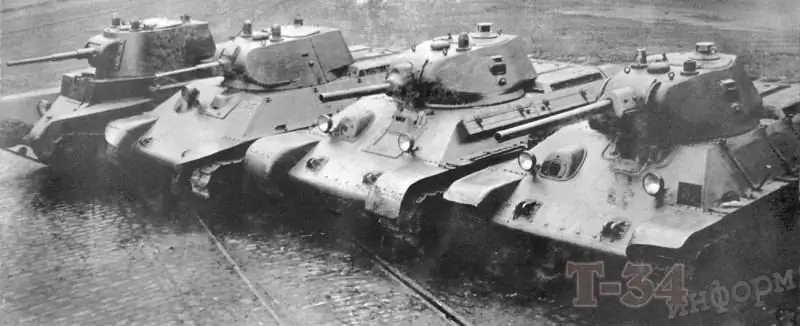
Czekam na wojnę
Problemy z produkcją czołgów w Związku Radzieckim w latach 20. i 30. XX wieku, związane przede wszystkim z niedostępnością przemysłu, były częściowo wyjaśniane zapóźnieniem przemysłu pancernego. Na początku 1932 r. tylko dwa z planowanych czterech przedsiębiorstw mogły wytapiać i toczyć zbroję. Były to fabryki Izhora i Mariupol. Ze względu na zbyt wysokie wymagania dotyczące szybkości produkcji (był to znak tamtych czasów), fabryki te chronicznie pozostawały w tyle. Tak więc w jednym z najstarszych przedsiębiorstw w kraju, zakładzie Izhora w mieście Kolpino, w ciągu roku byli w stanie opanować tylko 38% planu, aw Mariupolu w zakładzie Iljicza - tylko jedna czwarta. Wynikało to w dużej mierze z produkcji złożonej, cementowanej, heterogenicznej zbroi, którą w naszym kraju wiedzieli od 1910 roku. Podobny rodzaj zbroi był wymagany, aby wytrzymać ostre pociski i pociski, których nie zapewniała zwykła jednorodna średnia i niska twardość. W tym czasie pancerze cementowe dzieliły się na dwa gatunki: niskotemperaturowy jednostronnie cementowany z dostatecznie twardą tylną stroną oraz, w drugiej wersji, ze średnio twardą tylną stroną. Zasadniczo do produkcji takich „kanapek” potrzebna była stal chromowo-molibdenowa i chromowo-niklowo-molibdenowa, co wymagało ubogich importowanych dodatków żelazostopowych. Głównym składnikiem stopowym tych stali był chrom (1, 5-2, 5%), który sprzyja intensywnemu nawęglaniu i uzyskaniu wysokiej twardości warstwy spoiwa po hartowaniu. Próba zastosowania krajowego manganu i krzemu do stali nawęglanej zamiast importowanego chromu dała wynik negatywny. W stanie stopowym z manganem okazało się, że stal ma skłonność do rozrostu ziarna w temperaturze nawęglania (920-950 stopni Celsjusza), zwłaszcza przy długich ekspozycjach wymaganych do nawęglania na dużej głębokości. Korekta warstwy nawęglonej przegrzanej podczas cementowania stwarzała znaczne trudności i wiązała się z koniecznością zastosowania wielokrotnej rekrystalizacji, co powodowało znaczne odwęglenie warstwy nawęglonej i doprowadzeń blach, a także było nieopłacalne ekonomicznie. Niemniej jednak, aż do wczesnych lat 30-tych, pancerz cementowany był używany zarówno w lotnictwie, jak i przy budowie czołgów. W samolotach cementowano płyty pancerne o grubości do 13 mm, podobnie jak pancerz czołgów do 30 mm. Były również prace nad kuloodpornym, cementowym pancerzem 20 mm, który nie wykraczał poza eksperymentalny rozwój. Taka zbroja zdecydowanie musiała być masywna, co wymagało tylko gigantycznych środków na rozwój produkcji.
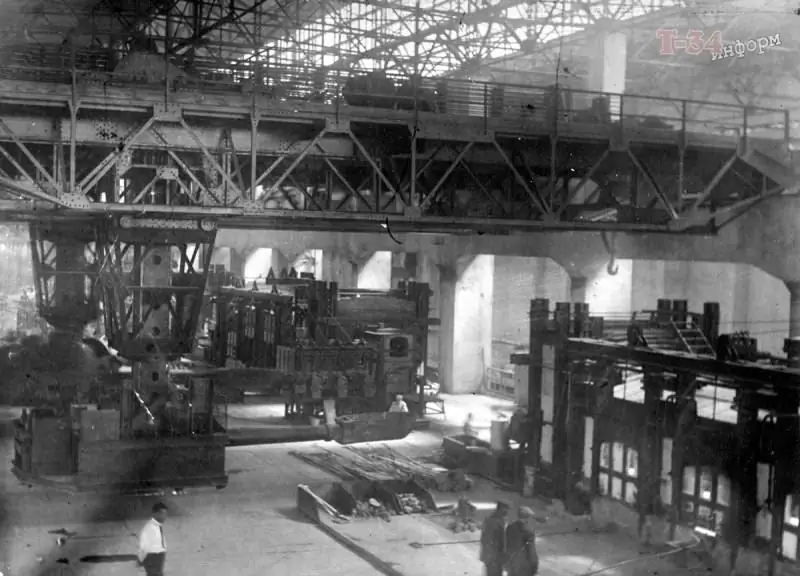
Pomimo takich trudności z produkcją opancerzenia cementowego, kadłub czołgu T-28 został z niego wykonany prawie w całości. Ale stopniowo krajowy przemysł porzucił technologie cementowania płyt pancernych, głównie ze względu na wyjątkowo duże odrzuty. Biorąc pod uwagę plany produkcyjne wymagane przez rząd i wyspecjalizowane komisariaty ludowe, nie było to wcale zaskakujące. Fabryka Izhora jako pierwsza przeszła na nową zbroję, po opanowaniu wytapiania bardzo twardego zbroi chromowo-krzemowo-manganowej „PI”. W Mariupolu opanowali niejednorodny mangan „MI”. Kraj stopniowo przestawił się na własne doświadczenie w projektowaniu zbroi. Do tego czasu opierał się na technologiach zagranicznych (głównie brytyjskich). Odmowa zacementowania pancerza spowodowała pogrubienie blach przy tej samej odporności pancerza. Tak więc, zamiast 10 i 13-milimetrowego pancerza cementowego, kadłub T-26 musiał być spawany z 15-milimetrowych blach ze stali Izhora „PI”. W tym przypadku czołg miał masę 800 kilogramów. Należy zauważyć, że przejście od drogiej stali cementowanej do stosunkowo tanich technologii jednorodnego pancerza okazało się bardzo przydatne w czasie wojny. Gdyby tak nie było w latach przedwojennych, rozwój wytapiania i walcowania drogich rodzajów zbroi byłby mało prawdopodobny, biorąc pod uwagę ewakuację przedsiębiorstw w latach 1941-1942.
Od lat przedwojennych główną rolę w poszukiwaniach i badaniach nowych rodzajów zbroi odgrywał „Instytut Zbroi” TsNII-48, który obecnie znany jest jako NRC „Instytut Kurczatowa” - TsNII KM „Prometeusz”. Zespół inżynierów i naukowców TsNII-48 wyznaczył główne kierunki krajowego przemysłu zbrojeniowego. W ostatniej dekadzie przed wojną pojawienie się za granicą artylerii przeciwpancernej kalibru od 20 do 50 mm stało się poważnym wyzwaniem. To zmusiło deweloperów do poszukiwania nowych przepisów na zbroję do gotowania.
Narodziny 8C
Wymień opancerzenie cementowe odporne na ostre pociski i pociski w lekko i średnio opancerzonych pojazdach tylko na stal o wysokiej twardości. I to z powodzeniem opanowali krajowi metalurdzy. Kadłuby pojazdów opancerzonych BA-10, czołgi lekkie T-60 (grubość pancerza 15 mm, czołowa 35 mm), T-26 (grubość pancerza 15 mm) i oczywiście czołgi średnie T-34 (grubość pancerza 45 mm). Niemcy mieli również priorytetowe opancerzenie o wysokiej twardości. W rzeczywistości wszystkie opancerzenie (od hełmów piechoty, a skończywszy na lotniczych konstrukcjach ochronnych) w końcu zyskało wysoką twardość, zastępując cementowany. Być może tylko ciężkie KV mogły sobie pozwolić na pancerz o średniej twardości, ale trzeba było za to zapłacić większą grubością blach i końcową masą czołgu.
Stal pancerna 8C, podstawa obrony przeciwdziałowej czołgu T-34, stała się prawdziwą koroną kreatywności krajowych metalurgów. Należy zauważyć, że produkcja zbroi 8C w latach przedwojennych i podczas Wielkiej Wojny Ojczyźnianej to dwa poważnie różne procesy. Nawet dla przedwojennego przemysłu Związku Radzieckiego produkcja 8C była procesem złożonym i kosztownym. Udało im się go z powodzeniem opanować tylko w Mariupolu. Skład chemiczny 8C: C - 0,22-0,28%, Mn - 1,0-1,5%, Si - 1,1-1,6%, Cr - 0,7-1,0%, Ni - 1,0-1,5%, Mo - 0,15-0,25%, P - mniej niż 0,035% i S - mniej niż 0,03%. Do wytapiania potrzebne były piece martenowskie o pojemności do 180 ton, wlewające przyszły pancerz do stosunkowo małych form po 7, 4 tony każda. Odtlenianie ciekłego stopu (usunięcie nadmiaru tlenu) w piecu przeprowadzono kosztowną metodą dyfuzyjną z użyciem węgla lub krzemu. Gotowy wlewek wyjęto z formy i walcowano, a następnie powoli schładzano. W przyszłości przyszły pancerz był ponownie podgrzewany do 650-680 stopni i chłodzony powietrzem: był to wysoki urlop, zaprojektowany, aby nadać stali plastyczność i zmniejszyć kruchość. Dopiero potem możliwe było poddanie blach stalowych obróbce mechanicznej, ponieważ późniejsze hartowanie i niskie odpuszczanie w temperaturze 250 stopni spowodowało, że stała się za twarda. W rzeczywistości po końcowym hartowaniu w 8C trudno było zrobić cokolwiek innego niż zespawać z niego korpus. Ale i tutaj pojawiły się zasadnicze trudności. Znaczne wewnętrzne naprężenia spawalnicze wynikające z niskiej ciągliwości metalu pancernego 8C, zwłaszcza przy jego niskiej jakości, prowadzą do powstawania pęknięć, które często narastają z czasem. Pęknięcia wokół szwów mogły powstać nawet 100 dni po wyprodukowaniu zbiornika. Stało się to prawdziwą plagą budowy czołgów Związku Radzieckiego podczas wojny. A w okresie przedwojennym najskuteczniejszym sposobem zapobiegania powstawaniu pęknięć podczas spawania pancerza 8C było zastosowanie wstępnego miejscowego nagrzewania strefy spawania do temperatury 250-280 stopni. W tym celu TsNII-48 opracował specjalne cewki indukcyjne.
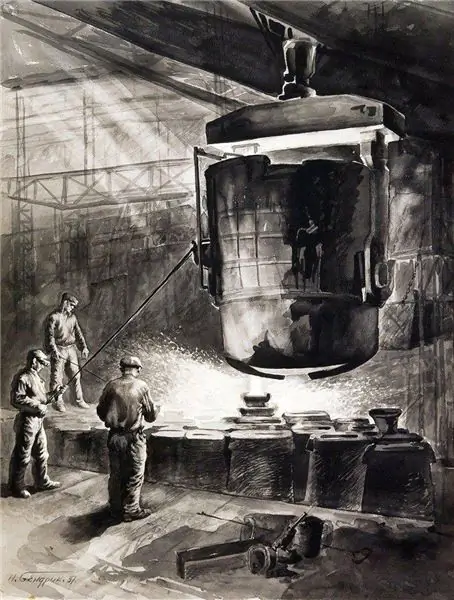
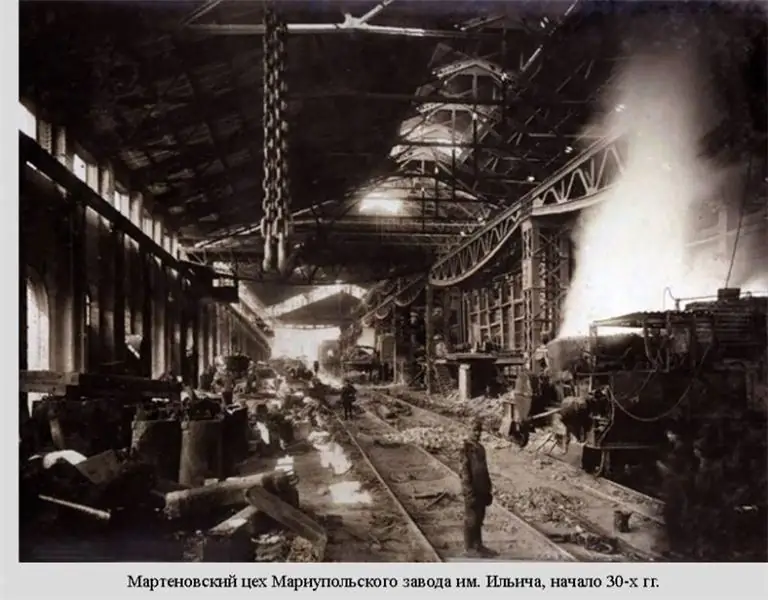
8C nie był jedynym gatunkiem stali na pancerz T-34. Tam, gdzie była okazja, wymieniano ją na inne, tańsze odmiany. W okresie przedwojennym TsNII-48 opracował pancerz strukturalny 2P, którego produkcja znacznie oszczędziła energię i uprościła walcowanie blach. Skład chemiczny 2P: C - 0,23-0,29%, Mn - 1,2-1,6%, Si - 1,2-1,6%, Cr - poniżej 0,3%, Ni - poniżej 0,5%, Mo - 0,15-0,25%, P - mniej niż 0,035% i S - mniej niż 0,03%. Jak widać, główne oszczędności dotyczyły deficytowego niklu i chromu. Jednocześnie bardzo wąskie tolerancje na obecność fosforu i siarki pozostały niezmienione dla 2P, co oczywiście było trudne do osiągnięcia, zwłaszcza w czasie wojny. Mimo wszystkich uproszczeń, pancerze konstrukcyjne wykonane ze stali 2P nadal poddawane były obróbce cieplnej - hartowaniu i wysokiemu odpuszczaniu, co znacznie obciążyło urządzenia cieplne niezbędne do obróbki cieplnej bardziej krytycznych części pancerzy czołgów, a także znacznie zwiększyło cykl produkcyjny. W czasie wojny specjaliści TsNII-48 byli w stanie opracować technologie otrzymywania podobnych stali, których produkcja uwolniła zasoby na główny pancerz 8C.